Важные аспекты формирования клеевых соединений фанеры
В производстве фанеры нередки случаи, когда пуск в производство новой партии смолы приводит к появлению пузырей, хотя, казалось бы, все технологические параметры находятся в норме. Рассмотрим причины, по которым это может происходить – и то, как можно контролировать кинетику прочности клеевых слоев фанеры при горячем склеивании.
При склеивании слоев фанеры принято выделять три основные стадии формирования клеевых соединений. В течение первой стадии с момента нанесения клея на поверхность шпона происходит растекание клеевого состава, смачивание шпона и макрореологическое затекание клея в перерезанную клеточную структуру древесины шпона, поглощение этой структурой воды и низкомолекулярных фракций из клеевого слоя. Величина адгезии жидких карбамидо- и фенолоформальдегидных смол к древесине, как правило, превышает их когезионную прочность, которую еще называют липкостью клея. Этот показатель очень важен для обеспечения качественной подпрессовки пакетов фанеры.
Вторая стадия протекает с образованием сетчатой структуры клея, в результате чего повышаются его когезионная прочность и прочность соединения слоев шпона.
В течение третьей стадии, после операции горячего прессования, когезионная прочность клея продолжает медленно повышаться за счет увеличения плотности его пространственной сетки. Рост прочности системы «клей-древесина» продолжается до тех пор, пока когезионная прочность клея не превысит когезионную прочность древесины или межфазного слоя.
Дальнейшее повышение когезионной прочности клея может уже не влиять на прочность соединения или оказывать на нее отрицательное влияние по причине увеличения напряжений в клеевом слое. Поэтому считается, что качественное склеивание гарантируется, если когезионная прочность клея равна когезионной прочности древесины.
Современные интенсифицированные режимы склеивания фанеры ориентированы на достижение минимума когезионной прочности клея, при котором обеспечивается целостность клеевого соединения после раскрытия плит пресса, согласно условию:
Руд + s’ ≥ Ризб + sупр,
где Руд – удельное давление прессования, Ризб – избыточное давление парогазовой смеси в фанерном пакете, а sупр – напряжение от деформации упругого восстановления пакета. Если это условие не выполняется, т. е. величина s’ на момент раскрытия плит пресса оказывается меньше суммы избыточного давления парогазовой смеси и напряжений от деформации упругого восстановления пакета, в фанере образуется пузырь.
Изучая причины появления пузырей, многие исследователи сошлись во мнении, что для оптимизации режимов склеивания фанеры и ДСтП при разработке новых смол и клеевых рецептур требуется метод, позволяющий оценить кинетику прочности клеевых соединений s’ непосредственно в процессе горячего прессования.
Научные публикации об исследованиях кинетики прочности соединений на клеях горячего отверждения появились не так давно, так как для определения прочности клеевых соединений непосредственно в процессе склеивания требуется довольно сложное нестандартное испытательное оборудование. Как правило, это специальные устройства, выполненные в виде малогабаритных нагревательных плит с захватами для образцов материалов, монтируемые на машину для испытаний – своего рода миниатюрные прессы, позволяющие проводить испытания по единому циклу: склеивание – определение прочности клеевого соединения.
В Центральном научно-исследовательском институте фанеры (ЦНИИФ) еще в 1960 году был разработан метод определения прочности клеевых соединений шпона на сдвиг непосредственно после размыкания плит пресса. Однако преимущественное распространение при изучении кинетики прочности клеевых соединений шпона получила схема испытания на нормальный отрыв. Основанием для использования этой схемы испытания является то, что в момент размыкания плит пресса клеевые соединения фанеры работают на нормальный отрыв, так как напряжения от избыточного парогазового давления и напряжения, вызванные деформацией упругого восстановления пакета, действуют перпендикулярно плоскости склеивания.
Большой вклад в изучение кинетики прочности смол и клеев внесли научные сотрудники Сибирского технологического института (СТИ; с 1997 года – Сибирский государственный технологический университет, СибГТУ) в г. Красноярске. Метод нормального отрыва был использован Светланой Денисовой в 1975 году при исследовании когезионной прочности карбамидоформальдегидных смол при склеивании тонких пластинок строганого шпона лиственницы. Начиная со второй половины 1980-х годов появляются многочисленные отечественные и зарубежные работы по изучению кинетики прочности смол и клеев горячего отверждения.
В этих работах условия, при которых проводились исследования, соответствовали условиям краевой зоны пакета шпона промышленного формата при горячем прессовании.
Уже в то время по формату склеиваемого горячим способом пакета шпона было принято выделять две характерные по термовлажностным условиям зоны – краевую и серединную. Интенсивность прогрева краевой зоны по сравнению с серединной заметно меньше, что является следствием потерь тепла на испарение влаги через кромки пакета. Из серединной зоны пакета удаления влаги почти не происходит, так как гидродинамическое сопротивление выходу пара шпона краевой зоны довольно велико. Первоначально считалось, что в краевой зоне условия для формирования клеевых соединений наименее благоприятные вследствие более низкой, чем в серединной зоне, температуры прогрева.
Основным дефектом склеивания фанеры является локальное расслоение – образование пузыря в области серединной зоны. Пузырь образуется сразу после размыкания плит пресса, если нерелаксировавшиеся к этому времени силы упругого сопротивления пакета и внутреннего парогазового давления оказываются выше когезионной прочности клея. Поэтому исследователями был сделан закономерный вывод, что основная причина появления пузырей – высокое давление парогазовой смеси в серединной зоне на момент раскрытия плит пресса.
Изучая закономерности изменения парогазового давления и сопоставив полученные значения со значениями прочности клеевых соединений для условий краевой зоны, Владимир Ворошилов из СТИ обратил внимание на то, что величина избыточного парогазового давления Ризб не настолько велика, чтобы вызвать разрушение образующихся клеевых связей. Проанализировав характер разрушения, он пришел к выводу, что причиной образования пузырей является недостаточная когезионная прочность смолы вследствие замедленного характера процесса отверждения в условиях серединной зоны.
В то время экспериментально оценить закономерности нарастания когезионной прочности клея в условиях серединной зоны не представлялось возможным из-за отсутствия методик и технических средств для их реализации. Поэтому о кинетике прочности клеевых соединений в серединной зоне судили по результатам исследования процесса отверждения в герметичных условиях, исходя из того, что в клеевых слоях серединной зоны и в герметичном объеме отверждение протекает без удаления воды.
Используя ИК- и УФ-спектроскопию, дифференциальносканирующую калориметрию, ультразвуковые и реологические методы, американские и советские ученые (С. Чоу, Валерий Тамбовский, Петр Белимов и др.) установили, что в герметичных условиях интенсивность процесса отверждения поликонденсационных карбамидо- и фенолоформальдегидных смол значительно снижается. С. Чоу, исследуя процесс отверждения фенолоформальдегидных смол в запаянных ампулах, обратил внимание на существование индукционного периода отверждения, в течение которого свойства смолы остаются неизменными. Он предположил, что вода выступает в роли энергетического барьера, сдерживающего реакцию поликонденсации.
В. Тамбовский, изучая отверждение вискозиметрическим методом фенолоформальдегидных смол, находящихся в герметичных условиях, установил, что отверждение смол без удаления воды протекает очень медленно, почти без изменения их вязкости.
На основании этих исследований было выдвинуто предположение о замедленном отверждении и росте когезионной прочности клея в серединной зоне склеиваемого пакета фанеры.
В. Ворошилов пытался экспериментально исследовать кинетику прочности клеевых соединений в серединной зоне, склеивая модельный пакет шпона в герметичной камере. Но влага из прессуемого модельного пакета испарялась в герметизируемый объем и, как признал сам ученый, условия эксперимента не соответствовали условиям серединной зоны.
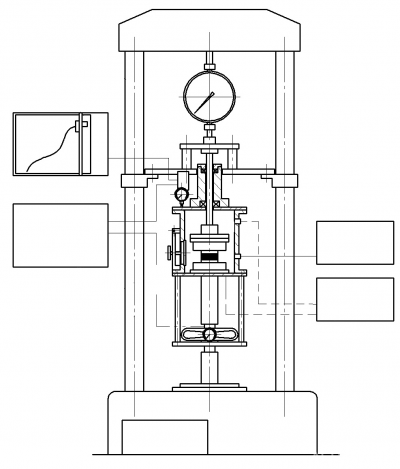
Наибольшего соответствия термовлажностных условий реальным процессам, протекающим в серединной зоне пакета промышленного формата, удалось достигнуть при склеивании модельного пакета шпона в герметичном объеме под избыточным давлением воздуха, что позволило исключить удаление влаги через кромки пакета. Установка (рис. 1), реализующая такой принцип моделирования, была создана в 1979 году Геннадием Орловым в Сибирском технологическом институте (авторское свидетельство 1656415) г. Красноярска.
Герметичная камера установки установлена на стойках испытательной машины. Для измерения нагрузки растяжения использовался динамометр типа ДПУ-0,2. Узел задачи и контроля давления прессования состоит из динамометра сжатия типа ДС. Модельный пакет шпона необходимой толщины и слойности фиксировался на нагревательных плитах. Загрузка пакета осуществлялась через окно, закрываемое герметизирующей задвижкой. Для фиксации разрушения по необходимому слою при сборке пакета в него закладывалось кольцо из термостойкой полиэтиленовой пленки. Для записи диаграммы «деформация – давление прессования» использовался двухкоординатный самописец. Испытание по непрерывному циклу «сжатие (прессование) – растяжение» осуществлялось в автоматическом режиме, для чего использовался блок автоматики. Установка была снабжена системой моделирования термовлажностных условий серединной зоны, включающей в себя систему управляемых вентилей, манометры, компрессор и узел подачи воды. Температура нагревательных плит регулировадась терморегуляторами. Конструкцией захватов экспериментальной установки было предусмотрено использование круглых образцов шпона, что позволяло повысить равномерность распределения напряжений в клеевом слое, исключив в определенной степени влияние силы расслаивания. Модельный пакет шпона формировался из образцов диаметром 60 мм.
Испытания осуществлялись следующим образом. На образцы шпона кистью наносили клей и формировали модельный пакет необходимой слойности, который помещали на нагревательные плиты установки. Затем закрывали герметизирующую задвижку и включали систему автоматического управления режимом испытания. По достижении номинального давления прессования в камере создавалось избыточное давление воздуха. После истечения заданного времени прессования силонагружатель установки включался на растяжение и по динамометру считывали разрушающую нагрузку. Затем сбрасывали давление воздуха в камере, открывали загрузочное окно и вынимали из захватов части модельного пакета шпона.
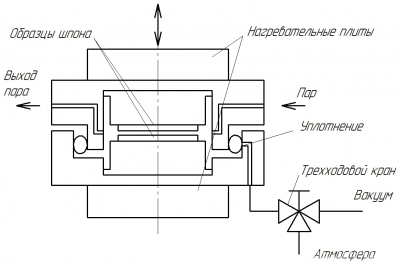
Похожая установка была создана Филиппом Хэмфри (США) только в 1988 году. Схема испытательной камеры установки приведена на рис. 2. Образцы шпона приклеивались эпоксидной смолой к алюминиевым дискам, которые крепились на миниатюрные нагревательные плиты. Герметизация достигалась благодаря использованию кольцевого трубчатого силиконового уплотнения в зазоре между плитами. Как и в установке Г. Орлова, моделирование термовлажностных условий серединной зоны достигалось подачей пара в герметизируемый объем камеры.
Неоспоримое преимущество установки Г. Орлова – возможность использования модельного пакета шпона любой слойности и толщины. Кроме того, в установке Ф. Хэмфри перед определением прочности давление пара в камере необходимо было сбрасывать, что снижало корректность полученных значений прочности из-за интенсивного доотверждения смолы.
Исследования, проведенные в СТИ, показали, что процессы формирования клеевых соединений в краевой и серединной зонах фанерного пакета существенно различаются. Установлено, что в краевой зоне показатель s’ для фенолоформальдегидных смол начинает расти при температуре 95–100°С, в серединной зоне – при температуре на 5–10°С выше.
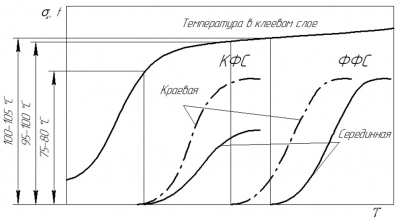
Склеивание шпона в краевой зоне сопровождается интенсивным удалением влаги в виде пара через кромки пакета. При моделировании серединной зоны влага почти не удаляется. Из наружных слоев, которые ближе к нагревательным плитам, она перемещается в центральные, конденсируясь в них. Поэтому к моменту достижения температуры 95–100°С количество влаги еще так велико, что оказывает заметное тормозящее влияние на процесс отверждения фенолоформальдегидной смолы.
Карбамидоформальдегидные смолы отверждаются при 70–90°С. При этих значениях температуры различие в термовлажностном состоянии шпона в характерных зонах еще не столь существенно, поэтому процесс отверждения (гелеобразования) с одновременным ростом когезионной прочности смолы начинается в краевой и серединной зонах при одинаковой продолжительности склеивания. В краевой зоне прочность s’ увеличивается, по сути, линейно, вплоть до момента изменения характера разрушения с когезионного по клею на когезионный по древесине.
В условиях серединной зоны разрушение клеевых соединений на карбамидоформальдегидной смоле происходит преимущественно по клею.
Отдельные партии смол можно идентифицировать по кинетике показателя s’. Причем в условиях серединной зоны при затрудненном удалении воды из клеевого слоя различия в характере кинетических зависимостей проявляются гораздо отчетливее, чем в условиях, отвечающих условиям краевой зоны пакета промышленного формата.
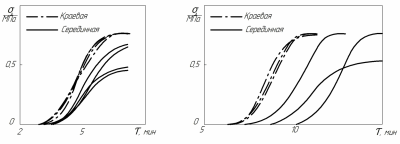
Неоднородность партий фенолоформальдегидных смол проявляется в различной продолжительности до начала роста (момента, когда показатель начинает фиксироваться) и скорости нарастания прочности s’. Для карбамидных партии смол различались только в скорости нарастания прочности s’.
Полученные результаты свидетельствуют о том, что смолы с практически одинаковыми физическими и физико-химическими показателями (которые соответствуют требованиям ГОСТ) в неблагоприятных условиях, при отсутствии свободного удаления растворителя – воды и низкомолекулярных продуктов из сферы реакции – могут отверждаться в клеевых слоях фанеры с различной интенсивностью. При использовании партии смолы с замедленным отверждением, когезионная прочность клеевого слоя на момент раскрытия плит пресса не успеет достичь прочности, достаточной для обеспечения целостности клеевого слоя. Избыточное давление парогазовой смеси разрушит клеевой слой с образованием пузыря. Приходится в экстренном порядке увеличивать продолжительность прессования или снижать температуру плит.
На основании вышеизложенного можно сделать вывод, что разработку новых клеевых составов, работы по оптимизации режимов склеивания, испытание клеящих свойств карбамидо- и фенолоформальдегидных смол следует проводить, ориентируясь на термовлажностные условия серединной зоны склеиваемых пакетов шпона как наименее благоприятные для формирования клеевых соединений.
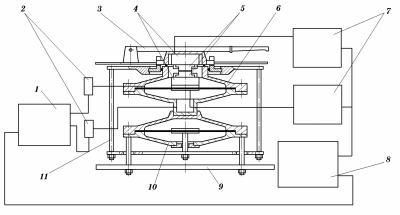
Прибор для оценки кинетики прочности синтетических смол и клеев горячего отверждения в условиях серединной зоны склеиваемого пакета шпона был разработан и изготовлен Александром Филипповичем в СТИ г. Красноярска в 1989 г. (авторское свидетельство 1538105, патент РФ 2045754). Принципиальная схема прибора приведена на рис. 5.
Прибор обеспечивает склеивание и последующее определение прочности клеевого соединения в автоматическом режиме с индикацией результатов в цифровом виде. Конструктивно он состоит из блоков управления, регулирования, силового, аналогоцифрового преобразователя и пневматической панели.
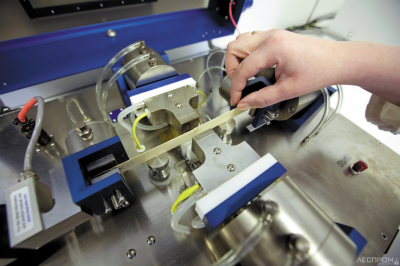
Позже аналогичный по назначению прибор был разработан в США Филиппом Хэмфри на базе его исследований конца 90-х. Склеивание полосок шпона осуществлялось между миниатюрными нагревательными плитами. Зажим образцов, усилие прессования и создание растягивающего усилия осуществлялись посредством пневмоцилиндров. Однако для упрощения конструкции Ф. Хэмфри отказался от герметичной камеры, сведя все достоинства метода на нет, так как склеивание и испытание образцов в приборе осуществлялось при свободном удалении влаги из клеевого слоя, т. е. в условиях краевой зоны.
К сожалению, более функционально совершенный отечественный прибор, созданный в двух экземплярах, так и остался перспективной разработкой, в то время как Ф. Хэмфри наладил серийное производство своего прибора в США. Метод, названный им ABES (от Automated Bonding Evaluation System, то есть «Автоматизированная система оценки склеивания») получил широкое распространение при исследовании клеев горячего отверждения, используемых в производстве фанеры, MDF и других материалов.
Александр Филиппович