Планирование на предприятиях ЛПК. Часть 9
Оперативное планирование производства
Часть 1. Внутрипроизводственное планирование: сущность, содержание, принципы, методы, показатели
Часть 2. Планирование производственной программы
Часть 3. Анализ выполнения производственной программы
Часть 4. Планирование труда и заработной платы
Часть 5. Планирование себестоимости лесопродукции
Часть 6. Финансовое планирование
Часть 7. Анализ выполнения плана по себестоимости, прибыли и рентабельности
Часть 8. Планирование природоохранной деятельности
Часть 9. Оперативное планирование производства
Часть 10. Бизнес-планирование
Как свидетельствует передовой опыт, разработка оперативных планов производства обеспечивает слаженную работу всех структурных подразделений предприятий ЛПК и полное использование их производственного потенциала.
Оперативное планирование нацелено на ритмичный выпуск продукции, экономное расходование ресурсов, слаженность всех производственных процессов, снижение доли брака и охрану труда работников и окружающей среды. Таким образом, оперативно-производственное планирование способствует росту производства и повышению его эффективности в условиях рыночных отношений.
Разработка оперативных планов производства (ОПП) является завершающим и ответственным звеном плановой работы предприятия. Она заключается в детализации текущих планов во времени (месяц, декада, сутки, смена) и пространстве (цехи, производственные участки, рабочие места). Сюда также следует отнести оперативный контроль и регулирование производства.
Оперативно-производственное планирование призвано обеспечить решение большого круга задач, в числе которых следующие основные:
- оптимальная загрузка оборудования, производственных площадей, рабочих мест;
- соблюдение установленных договорами сроков поставки готовой продукции;
- обеспечение ритмичности выполнения производственных плановых заданий, достижение согласованной работы всех звеньев производства;
- конкретизация и доведение заданий до отдельных структурных подразделений предприятия с указанием сроков их выполнения;
- составление графиков движения предметов труда и доведение их до исполнителей;
- экономное расходование производственных ресурсов;
- выполнение производственной программы по количеству и качеству выпускаемой продукции;
- сокращение длительности производственных циклов и размеров незавершенного производства;
Для выполнения этих и других задач оперативно-производственное планирование наделено многими функциями (рис. 1).
Для разработки оперативных планов прежде всего необходимо дифференцировать ОПП на межцеховое и внутрицеховое. Межцеховое ОПП осуществляется в общепроизводственном масштабе, а внутрипроизводственное оперативное планирование – в рамках отдельных структурных подразделений предприятия. При этом перечень показателей работы цехов в оперативном плане зависит от характера производства и специфики работы цеха. На предприятиях ЛПК важным показателем ОПП является выпуск продукции в натуральном выражении в соответствии с договорами и с учетом наиболее полного использования оборудования (аппаратов).
Для предприятий ЛПК характерны три системы организации ОПП: подетальная, позаказная, полуфабрикатная. Первые две распространены на мебельных и столярно-механических производствах, а последняя – на лесопильном, фанерном, целлюлозно-бумажном и лесохимическом. Наиболее сложной является подетальная система, используемая при относительно устойчивом ассортименте продукции и позволяющая наиболее обоснованно и тщательно осуществлять и регулировать производство. При этом достигается ритмичный выпуск продукции и высокие технико-экономические показатели.
Позаказная система зачастую требует особых форм планирования и учета по каждому заказу, ограничивает использование единых форм, но она менее ограничена по срокам выпуска и комплектности продукции. Полуфабрикатная система проста в части планирования и контроля, но сложна в выпуске продукции по спецификациям, так как эта задача зависит от размерно-качественной характеристики обрабатываемого сырья. Рассмотрим этот вопрос на примере лесопиления, оперативно-производственное планирование в котором непосредственно связано с выполнением спецификации пилопродукции, наиболее полным использованием сырья и основных видов оборудования. На лесопильных заводах основной продукцией являются пиломатериалы разных размерно-качественных характеристик (обрезные, необрезные, хвойные, лиственные, твердолиственные, разной размерности и сортности). В качестве основного оборудования выступают лесопильные рамы и фрезернопильные агрегаты (ФПА, ЛАПБ и др.).
Организация технологического процесса строится по потокам (обычно развальный, брусовый и фрезернопильный). При оперативно-производственном планировании лесопильному цеху, помимо спецификационного задания, устанавливается объем выпуска пиломатериалов по месяцам, сменам, суткам. Обычно действует бригадный метод организации труда и задания выдаются каждой бригаде.
Такие бригады охватывают всех рабочих одной смены. Сначала разрабатывается график работы бригад, а затем месячное задание распределяется по бригадам (табл. 1).
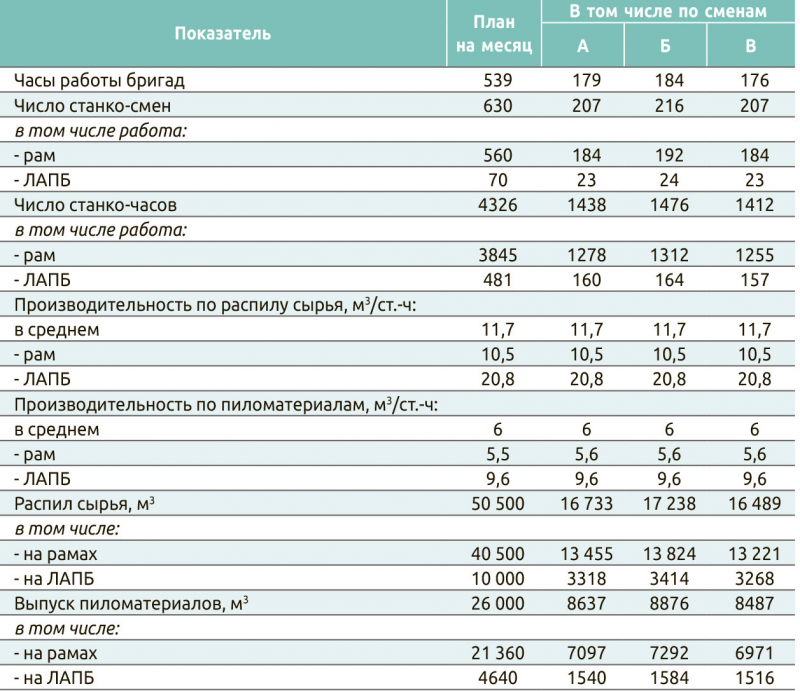
Содержание оперативно-производственного планирования в фанерном производстве примерно такое же, как в лесопильном в части формирования и реализации спецификации продукции, более полного использования оборудования и сырья. Основной продукцией фанерного производства является фанера обычного потребления, экспортная фанера, товарный лущеный и строганый шпон, фанера специального назначения, гнутоклееные детали; прочие виды фанерной продукции; технологическая щепа. Ассортимент фанерной продукции значительно шире, чем лесопильной.
В спецификациях (стокнотах) отражают формат и толщину фанеры (шпона), ее сортность, породный состав древесины, объем выпуска. Главным структурным звеном, на которое ориентируется в работе остальные структурные подразделения предприятия в части спецификации, объемов и сроков выпуска продукции, служит клеильный цех, а при выпуске товарного шпона – сушильный цех. Формирование заданий другим цехам идет в обратной последовательности технологического процесса, начиная с клеильного цеха.
Основным видом оборудования в клеильном цехе служат различные клеильные прессы, которые в совокупности с другими видами оборудования и транспортными средствами образуют линии склеивания шпона. Из этих линий выходит необрезная фанера, которая затем поступает на обрезные станки и выходит в виде обрезной фанеры.
Для предприятий целлюлозно-бумажной и лесохимической переработки древесины, на которых действует полуфабрикатная система организации ООП, важное значение имеет учет тесных взаимосвязей технологических процессов основных производственных цехов и строгая согласованность изготовления полуфабрикатов и готовой продукции. Например, объем выпуска дрожжей в целлюлозном производстве зависит от количества сульфитного щелока. Выпуск белкового концентрата из послеспиртовой барды зависит от объема выпуска этилового спирта, производственное задание по выпуску синтетической камфары зависит от производства живичного скипидара, и т. д. Примером может служить оперативный план производства этилового спирта (табл. 2).
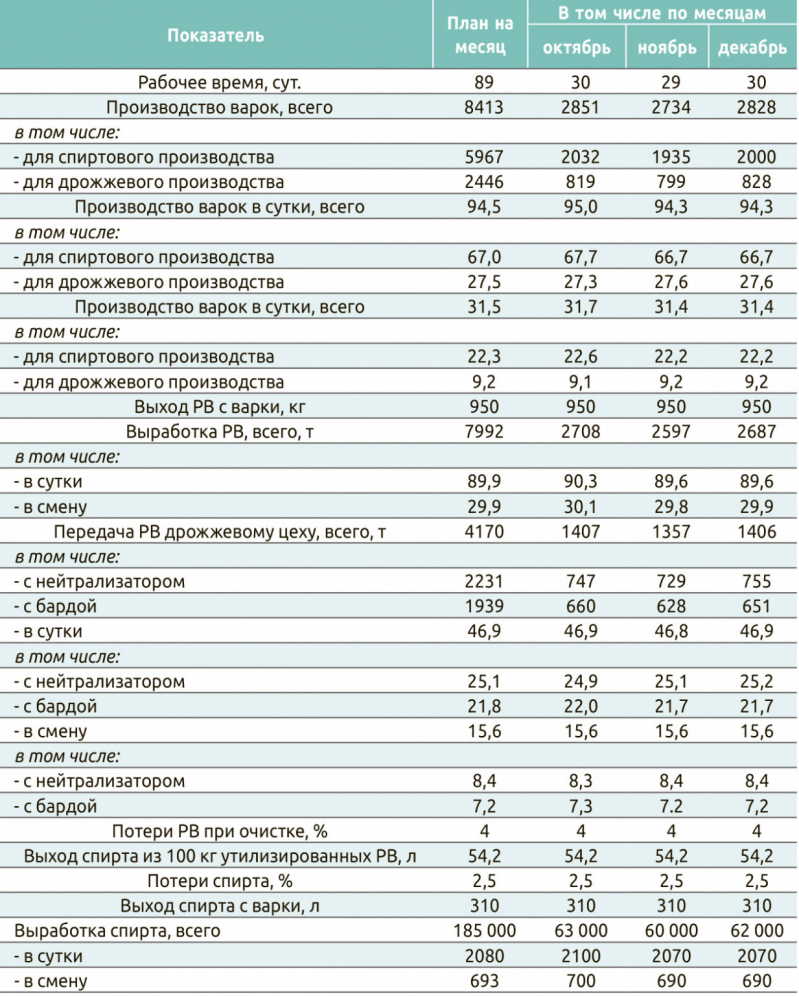
В мебельном производстве, для которого характерна подетальная система оперативно-производственного планирования, сложнее разрабатывать ОПП, чем для других деревообрабатывающих и лесохимических производств, что обусловлено широким ассортиментом изделий мебели и обрабатываемых деталей, большим разнообразием используемого оборудования (позиционные станки, поточные линии, автоматы и полуавтоматы), широкий номенклатурой обрабатываемого сырья и материалов. Оперативно-производственное планирование включает в себя расчеты различных норм и нормативов по цехам, видам оборудования и продукции, длительности производственного и технологического циклов, величины серий и партий изделий (деталей), незавершенного производства, норм использования и загрузки оборудования и др.
Оперативные планы цехам устанавливают с учетом месячной программы выпуска изделий, заделов, опережений и длительности производственного цикла. Расчеты ведут в последовательности, обратной ходу технологического процесса, то есть план сборочного цеха составляют исходя из месячного плана выпуска продукции по предприятию, месячный план отделочного цеха – исходя из месячного плана и необходимости сохранения определенного задела сборочного цеха; месячный план машинного цеха – из плана необходимости сохранения задела отделочного цеха, и т. д. Планы цехам устанавливают как по выпуску, так и по запуску комплектов изделий.
Пример 1. Машинный цех должен ежемесячно выпускать 1000 комплектов столов и при производственном цикле восемь дней иметь задел 320 комплектов при средних потерях по материальному браку 40 комплектов; задел на начало месяца 300 комплектов. В этом случае план на следующий месяц составит 1000 + 20 + 40 = 1060 комплектов столов. Если задел на начало месяца будет больше норматива (предположим, 380 комплектов), план по запуску на следующий месяц будет уменьшен на количество, превышающее норматив, то есть он составит 1000 - 60 + 40 = 980 комплектов, а план выпуска и передачи в сборочный цех будет сохранен в объеме 1000 комплектов столов.
Как правило, план выпуска комплектов машиного цеха должен быть равен плану запуска комплектов последующего цеха. Рассмотренный порядок составления месячных планов цехов применяется в отношении изделий, изготовляемым постоянно. Когда предприятия и цеха приступают к выпуску новых изделий, по ним используется другой порядок составления месячных планов цехов. В этом случае планы сопряженных цехов будут значительно отличаться по числу изделий и срокам их запуска и выпуска. Работы в заготовительном цехе начнутся позже, чем в сборочном, так как изделия сначала должны пройти производственный цикл в заготовительном, сушильном, машинном и отделочном цехах.
Пример 2. Предприятие с марта приступает к выпуску шкафов новой конструкции. В первый месяц должно быть выпущено 400 шкафов, а в последующие месяцы по 1000, в среднем 40 шкафов в день. Длительность производственного цикла в заготовительно-сушильном цехе составляет восемь дней, в машинно-фанеровочном – 12, в отделочном – три, сборочном – четыре дня. Необходимо установить план работы по отдельным цехам, начало выпуска и запуска первой партии в заготовительном цехе (табл. 3). Составление плана начинается со сборочного цеха с учетом режима работы.
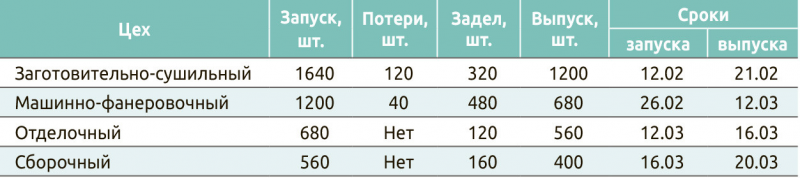
На основании месячного плана по цехам разрабатывают сменно-суточные задания. Оперативные планы цехов оформляют в виде графиков запуска, выпуска, заделов деталей (изделий), а также их комплектности.
В мебельном производстве большое значение придается подбору серий изделий и партий деталей (изделий). При серийном производстве выпуск изделий планируется сериями. Серия – это число конструктивно одинаковых изделий, которые изготовляют за установленное время, после чего выпуск этих изделий временно или совсем прекращается. Величина серии изделия устанавливается с учетом требований потребителей, сроков выпуска изделий, производственных возможностей предприятия, числа и видов других изготовляемых изделий, условий обеспечения сырьем и материалами.
Серию изделия разбивают на партии. Партия изделий (деталей) – это число одинаковых изделий (деталей), одновременно запускаемых в производство и непрерывно обрабатываемых на одних и тех же рабочих местах при однократной наладке оборудования (линий).
В серийном производстве партии деталей обрабатывают на каждом рабочем месте при последовательном чередовании с другими партиями деталей этого же изделия или других изделий. Переход к обработке другой партии деталей на этом рабочем месте связан с переналадкой оборудования. Принятый для запуска в производство размер партии деталей важен для работы предприятия. С увеличением размера партии сокращаются затраты на переналадку и повышаются степень использования оборудования и производительность труда. Вместе с тем требуется увеличение запаса деталей на рабочих местах и складах, удлиняется производственный цикл, увеличивается потребность в запасах материалов и производственных площадях. Чрезмерное сокращение партий приводит к обратным результатам. Поэтому стремятся рассчитывать оптимальные партии деталей.
Для бесперебойного функцирнирования всех рабочих мест цеха необходимо иметь заделы деталей (полуфабрикатов) для каждой операции. Заделом называется число изделий, не законченных производством на каждом рабочем месте. Заделы различают цикловые и страховые. Цикловые заделы зависят от среднесуточной потребности в деталях и производственного цикла и определяются по формуле
Зц = Пср Тц,
где Зц – цикловой задел деталей, шт.; Тц – длительность производственного цикла, дней; Пср – среднесуточная потребность в деталях, шт. Общий задел определяется по формуле
Зобщ = Пср Тц + Зстр,
где Зстр – страховой задел.
Незавершенным производством называют денежное выражение заделов. Объем незавершенного производства (в рублях) зависит от размера заделов и их себестоимости. Таким образом, сумма незавершенного производства зависит от длительности производственного цикла, среднесуточной потребности в деталях (полуфабрикатах) и себестоимости применяемых изделий (полуфабрикатов). Себестоимость задела (полуфабриката) зависит от коэффициента нарастания затрат, связанных с изготовлением изделия. Под этим коэффициентом понимают отношение средней себестоимости одной единицы незавершенного изделия, находящегося в заделе, к полной его себестоимости. При изготовлении продукции затраты на производство растут постепенно: по мере выполнения каждой технологической операции изделие (полуфабрикат) становится дороже. Для упрощенных расчетов обычно коэффициент нарастания затрат принимают равным 0,5. Это значит, что себестоимость каждого изделия (детали, полуфабриката), находящегося в заделе, равна примерно половине себестоимости готового изделия (детали, полуфабриката).
Таким образом, средний размер оборотных средств по каждому изделию в незавершенном производстве S может быть определен по формуле
Тпл где Aпл – планируемый выпуск изделия, шт.; Сед – себестоимость изделия, руб.; Тпл – длительность планируемого периода, по которому учтен выпуск продукции (360, 90, 30 дней); Тц – длительность производственного цикла, дней; Кн – коэффициент нарастания затрат.
На некоторых предприятиях ЛПК применяется позаказная система оперативно-производственного планирования (в основном в единичном производстве) с разнообразной номенклатурой и небольшим объемом выпускаемой продукции и производственных услуг (различные виды мебели, столярных изделий, музыкальных инструментов, запасных частей для ремонта и т. д.). В этом случае объектом планирования, то есть основной планово-учетной единицей, является отдельный производственный заказ, включающий несколько однотипных работ конкретного потребителя-заказчика. Такая система планирования основана на расчетах длительности производственных циклов и нормативов опережения, с помощью которых устанавливаются требуемые заказчиком или рынком сроки выполнения как отдельных процессов или работ, так и заказа в целом.
Главная задача оперативно-производственного планирования – обеспечение ритмичности производства. Ритмичная работа является одним из важнейших условий рационального использования живого труда и производственных ресурсов. Особенно велико значение этого фактора на современном этапе развития. Чем сложнее техника на предприятии, тем актуальнее обеспечение ритмичности производства, поскольку малейшие перебои в работе высокопроизводительного оборудования вызывают большие потери. Нарушение ритмичности производства приводит к срыву плана поставок по договорам. Неритмичная работа дезорганизует производство, приводит к сверхурочным работам, перерасходу заработной платы.
Основные причины неритмичной работы: несоответствие пропускной способности оборудования по участкам, цехам, появление узких мест, некомплектность заделов, внеплановые простои оборудования, недостатки в организации производства, труда, планирования; перебои в материально-техническом снабжении, низкая трудовая и производственная дисциплина.
На практике для оценки ритмичности производства используется несколько методов. Самым общим показателем ритмичности производства является удельный вес выпуска продукции за декаду по отношению к месячному плану:
где Ад, Ам – фактический выпуск продукции по плану за декаду и месяц соответственно, тыс. руб.
Недостаток этого показателя в том, что он не учитывает количество рабочих дней по декадам, выполнение планового графика выпуска продукции.
Более достоверно оценить уровень ритмичности производства можно с помощью коэффициента ритмичности выпуска продукции Кр. Этот коэффициент определяется как частное суммы фактического выпуска продукции за сутки в пределах плана и суммы планового выпуска за сутки:
где Аф – фактический выпуск продукции за сутки планового задания; Ап – плановое задание за сутки; Ан – недовыполнение плана по выпуску продукции в отдельные периоды времени (сутки).
Пусть на предприятии выпуск продукции характеризуется данными приведенными в табл. 4.

Тогда план по объему производства выполнен на 100%: (520/520×100).
Коэффициент ритмичности равен Кр = (95 + 105 + 90 + 105 + 115)/520 = 510/520 = 0,98 , или Кр = 1 - 10/520 = 0,98.
Преимуществом этого метода расчета состоит в том, что он базируется на плановом графике выпуска продукции. Коэффициент ритмичности может рассчитываться по выполнению не только суточного, но и сменного, часового, декадного графиков.
Точность и обоснованность оперативного планирования в значительной степени зависят от качества используемых нормативов организации производства, характеризирующих наиболее рациональные соотношения основных элементов трудовых, технологических и производственных процессов, а также расход ресурсов по всем стадиям обработки (переработки). К ним относится такие показатели, как длительность производственного цикла, размеры партий запуска-выпуска изделий, величина производственных заделов (запасов) заготовок, время наладки и переналадки оборудования и др.
Важные нормативные показатели ОПП – производственные и технологические циклы. От их величины зависят сроки и комплектность выпуска продукции, ритмичность производства, выполнение ассортиментного плана, производительность труда, размер незавершенного производства. Длительность производственного цикла рассчитывают по столярно-механическим производствам: мебельному, музыкальных инструментов, оконных и дверных блоков, стандартного домостроения.
Длительность технологического (Ттех) и производственного (Тц) циклов в общем виде определяют по формулам:
Ттех = Тос + Твс + Тмо + Тв и Тц = Ттех + Трв + Тпр ,
где Тос – длительность основных технологических операций; Твс – длительность вспомогательных операций; Тмо – межоперационные перерывы; Тв – технологические выдержки; Трв – перерывы, обусловленные режимом рабочего времени (нерабочие смены и дни, обеденные и другие регламентированные перерывы); Тпр – прочие перерывы, связанные с нарушениями организации производства: отключением электроэнергии, несвоевременным обеспечением материалами, инструментами и др. (в плановых расчетах не учитывается).
В свою очередь, длительность технологических операций зависит от нормативной продолжительности каждой операции, величины партии деталей (изделий), процента выполнения норм выработки, числа рабочих мест на одноименных операциях, размера передаточных партий деталей (изделий) и последовательности выполнения операций. Технологические перерывы зависят он нормативной выдержки и сменности работы цеха. От уровня специализации технологических процессов зависят межоперационные перерывы. Режимные перерывы зависят от времени выдерживания деталей (изделий) без обработки между сменами, в выходные и праздничные дни (в прерывных производствах).
На производство влияет много факторов. Некоторые из них необходимо заранее выявлять, чтобы предупреждать их отрицательное воздействие, иначе они неизбежно приведут к нарушению выполнения производственной программы. То есть необходим постоянный текущий контроль за ходом производства, выявление факторов, которые могут отрицательно повлиять на него, и принятие мер по регулированию производства. Непрерывное, оперативное наблюдение, контроль и текущее регулирование производственного процесса для обеспечения своевременного и полного выполнения плана выпуска и реализации продукции в соответствии с договорами и заказами принято называть диспетчированием.
При диспетчировании ведется оперативный учет фактического хода выполнения разработанных производственных планов-графиков выпуска продукции, ее количество, комплектность, выявляются отклонения фактических показателей хода производства товаров и услуг от плановых, принимаются оперативные решения по предупреждению и устранению отклонений и перебоев в ходе производства, анализируются причины отклонений от установленных планов-заданий и разрабатываются меры по их ликвидации, координируются работы сопряженных подразделений предприятия, включая объекты вспомогательного производства, устраняются последствия отклонений от нормального хода производства.
Таким образом, диспетчирование должно носить предупредительный характер, заключающийся в заблаговременном выявлении и своевременном устранении намечающихся отклонений от установленных планов-графиков и текущих заданий.
Для правильного и эффективного диспетчирования производства необходимо соблюдение следующих условий:
- диспетчирование должно базироваться на обоснованных производственных программах, заданиях и календарных планах-графиках;
- диспетчерский контроль за ходом производства должен осуществляться на основе данных оперативного учета и точной оперативной информации о фактическом выполнении работ;
- диспетчерская служба должна быть оснащена необходимыми техническими средствами, повышающими ее оперативность;
- персонал диспетчерской службы должен быть наделен достаточными полномочиями по текущему регулированию хода производства.
При несоблюдении этих условий диспетчирование может быть сведено к простой регистрации неполадок без устранения причин, нарушающих планы-графики и вызывающих штурмовщину в работе.
Текст Владимир Мосягин, д-р экон. наук, профессор СПбГЛТУ