Ресурсосберегающая технология переработки макулатуры. Часть 7
Фракционирование и дополнительный размол
Продолжение. Начало в № № 3, 5−8 2006 г., № 1 2007 г.
В России объемы переработки макулатуры гораздо ниже, чем в европейских странах. Дело в том, что в нашей стране обычные люди, никак не связанные с бумажной промышленностью, редко сдают макулатуру в соответствующие пункты. Простые подсчеты могут убедительно доказать материальную неэффективность сдачи макулатуры. Белая (офисная) бумага оценивается в среднем в 1,30 рублей за килограмм, а более низкосортная бумага (газеты, книги, журналы) – примерно в 1 рублей за килограмм. Учитывая, что мест приема макулатуры не так уж много, Вам скорее всего придется ехать куда то, а следовательно, тратить деньги на проезд. То есть, просто проехав на автобусе по Петербургу туда и обратно, вы затратите 28 рублей. Нетрудно подсчитать, сколько Вам нужно будет сдать бумаги только для того, чтобы покрыть транспортные расходы. В то же время малое количество подобных пунктов в черте города легко объяснимо. На основании законодательства такие пункты требуют предварительного согласования с государственными природоохранными органами, органами санитарно-эпидемиологического надзора и государственной пожарной службы и должны проходить обязательную государственную экологическую экспертизу. Они должны располагаться не менее чем в 20 м от жилых общественных зданий и не менее чем в 50 м от лечебно-профилактических детских учреждений и школ.
Макулатурная масса является сложной полидисперсной системой. Фракционный состав макулатурной массы: коротковолокнистая фракция – 19−28 %, длинноволокнистая – 65−70 %.
Коротковолокнистая фракция макулатурной массы (short fiber fraction – SF) состоит из коротких волокон, обрывков ороговевших волокон длиной менее 0,2 мм; характеризуется высокой степенью помола и низкими бумагообразующими свойствами.
Длинноволокнистая фракция макулатурной массы (long fiber fraction – LF) состоит из грубых длинных волокон; имеет низкую степень помола и потенциально высокие показатели механической прочности.
Фракционирование макулатурной массы – технологическая операция по разделению волокнистой суспензии на фракции, отличающиеся по средней длине волокна и содержанию примесей.
Цель фракционирования макулатурной массы – разделение волокнистой суспензии на фракции для селективной обработки или производства отдельных слоев многослойного картона.
Низкие показатели механической прочности макулатурной массы обусловлены наличием SF-фракции и обрывков волокон. Ороговение волокон при сушке бумаги и картона приводит к уменьшению их способности к образованию водородных связей, что является основной причиной ухудшения бумагообразующих свойств макулатурной массы. Разволокнение макулатуры и размол макулатурной массы сопровождаются разрушением структуры волокна, при этом вторичное волокно становится более измельченным и менее фибриллированным по сравнению с первичным, а полученная бумага – менее прочной, более рыхлой, мягкой, непрозрачной.
Одним из путей восстановления бумагообразующих свойств вторичного волокна является фракционирование макулатурной массы с последующим размолом LF-фракции и смешиванием её с SF-фракцией либо раздельным использованием фракций.
Фракционирование макулатурной массы позволяет снизить УРЭ на переработку макулатуры на 15−20 % по сравнению с традиционным способом, так как дополнительному размолу подвергается лишь LF-фракция. В то же время фракционирование макулатурной массы крайне редко применяется в технологических линиях переработки макулатуры. При дополнительном размоле LF-фракции макулатурной массы возможно улучшение качества волокнистого полуфабриката при возвращении этих волокон в основной поток. Данная обработка длинных волокон более целесообразна при использовании макулатуры, содержащей сульфатную целлюлозу.
В технологических линиях переработки макулатуры сочетание фракционирования и сортирования в отдельных аппаратах обеспечивает эффективное удаление примесей и разделение макулатурной массы на фракции, которые могут быть оптимально обработаны.
Фракционирование макулатурной массы, полученной из гофрокартона, обычно включают в технологическую схему для производства тест-лайнера, бумаги-основы для гофрирования и коробочного картона (рис. 1). Пос¬ле разволокнения макулатуры производится грубое сортирование макулатурной массы с использованием сита с круглыми отверстиями. Отходы грубого сортирования макулатурной массы направляются на сортировку конечной ступени, которая работает без давления и выполняет функцию аппарата для промывки отходов с целью предотвращения потери волокна.
После грубого сортирования макулатурной массы подвергается фракционированию в одну или две стадии в зависимости от требований к качеству конечной продукции. Фракционирование макулатурной массы осуществляется на сортировке с щелевыми отверстиями. Оптимальные результаты фракционирования макулатурной массы достигаются при обработке очищенной макулатуры с повышенным содержанием длинных волокон. Ширина щели сита фракционатора подбирается с учетом условий достижения высокой чистоты SF-фракции и достаточного отделения длинных волокон. Далее SF-фракция макулатурной массы сгущается и подается на хранение или используется для получения верхнего слоя картона.
применяемой для произ-водства тест-лайнера
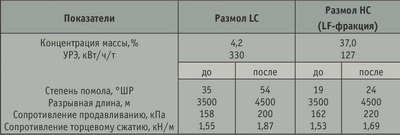
Дополнительное сортирование LF-фракции макулатурной массы производится в сортировке с дефлокулирующим эффектом, так как она содержит большое количество примесей, пучков волокон и, возможно, неразволокненных фрагментов макулатуры. Отходы тонкого сортирования LF-фракции макулатурной массы непрерывно удаляются из системы.
При наличии легких примесей применяется очистка LF-фракции макулатурной массы в реверсивных гидроциклонах. При недостаточном отделении легких примесей в гидроциклонах LF-фракция макулатурной массы после сгущения обрабатывается в диспергаторе, что способствует её гомогенизации. Кроме того, диспергирование LF-фракции макулатурной массы позволяет отделить от волокон частицы печатной краски и распределить на волокне остаточные частицы липких веществ. Таким образом, обработка LF-фракции макулатурной массы завершается размолом с целью повышения показателей механической прочности картона или диспергированием для гомогенизации суспензии. Полученная масса используется для производства нижнего слоя картона.
Использование барабанного гидроразбивателя позволяет значительно сократить количество технологических операций подготовки макулатурной массы. Технологическая схема переработки макулатуры типа FibreFlow представлена на рисунке 2.
Дальнейшим совершенствованием схемы подготовки макулатурной массы являются дополнительная ступень фракционирования LF-фракции и включение ступени промывки SF-фракции (рис. 3). Двойное фракционирование позволяет дополнительно сократить затраты на обработку макулатурной массы, так как диспергированию не подвергаются МF-фракция (средневолокнистая) и SF-фракция. Разделение фракций повышает гибкость технологии. Фракции можно смешивать в различных комбинациях в зависимости от требований к конечному продукту: обычно SF-фракция используется для производства верхнего слоя картона, МF-фракция – для среднего, LF-фракция – для нижнего.
Разволокненная суспензия подвергается грубой очистке и сортированию. Далее осуществляется фракционирование макулатурной массы в две ступени: на первой ступени отделяется SF-фракция, на второй – МF-фракция. SF- и МF-фракции направляются на промывку и сгущение.
Технологическая схема со ступенью промывки применяется в случае повышенной зольности макулатурного сырья (рис. 4). Промывка SF-фракции позволяет значительно снизить зольность макулатурной массы. Фильтрат от промывки SF-фракции подвергается очистке на установке микрофлотации с последующим повторным использованием в технологическом процессе, а в случае повышенных требований к степени очистки фильтрата может осуществляться микрофлотация с биологической очисткой, ультрафильтрацией или обратным осмосом.
Фракционирование макулатурной массы осуществляется в напорных сортировках, которые используются и для сортирования. При этом применяются сита с отверстиями меньшего диаметра или щелями меньшего размера с нулевым профильным углом. Обработка макулатурной массы при сортировании обеспечивает 5−25 % отходов, при фракционировании – 30−40% (LF-фракция).
В качестве фракционаторов используются сортировки с диаметром отверстий сита 1,4−1,8 мм, при этом отходы в виде LF-фракции должны составлять не менее 50−60 % от объема поступающей массы. При фракционировании макулатурной массы можно исключить диспергирование и/или размол SF-фракции.
Сортировки типа MоduScreen F фирмы Andritz применяются в системе FibreFlow для фракционирования макулатурной массы. Данная сортировка оборудована цилиндрическим ситом с размером щелей 0,15 мм. Длинноволокнистая фракция проходит тонкое сортирование последовательно в три ступени на сортировках с размером щелей 0,2 мм.
Сортировка типа OptiScreen FS фирмы Metso может быть использована для фракционирования макулатурной массы при концентрации 2 %, для сортирования длинноволокнистой фракции макулатурной массы.
Сортировка типа CELLECOSCREEN фирмы GL&V может применяться для фракционирования макулатурной массы. В сортировке могут быть использованы сита различного типа при регулировании зазора между ротором и ситом, а также скорости вращения ротора.
Фракционирование макулатурной массы можно осуществлять в гидроциклонах, при этом более длинные жесткие волокна с меньшей площадью поверхности сосредотачиваются в нисходящем потоке, а мелкие, хорошо размолотые волокна и примеси с большей площадью – в восходящем потоке.
Фракционирование в гидроциклонах имеет следующие недостатки по сравнению с напорными сортировками: низкая концентрация суспензии – 1,0−1,5 %; повышенный УРЭ – 10- 20 кВт/ч/т.
На фракционаторе, сконструированном на основе гидроциклона, – разработка ОАО «Караваево» и ОАО «Вторресурсы-Караваево» – фракционирование осуществляется в одну ступень: пропускная способность аппарата – 60 л/мин, производительность – 40 кг/ч. Подготовка макулатурной массы с использованием разделения на SF- и LF-фракции с последующим размолом LF-фракции от 24 до 32°ШР и смешиванием обеих фракций обес¬печивает повышение сопротивления продавливанию картона тест-лайнера на 14 % при снижении УРЭ.
Фирма GL&V рекомендует осуществлять фракционирование и промывку на барабанном сгустителе типа FDW после тонкой очистки в гидроциклонах, в том числе и реверсивных. При сгущении макулатурной массы до концентрации 6−7 % отделяется LF-фракция, которая направляется на термодиспергирование. Фильтрат и SF-фракция подаются на наклонные сита для улавливания волокна, фильтрат подвергается очистке на микрофлотационной установке DAF.
На некоторых технологических линиях переработки макулатуры применяется дополнительный размол макулатурной массы. Дополнительный размол, или «холодное» диспергирование, способствует восстановлению основных бумагообразующих свойств макулатурной массы, в первую очередь показателей механической прочности, приближая их к свойствам первичных волокнистых полуфабрикатов.
Цель размола заключается в подготовке поверхности волокон к образованию межволоконных связей за счет частичного разрушения наружных клеточных стенок, повышения гибкости и пластичности волокон при их набухании.
макулатурной массы обычно представляет собой смесь различных видов волокна: по происхождению – породе древесины; по методу получения – химическое, химико-механическое, механическое, беленое или небеленое; по использованию – изготовление различных видов бумаги и картона, последующая их обработка и переработка.
Состав макулатурной массы обусловливает значительные различия её способности к размолу. Данную проблему можно решить путем фракционирования макулатурной массы. Селективному размолу следует подвергать только грубодисперсную длинноволокнистую фракцию волокнистой суспензии (+14 меш.).
Размол макулатурной массы, как правило, осуществляется после грубой очистки и сортирования во избежание повреждения гарнитуры дисковых мельниц. Размол макулатурной массы до грубого сортирования приводит к уменьшению размеров частиц посторонних примесей, что затруднит их дальнейшее удаление.
Размол может значительно изменить свойства волокна: при увеличении степени помола макулатурной массы снижается пухлость и способность бумажного полотна к обезвоживанию. Отмечено отрицательное влияние размола на оптические свойства макулатурной массы, такие как белизну, непрозрачность и коэффициент светорассеяния.
При переработке макулатуры, не содержащей механической древесной массы, для использования при производстве писче-печатных видов бумаги или бумаги санитарно-бытового назначения дополнительный размол макулатурной массы обычно не производится.
При переработке макулатуры из небеленой сульфатной целлюлозы, применяемой для производства бумаги-основы для гофрирования и картона тест-лайнера, необходимо осуществлять дополнительный размол макулатурной массы.
При размоле волокна подвергаются укорочению, расщеплению, раздавливанию и набуханию, при этом развивается их внешняя и внутренняя фибрилляция.
Внешняя фибрилляция заключается в полном или частичном отделении от волокна клеточных оболочек и фиб¬рилл, что приводит к увеличению наружной поверхности волокон и росту числа свободных гидроксильных групп на его поверхности. Однако внешняя фибрилляция снижает прочность отдельных волокон.
Внутренняя фибрилляция изменяет структуру набухающей вторичной стенки волокна без влияния на прочность отдельных волокон, ослабляя связи между фибриллами, повышает гибкость и пластичность волокон в результате набухания гемицеллюлозной фракции и в целом повышает прочность бумаги.
Таким образом, размол макулатурной массы повышает способность волокон к образованию межволоконных связей при развитии внешней и внутренней фибрилляции волокон. Вместе с тем при размоле происходит определенное измельчение волокон макулатурной массы и увеличение содержания коротковолокнистой фракции, что снижает способность полуфабриката к обезвоживанию.
В современных технологических схемах переработки макулатуры дополнительному размолу подвергается только длинноволокнистая фракция макулатурной массы, что значительно снижает УРЭ и на 20 % повышает показатели механической прочности получаемой из нее бумаги. После размола отдельные фракции макулатурной массы могут быть вновь смешаны или распределены по слоям в многослойных видах конечной продукции.
Размол может производиться при низкой (LC) – до 5 % – и при высокой (HC) концентрации макулатурной массы – до 30 %.
Размол LC позволяет улучшить показатели механической прочности макулатурной массы: размол макулатурной массы при концентрации 3,2−3,5 % и УРЭ 70−100 кВт/ч/т повышает разрывную длину на 20 %, но оказывает незначительное влияние на её оптические свойства – коэффициент светорассеяния.
Размол HC осуществляется за счет трения волокон макулатурной массы друг о друга, что приводит к увеличению прочности во влажном состоянии бумаги, а также сопротивления раздиранию и излому. Однако размол HC требует повышенного УРЭ и при формовании бумажного полотна может происходить флокуляция волокон, что приводит к ухудшению печатных свойств, просвета и белизны бумаги. Размол НС целесообразно осуществлять при наличии в макулатурной массе целлюлозы из лиственных пород древесины, содержащей значительное количество волокон коротковолокнистой фракции.
На эффективность размола существенно влияет тип дисковой мельницы, рисунок применяемой гарнитуры и концентрация массы. Степень помола макулатурной массы при размоле зависит от качества и свойств макулатурного сырья и определяется видом конечной продукции.
При размоле основное механическое воздействие на волокна осуществляется передними кромками ножей гарнитуры. Ширина ножей гарнитуры не должна существенно превышать длину волокон – 3−4 мм. Определение интенсивности механического воздействия на волокна при размоле затруднено, так как при этом происходит локальное сгущение массы и давление ножей гарнитуры на слой волокна достигает нескольких мПа.
На эффективность размола влияют свойства макулатурной массы, удельное давление между ножами гарнитуры, УРЭ, концентрация, величина рН и температура, а также конструктивные особенности размалывающего оборудования: частота вращения ротора, ширина ножей гарнитуры статора и ротора, ширина и глубина канавок между ножами, величина зазора между ножами.
Для размола НС используют дисковые мельницы. УРЭ на размол макулатурной массы определяется величиной зазора между ножами гарнитуры. Увеличение степени помола макулатурной массы зависит от температуры размола, которая может составлять 40−90°С. При повышении температуры происходит небольшое увеличение степени помола макулатурной массы. По сравнению с размолом LC для осуществления размола НС необходимо производить сгущение волокнистой суспензии до концентрации 30% и более, что повышает УРЭ и затраты на приобретение дополнительного оборудования.
Сравнение результатов размола при низкой (LC) и высокой (НС) концентрации макулатурной массы для производства тест-лайнера представлено в таблице. Размол LC осуществляется в дисковых мельницах, установленных в три последовательных ступени, при SEL 1500 Вт/с/км. При этом показатели механической прочности макулатурной массы – разрывная длина, сопротивление продавливанию и торцевому сжатию – увеличиваются на 20−30 %.
LF-фракция подвергалась размолу НС в дисковом диспергаторе при температуре 40°С. При повышении степени помола LF-фракции макулатурной массы показатели разрывной длины, сопротивления продавливанию и торцевому сжатию увеличивались на 10−20 %.
Для дополнительного размола макулатурной массы используются дисковые и конические мельницы. Оборудование для размола макулатурной массы в зависимости от характера воздействия на волокна подразделяется на две группы: аппараты с механическим воздействием – ножевой размол – и гидродинамическим воздействием – безножевой размол.
В аппаратах с механическим воздействием размол осуществляется за счет контакта противолежащих жестких элементов гарнитуры на защемленный между ними деформируемый слой волокнистого материала.
Размол макулатурной массы в дисковых мельницах осуществляется при постоянном регулировании зазора. Недостатком дисковых мельниц является неравномерное качество массы и повышенный УРЭ в режиме эксплуатации мельницы в условиях отсутствия нагрузки.
Расход энергии на размол зависит от частоты вращения и диаметра размалывающих элементов мельницы. Производительность мельницы можно повысить за счет увеличения режущей поверхности и частоты вращения ротора. Общая размалывающая поверхность гарнитуры возрастает при увеличении длины и количества ножей гарнитуры. В конической мельнице величина размалывающей поверхности зависит от диаметра статора и ротора. Конструктивные особенности конической мельницы обеспечивают более длительное нахождение массы в зоне размола.
Широкий ассортимент гарнитуры размалывающих дисков позволяет регулировать условия размола, сокращая его продолжительность и обеспечивая фибриллирование волокон. В зависимости от типа используемой гарнитуры может производиться укорочение волокон либо фибриллирование при минимальном сокращении их длины.
Энергия размола передается волокнам в три фазы (рис. 5). В первой фазе подвижный нож ротора, пересекаясь с ножом статора, захватывает волокна: волокна, зажатые между кромками ножей, испытывают ударное воздействие.
Во второй фазе кромка ножа ротора прижимает волокна к плос кой-поверхности ножа статора. При этом, в зависимости от шероховатости поверхности и остроты кромки ножа, производится преимущественно внешняя или внутренняя фибрилляция волокон. В том случае, когда кромки ножей острые, а поверхность ножей шероховатая, происходит расслаивание и увеличение удельной внешней поверхности волокон, то есть внешняя фибрилляция. При сжатии волокон без рубки, резки и увеличения их внешней поверхности происходит внутренняя фибрилляция.
По окончании фазы «кромка – поверхность» сжатие волокон происходит между поверхностями ножей и продолжается фибрилляция волокон – третья фаза, которая заканчивается при расхождении кромок ножей ротора и статора.
Поскольку фазы размола противодействуют вращению ротора, УРЭ на размол складывается из энергии фазы пересечения кромок (кромка – кромка), энергии фазы пересечения кромки ножа ротора и поверхности ножа статора (кромка – поверхность) и энергии фазы фибрилляции (поверхность – поверхность). Распределение энергии между фазами в значительной степени зависит от соотношения ширины канавки и ширины ножа и определяет результат размола, то есть качество волокнистого полуфабриката.
При повышении расхода энергии в первой фазе волокна подвергаются режущему воздействию с уменьшением их длины, а во второй и третьей фазах волокна фибриллируются.
Характер обработки волокон при размоле макулатурной массы зависит от расстояния между статором и ротором аппарата. При вращении ротора в канавках статора и ротора образуются вихревые потоки, благодаря которым волокна непрерывно попадают в зазор между ножами. При увеличении скорости движения массы в радиальном направлении образование вихревых потоков усиливается.
Качество размолотой волокнистой суспензии определяется стабильностью зазора между элементами гарнитуры статора и ротора мельницы, величина которого при низкой концентрации массы составляет 0,1−0,2 мм.
Элементы гарнитуры конических и дисковых мельниц представлены на рисунке 6.
Дисковая мельница типа DD 4500 фирмы GL&V имеет прочную конструкцию, которая обеспечивает параллельность пластин гарнитуры и точное управление размером зазора между ними.
Коническая мельница типа TwinFlo E фирмы Voith со сдвоенной гарнитурой обеспечивает эффективный размол макулатурной массы благодаря высокой степени параллельности размалывающей гарнитуры. Преимущества аппарата: свободное перемещение ротора в осевом направлении, минимум движущихся деталей, оптимальное соотношение мощности при отсутствии нагрузки и в режиме эксплуатации, доступность и простота обслуживания.
Коническая мельница типа OptiFiner RF (Conflo) фирмы Metso Paper имеет ротор малой длины и средний угол конуса. Конструктивные особенности мельницы сочетают преимущества конических и дисковых мельниц: однородность массы, стабильный результат размола, точный контроль зазора между гарнитурой ротора и статора, легкость смены гарнитуры и высокую установочную мощность двигателя. Конический ротор обеспечивает более продолжительное нахождение волокнистого материала в зоне размола. В процессе размола волокна подвергаются интенсивной внутренней фибрилляции, в результате чего повышается сопротивление разрыву при растяжении и сопротивление раздиранию по сравнению с массой, размолотой в дисковой мельнице. Концентрация суспензии – 2− 6 %. Производительность аппарата составляет от 5 до 800 т/сутки, в зависимости от модели.
Преимущества мельницы типа OptiFiner по сравнению с дисковыми мельницами:
- наличие большей зоны размола и вследствие этого более продолжительное время нахождения в ней массы;
- точный контроль зазора между ротором и статором;
- высокие показатели механической прочности готовой продукции при более низкой степени помола с оптимальным сочетанием показателей жесткости, пористости, разрывной длины и сопротивления раздиранию;
- более продолжительный срок службы гарнитуры;
- низкий УРЭ за счет уменьшения нагрузки в режиме холостого хода.
При сравнении результатов размола в двухдисковой мельнице и в мельнице типа OptiFiner RF отмечаются увеличение сопротивления продавливанию на 5−10 % и снижение степени помола на 10−15 % при уменьшении УРЭ на 30−40 %. Размол в данной мельнице придает вторичным волокнам необходимые бумагообразующие свойства при сохранении длины волокна без снижения их прочности. Наилучшие результаты размола LC достигаются при УРЭ 30−60 кВт/ч/т.
В аппаратах гидродинамического действия размол осуществляется за счет силового воздействия на свободнодвижущиеся в жидкой среде волокна. К силовым воздействиям относятся: напряжение сдвига в градиентном потоке, кавитация, пульсации гидродинамического давления, трение между волокнами и турбулентные напряжения. Следует отметить, что названные виды гидродинамического воздействия присутствуют в той или иной степени и в аппаратах механического воздействия, работающих при концентрации массы до 3−6 %.
Принцип действия безножевых аппаратов основан на гидродинамическом воздействии на волокна. К ним относятся: роторно-пульсационные – энтштипер, пульсационные мельницы; акустические – гидродинамический генератор акустических колебаний (ГАК) – и кавитационные аппараты.
Энергоемкость гидродинамических аппаратов в 3−4 раза выше, чем ножевых, поскольку затраты энергии на создание сжимающего воздействия на волокна в 2−3 раза ниже, чем на создание сдвигового усилия при давлении ножей гарнитуры на слой волокна. Несомненным достоинством этих аппаратов являются мягкое воздействие на волокна без их укорочения и диспергирование пучков волокон на отдельные волокна. Поэтому гидродинамические аппараты применяются для дополнительного разволокнения макулатурной массы после гидроразбивателя с целью преодоления слабых межволоконных связей.
Для окончательного разволокнения и частичного размола макулатурной массы наибольшее распространение получили роторно-пульсационные аппараты, принцип действия которых основан на пульсации давления и высоком градиенте скорости потока волокнистой суспензии. К таким аппаратам относятся пульсационные мельницы отечественного производства. Достоинством пульсационных мельниц является жесткая и прочная конструкция рабочих поверхностей, устойчивых к износу при обработке макулатурной массы с содержанием твердых примесей. Использование различных химических реагентов при размоле макулатурной массы улучшает показатели качества бумаги и картона, вырабатываемых с её применением.
С. С. ПУЗЫРЁВ, профессор
Статьи из цикла «Ресурсосберегающая технология переработки макулатуры»:
Ресурсосберегающая технология переработки макулатуры. Часть 13
Ресурсосберегающая технология переработки макулатуры. Часть 12.2
Ресурсосберегающая технология переработки макулатуры. Часть 12.1
Ресурсосберегающая технология переработки макулатуры. Часть 11
Ресурсосберегающая технология переработки макулатуры. Часть 10
Ресурсосберегающая технология переработки макулатуры. Часть 9
Ресурсосберегающая технология переработки макулатуры. Часть 8
Ресурсосберегающая технология переработки макулатуры. Часть 6
Ресурсосберегающая технология переработки макулатуры. Часть 5
Ресурсосберегающая технология переработки макулатуры. Часть 4
Ресурсосберегающая технология переработки макулатуры. Часть 3
Ресурсосберегающая технология переработки макулатуры. Часть 2
Ресурсосберегающая технология переработки макулатуры. Часть 1