Дебаты о плитах продолжаются
Заметки с XII Международного симпозиума по древесным плитам - 2008 в Финляндии
В предыдущем номере журнала мы начали публиковать отчет о работе симпозиума, прошедшего в Диполи-центре 24–26 сентября 2008 года. Напомним, что работа симпозиума проходила по следующим секциям: общий обзор промышленности; формальдегидная сессия, фанерная сессия; прочность смол и контроль качества; технология производства смол; мониторинг и тестирование; сырье и новые продукты.
Особенности финской фанеры
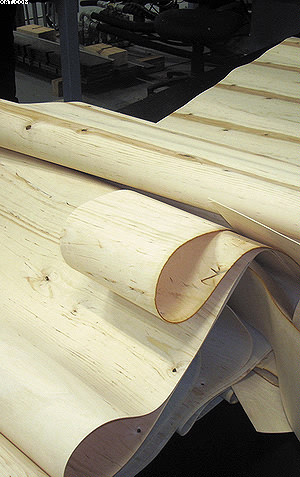
Лента шпона, полученного из чурака
В Европе с 2002 по 2006 год потребление фанеры выросло с 6 млн 876 тыс. до 7 млн 590 тыс. м3, объем потребления лиственной фанеры за тот же период - с 4 млн 186 тыс. до 4 млн 573 тыс. м3 В Финляндии также производят фанеру из древесины лиственных пород, при этом большая ее часть идет на экспорт (от 520 тыс. до 570 тыс. м3 ежегодно). Поэтому в 2006 году экономический эффект экспорта составил $482 млн 739 тыс. (по данным UNECE/FAO). В последнее время наблюдается резкое увеличение цен на фанерные бревна (например, в 2006 году оно составило 18%), а с учетом роста конкуренции древесного сырья в других секторах, например биоэнергетическом, вряд ли можно ожидать снижения цен. Поэтому необходимо использовать ресурсы рационально и производить продукцию с высокими физико‑механическими характеристиками. Этим вопросам был посвящен доклад Анти Рохумаа «Факторы, оказывающие влияние на древесину шпона» (Хельсинский технологический университет, Финляндия), прочитанный в рамках работы сессии «Фанера».
При изготовлении фанеры чураки, поступающие на разлущивание, предварительно проваривают до температуры 70°С. Целью работы сотрудников Хельсинского технологического университета было выяснить влияние температуры проваривания на цвет шпона, его смачивающую способность и прочность клеевого соединения, полученного в результате склеивания листов шпона фенолоформальдегидной смолой. Было обнаружено, что поверхность шпона, полученного при разлущивании чураков, проваренных при температуре 70°С, имеет светлые желто-красные тона. При обработке сырья при более низких температурах подобного эффекта не наблюдается. При таких условиях обработки чураков краевой угол смачивания меньше, что существенно уменьшает адгезионную способность. Таким образом, физико‑химические изменения поверхности древесины шпона напрямую зависят от температуры проваривания.
Генрик Хераайярви выступил с докладом «Качество российского и финского сырья в производстве фанеры». Целью его исследования было сравнить характеристики фанерных бревен, спиленных в восточном районе Финляндии и на северо-западе России, а также определить качество и предел прочности на разрыв полученной из этих бревен древесины шпона. Бревна были привезены в Финляндию и разлущены на заводе UPM в Йоенсу, после чего образцы шпона подверглись испытаниям на определение предела прочности на разрыв. Для исследований взяты две разновидности белой березы (Betula pubescens Ehrh и Betula Pendula Roth), средний возраст срубленных российских и финских деревьев составлял 78 и 36 лет соответственно. Средняя величина предела прочности на разрыв в направлении поперек волокон у образцов шпона, полученного из российской и финской древесины, составила 1,86 и 1,84 МПа соответственно.
Пределы прочности смол
На следующий день, 25 сентября, работу конференции продолжила сессия «Прочность смол и контроль их качества».
Милан Сернек (Люблянский университет, Словения) рассказал о зависимости температуры прессования на предел прочности при сдвиге для фенолоформальдегидной смолы. В процессе исследований изучалась ее адгезионная прочность во время отверждения. Для эксперимента был взят фенолоформальдегидный клей, применяемый в промышленности для производства фанеры, и березовый шпон (Fagus sylvatica L.) толщиной 1,1мм. Температура прессования была переменным фактором и задавалась в пределах от 140 до 200°С с интервалом в 20°С. Предел прочности при сдвиге определили как выходную величину эксперимента. С помощью диэлектрического анализа и системы ABES оценивались механические и физико‑химические показатели прочности клеевого соединения. Сами образцы фанеры склеивались в лабораторном гидравлическом горячем прессе. Было обнаружено, что высокая температура прессования способствует быстрому росту температуры в клеевом соединении и вызывает изменение в нем на химическом уровне, а прочность связи в клее зависит от степени его отверждения.
Следующий докладчик Йаоо Ферра (Порту, Португалия) говорил про оптимизацию синтеза карбамидоформальдегидных смол. До сих пор эта смола широко используется плитными предприятиями, в основном из-за высокой реакционной способности, низкой стоимости и прекрасной адгезии к древесине. Тем не менее влияние реакционной способности смолы на эксплуатационные качества производимых древесных плит до сих пор до конца не выяснено. В ближайшем будущем компании будут вынуждены выпускать смолы с уровнем свободного формальдегида не выше, чем у натуральной древесины. Йаоо Ферра были рассмотрены следующие факторы: число добавлений в процессе реакции карбамида в связующее, временной промежуток между каждой добавкой и уровень pH. Все это оказывает влияние на прочность когезионной связи и уменьшение эмиссии формальдегида из смолы. Образцы смолы были предоставлены компанией EuroResinans (Португалия).
Будущее за меламином?
Работа сессии «Технология смол» началась с доклада Дэвида М. Хармона. Он рассказал о преимуществах карбамидоформальдегидной смолы, модифицированной меламином. По новой технологии изготовления, которая запатентована в 25 июня 2008 года в США, было получено связующее, имеющее сверхнизкое содержание формальдегида и способное применяться в производстве плит MDF, ДСП и фанеры. Изначально меламин вводили в низкомолекулярные смолы для усиления поперечных связей. Однако стабильность при хранении и водостойкость этого связующего не соответствовала требованиям. К тому же скорость их отверждения была намного ниже стандартных смол.
Новый продукт - это эквивалент связующего, у которого в составе нет формальдегида и который может использоваться в производстве древесных плит без изменения последовательностей существующего технологического процесса. При разработке новой смолы было решено в первую очередь минимизировать суммарные издержки производства. Получаемая смола имеет хорошую стабильность при хранении, физико‑механические показатели, и внедрение нового материала на предприятии не уменьшит его производственных мощностей.
ДСП из кукурузы
В последний день Международного симпозиума по древесным плитам были заслушаны доклады на сессии «Сырье/новые изделия». Фраунгоферовский научно-исследовательский университет (Германия) занимается разработкой легких древесно-стружечных плит, получаемых из отходов сельского хозяйства. Целью исследования было получение плит плотностью 300-500 кг/м для мебельной промышленности. За основу были взяты два способа: использование сырья малой плотности и получение комбинированных материалов.
Для разработки первого метода был организован совместный Европейский проект под названием DIPP, в рамках которого легкие древесно-стружечные плиты изготавливали из однолетних и многолетних растений. Стебли подсолнечника (Helianthus annuus), топинамбура (Helianthus tuberosus) и кукурузы (Zea maize) насыщены легкими паренхимными клетками, они особенно подходят для изготовления легких древесно-стружечных плит. Целью эксперимента было сравнение свойств изготавливаемых плит со свойствами древесно-стружечных плит, получаемых из натуральной древесины.
Итак, для изготовления однослойных древесно-стружечных плит были взяты стебли подсолнечника, топинамбура и кукурузы. После измельчения стеблей получали древесные частицы для изготовления плит толщиной 16мм, плотностью 400 кг/м. В качестве связующего использовалась PMDI. Гидрофобные вещества в производстве плит не использовались. Для сравнения взяли древесно-стружечные плиты из древесины ели и тополя. Результаты механических и влажностных характеристик следующие:
- Плиты из стеблей подсолнечника и топинамбура имели такую же, как и плиты из древесины тополя, прочность клеевого соединения, что соответствует европейскому стандарту EN 312 для марки плит P2.
- Предел прочности при изгибе (2–6 Н/мм) у всех исследованных плит из сельскохозяйственных культур - низкий. У плит из кукурузы он самый высокий (6,2 Н/мм2), а у плит из топинамбура самый низкий (2,4 Н/мм. Поэтому требования, предъявляемые EN 312 для марки плит Р2, выполнены не были.
- У плит из топинамбура самая низкая величина разбухания по толщине (вымачивание в течение 24 часов) - 9,4%, у плит из древесины тополя - 6,6%, а у плит из ели - 7,1%. С другой стороны, водопоглощение у плит из сельскохозяйственных культур больше в 2-3 раза (58,7; 75,4; 95,7%), чем у древесных плит (31,4; 36,5%).
Следующим этапом исследований было получение плит из топинамбура плотностью примерно 650 и 440 кг/м с применением разных связующих. Результаты этого эксперимента таковы:
- У однослойных плит, склеенных на карбамидоформальдегидном связующем, с плотностью 658 кг/м высокие показатели по прочности клеевого соединения и пределу прочности при изгибе, чем у трехслойных плит плотностью 440 кг/м.
- Трехслойные плиты на карбамидо- и таниноформальдегидном связующем, полученные из древесины ели и тополя (наружные слои) и топинамбура (внутренний слой), имели практически одинаковые характеристики по пределу прочности при изгибе, модуль упругости и прочности клеевого соединения.
- Свойства трехслойных плит малой плотности (440 кг/м) с внутренним слоем из топинамбура не соответствовали стандарту EN 312 для марки плит Р2.
Реализацией второго метода (производство легких древесно-стружечных плит, в состав которых входят вспененные клеи и добавки) занималось Немецкое министерство по образованию и развитию науки (BMBF). В рамках этого проекта были поставлены следующие задачи: вспенивание карбамидоформальдегидного клея с помощью воздуха и поверхностно-активных соединений; смешивание добавок и полистирола в карбамидоформальдегидной смоле; применение пенообразующих полиуретановых клеев, в которых отсутствует формальдегид.
Новое оборудование – новые возможности
Роберт Лос (компания Maier, Германия) рассказал о многостороннем применении центробежных стружечных станков MRZ. Он заметил, что изначально станок марки MRZ широко применяялся (и применяется до сих пор) в производстве древесно-стружечных плит. Большим спросом он начал пользоваться с 1996 года. На сегодняшний день станок претерпел изменения (увеличено количество ножей от 48 до 60, скорости вращения ротора, скорости резания от 80 до 110 м/сек), что предопределило расширение области его применения в деревообрабатывающем секторе.
C новой конфигурацией и возросшими скоростями MRZ стало возможно уменьшить толщину древесных частиц до 0,6мм и увеличить производительность. Мелкая древесная стружка получается, как правило, в молотковых мельницах. Теперь же увеличение скорости станка MRZ HS позволяет получать древесные частицы толщиной 0,4–0,5мм. Поэтому технически измененный станок MRZ может найти применение в производстве древесных плит из остатков сельскохозяйственных культур (соломы, жмыха и конопли) и плит OSB. Одним из преимуществ станка является низкая энергоемкость и наличие клининговой системы.
В ходе конференции компания Limab AB (Швеция) ознакомила участников конференции с оборудованием для бесконтактного измерения толщины древесных плит, а компания Habasit представила новый способ бесподдонного прессования древесных плит с применением ленточных конвейеров.
Роджер Ровелл (заслуженный профессор в отставке Висконсинского университета, в настоящий момент - руководитель научно-исследовательского направления в области деревообработки компании Titan Wood Ltd) рассказал о производстве формоустойчивых и биостойких древесных композитов методом ацетилирования. Данная технология позволяет получить экологически чистые древесные материалы. Это был последний доклад конференции Международного симпозиума.
Как и полагается главному организатору, завершая работу конференции, коммерческий директор Центра Биокомпозитов Роб Элайас подвел итоги работы и торжественно объявил о закрытии симпозиума. Но само мероприятие на этом не завершилось: все желающие смогли ознакомиться с работой прекрасно оборудованных лабораторий Хельсинского технологического университета и оборудованием, на котором студенты проводят свои исследования - и делают свои открытия. По мнению организаторов, это стимулирует молодых ученых трудиться на благо науки.
Екатерина МАТЮШЕНКОВА