Ligna 2017. И целого мира мало!
Разговор о прошедшей в г. Ганновере (ФРГ) выставке Ligna 2017 мы начали в предыдущем номере журнала с личных и общих впечатлений о ней, а теперь пришло время уделить внимание самым интересным новинкам и наиболее значимым, на наш взгляд, экспозициям компаний-участниц.
Надпись new (в переводе «новинка, новый») попадалась в наполненных ревом машин и гулом людских голосов павильонах ганноверского выставочного центра на каждом шагу. Оно и понятно: все компании-участницы, от мала до велика, стараются на этом мероприятии «показать товар лицом» и хотят, чтобы это лицо вышло максимально привлекательным. Ну и, разумеется, приберегают для Ligna свои новые разработки, машины, станки, установки, инструмент, системы, линейки и т. п. - как кутюрье готовят свои коллекции к модному сезону.
Будущее - рядом. Руководитель Союза немецких машиностроителей VDMA Вольфганг Пешль отметил:
- Ключевым фактором роста отрасли сегодня является набирающая обороты во всех ее секторах дигитализация. Даже довольно небольшие и простые станки с помощью цифровых «облачных» технологий могут быть интегрированы в производственный поток, а оборудование индустриального уровня обладает возможностями самообучения и самооптимизации.
В самом деле, собственный вклад в Industry 4.0 - разработки в сферах компьютерной визуализации технологических процессов и автоматизации производства - постарался внести едва ли не каждый участник выставки в Ганновере. Поэтому волей-неволей мы будем не раз обращаться к этим темам, о какой бы части экспозиции ни шла речь - посвященной технологиям лесозаготовки и лесопиления, производству древесных плит или получению энергии из отходов деревообработки...
Сотрудники журнала «ЛесПромИнформ», квадратно-гнездовым способом осваивая экспозиции павильонов, постарались собрать информацию обо всем наиболее значимом, новом, революционном (в конце концов, Ligna задает индустриальную моду в ЛПК как минимум на два года), и эту информацию предлагаем вниманию наших читателей. Поехали!
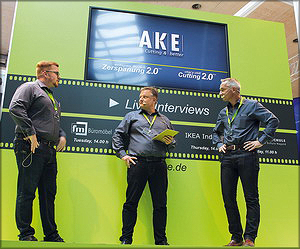
Наш постоянный автор, заместитель генерального директора ООО «АКЕ Рус» Владимир Падерин поделился информацией о том, что входило в экспозицию известного производителя режущего инструмента AKE Knebel GmbH & Co. KG (Балинген, Германия) на Ligna 2017:
- Как и двумя годами ранее, продукция АКЕ была представлена на двух стендах в разных павильонах, что отражало работу компании в двух направлениях: инструмент для лесопильных предприятий и для деревообрабатывающих и мебельных производств. Были продемонстрированы образцы лесопильных пил новой конструкции для ФПЛ и ФБЛ, делительные сверхтонкие пилы для станков второго ряда, дистанционные кольца новой конструкции для оборудования ведущих лесопильных европейских брендов. На стенде, посвященном деревообработке и мебельному производству, были представлены новые образцы алмазных пил и фрез (DP) в развитие темы Cutting 2.0. серии SuperSilent (SS) для форматнообрезных станков средней и тяжелой серии, новых насадных алмазных фрез для разного оборудования серии Harmony, а также концевых алмазных одно-, двух- и трехзубовых фрез новой конструкции. Особенности этих продуктов - в их конструкции, позволяющей достичь оптимального вывода стружки из зоны резания, новых материалах корпуса и режущих элементов.
В ответ на просьбу высказать мнение о новинках других компаний, которые вызвали у него наибольший профессиональный интерес, г-н Падерин порадовал объективностью: «Очень интересные разработки были показаны на стенде фирмы STARK - новые по конструкции и креплению сменные ножи для фрез на сращивание, по сравнению с ножами предыдущего поколения. У них более высокая стойкость; кроме того, для их установки в корпус фрезы требуется меньше времени, а еще коллеги показали и комплекты фрезерного инструмента новой конструкции для производства окон и дверей».
Возвращаясь к новинкам компании АКЕ, необходимо упомянуть пильное полотно для торцовочных пил из линейки продуктов AKE Cutting 2.0, впервые представленное в Ганновере. В числе его особенностей - увеличение ресурса инструмента на 70% по сравнению с предыдущей моделью, снижение общих затрат на 35%, универсальность эксплуатации и бесшумная работа, отличное качество. Внимание деревообработчиков также привлекли фрезы 2.0 DP Harmony в модификациях Z1, Z2, Z3 (они характеризуются длительным сроком службы, обработкой кромок заготовок без сколов, возможностью обработки самых капризных материалов), модифицированные дисковые пилы SuperSilent (по заявлению производителя, их отличают высокое качество реза наряду с беспрецедентной экономичностью, снижение шума на 75% в сравнении с традиционными дисковыми пилами, универсальность - они подходят для обработки как массива древесины вдоль и поперек волокон, так и плитных материалов: ДСП, MDF и OSB, в том числе облицованных с двух сторон).
На стенде компании Altendorf GmbH & Co. KG (Минден, Германия) состоялась мировая премьера «цифрового пильного гида» - Altendorf Magis, который представляет собой компьютерный навигатор. Magis помогает оператору выполнять рабочие процессы при распиловке. Интеллектуальное программное обеспечение помогает даже не самому опытному оператору, по заранее подготовленной карте раскроя, пошагово выполнять последовательность технологических операций. Следуя подсказкам интуитивно понятного интерфейса, человек выполняет процесс пиления материала, экономя материал и рабочее время. Вводные данные для Magis поступают из программы оптимизации. Также предусмотрена возможность установки принтера для печати этикетки с информацией для дальнейшей обработки.
- Система Altendorf Magis - первая цифровая система управления для операторов станков с подвижным столом, - поясняет управляющий директор компании Altendorf Йорг Ф. Майер. - Она указывает оператору верную последовательность резания, обеспечивая оптимизацию обработки панели. Система существенно упрощает работу оператора, помогает повысить безопасность на рабочем месте и сократить время, необходимое для выполнения задания, предустановленного на ПК станка.
По информации специалистов компании Altendorf, на стенде представлены несколько передовых решений, которые позволяют оптимизировать рабочий процесс и расширить возможности форматных станков.
Новый подрезной агрегат с парковкой может перемещаться из рабочей зоны под рабочий стол - на место парковки и находиться в режиме ожидания, что позволяет применять пильные диски диаметром до 550 мм.
Впервые в конструкцию форматного станка включен рабочий стол с воздушной подушкой для уменьшения трения и исключения царапин при обработке тяжелых материалов или материалов с легко повреждаемой поверхностью. Воздушная подушка в значительной степени уменьшает сопротивление трения между материалом и столом станка, что не только облегчает процесс обработки тяжелых заготовок, но и значительно снижает риск возникновения царапин на заготовке.
Эргономика рабочего места оператора индивидуальна. Теперь при заказе форматного станка клиент может выбрать станину из трех вариантов - высотой 85, 88 и 91 см - с учетом потребностей своего производства.
Менеджер проектов компании Amandus Kahl GmbH & Co. KG (Германия) Владимир Выборов поделился информацией о самом интересном на стенде производителя оборудования для гранулирования и утилизации отходов:
- На выставке Ligna мы показывали новый пресс с максимальной производительностью до 8 т/ч. Сейчас эта модель тестируется на предприятии крупнейшего производителя пеллет в США.
Кроме того, на нашем стенде были представлены и другие новые разработки: система смены гидравлической головки пресса (теперь пользователям будет удобнее ее обслуживать и демонтировать при необходимости); съемная матрица - сейчас мы тестируем ее возможности при гранулировании бытового мусора, а в дальнейшем проверим и при обработке древесных отходов. Особенность этой матрицы в том, что в отличие от прежних литых матриц у нее можно заменять только среднюю часть, а кольца остаются. Изменения конструкции наших прессов обеспечивают их более удобное обслуживание, чем обслуживание прессов с кольцевой матрицей - проще выполнять замену запасных частей: матриц, роликов, гидравлических головок.
Рынок растет, растут и объемы производства и потребления пеллет, для нас это очень позитивная тенденция, год складывается очень хорошо для компании. Сейчас реализуем большой проект в Архангельской области, выступаем как генеральный поставщик; у оборудования Amandus Kahl, которое будет там установлено, высокая производительность - 22,5 т/ч пеллет. Довольно серьезные контракты заключены с предприятиями из Башкирии и Коми - мощность оборудования, которое будет поставлено этим компаниям, - 2,5 и 5 т/ч соответственно. Есть и другие перспективные наработки в России.
На стенде шведской компании AriVislanda наибольший интерес посетителей вызвал станок последнего поколения QSS P-700, предназначенный для профилирования и отделения боковых досок. Благодаря высокому проценту выхода (за счет использования технологии наклонного пиления боковых досок) производственная линия оборудования QSS P-700 может стать эффективным решением для линий с оптимизацией и профилированием боковых досок. Станок легко вписывается в цепочку при модернизации оборудования на большинстве лесопильных предприятий и может быть использован в разных конфигурациях с дополнительными опциями.
Коммерческий директор компании Artiglio S.R.L. (Италия) Фабио Пассарди рассказал о том, что этот производитель высококачественного лесопильного оборудования представил на стенде уникальную автоматическую линию для распила бревен диаметром от 150 до 1500 мм и длиной до 16 м. Основа линии - высокопроизводительный вертикальный ленточнопильный станок с наклоном рамы 18° для двухстороннего пиления. Он разработан для раскроя древесины любой породы (и отлично подходит для распиловки древесины ценных пород, когда нежелательно допускать растрескивание досок). Станок снабжен запатентованной гидравлической кареткой, состоящей из четырех автономных модулей, при пилении бревен небольшой длины задействуется лишь необходимое число модулей, остальные не участвуют в процессе, что позволяет обеспечивать существенную экономию энергии. Линия, возможности которой обеспечивают пиление бревен разного диаметра в широком диапазоне при гарантированном высоком качестве продукции и 70% объемного выхода, вызвала огромный интерес у посетителей. Отличные характеристики лесопильной линии и ее умеренная цена обеспечили большое число запросов на это оборудование от клиентов со всего мира.
А выставочный образец уже приобретен постоянным заказчиком компании из Германии (у него это уже третья по счету линия Artiglio).
Инновационная система Inert Coat испанской компании Barberan, которая успешно реализована в установках High Gloss HotCoating, предназначена для повышения качества глянцевых поверхностей. Система Inert Coat позволяет осуществлять высокоэффективный процесс отделки готовых панелей с нанесением слоя УФ-лака и прозрачной пленки. Слой разглаживается и высыхает почти мгновенно, образуя красивую блестящую поверхность, так называемый суперглянец, который очень ценится мебельщиками. Разработка HotCoating приобретает все больше поклонников среди производителей предметов интерьера благодаря получению высокого качества поверхностей и экономичности довольно простого их производства, а также многообразию финишных отделок и декоров, завидным эксплуатационным свойствам.
Среди нововведений, которые Barberan представил в системах «высокого глянца», на самом видном месте оказалась новая Compact Line HG - машина для нанесения прозрачных высокоглянцевых пленок на поверхности (например, ламинированные и т. п.) с помощью дополнительного разглаживания слоя клея до каширования и каландрирования. В результате конечный продукт приобретает не только весьма привлекательный внешний вид, но и большую стойкость к истиранию и царапинам.
В ознаменование 10-летия презентации на Ligna первого в ассортименте компании однопроходного цифрового принтера Barberan продемонстрировала полную линейку печатных устройств для отделки древесины с шириной печати 1260 мм и десятью печатными группами. Большой интерес посетителей вызвала и линия Jetmaster, популярность которой подчеркивает тот факт, что более 30 подобных машин уже продано по всему миру.
Одна из недавних разработок испанской компании - новый кашировально-окутывающий станок Speed Press, разработанный по заказу шведского мебельного концерна IKEA. Barberan в апреле осуществил поставку этой машины для технологического центра в г. Эльмхульт (Швеция), в дальнейшем подобные прессы будут устанавливаться и на других площадках IKEA по всему миру.
Экспозиция компании Biesse (Италия) на стенде площадью 5 тыс. м2 продемонстрировала высокотехнологичные продукты и решения, позволяющие повысить эффективность и качество услуг. Think Forward - под этим девизом компания продолжает развивать технологии и предлагать интегрированные решения, которые являются комплексными, но простыми в использовании, что позволяет производить больше, лучше и с меньшими затратами.
«Заглядывать в завтра - это прекрасный способ понять, как действовать сегодня», - этими словами директор по маркетингу и связям с общественностью группы Biesse Рафаэль Прати открыл пресс-тур по выставочной площадке компании.
«На выставке в Ганновере мы показали прежде всего свои последние разработки в рамках концепции Industry 4.0, - подчеркнул директор по продажам подразделения деревообработки и развития сети филиалов компании Biesse Федерико Брокколи. - Все оборудование интегрировано и связано между собой, что повышает общую производительность и эффективность "цифрового" производства. Мы называем такие решения IoB - Internet of Biesse».
«В экспозиции более 40 моделей машин для всех категорий производителей - от небольших ремесленных мастерских и предприятий, которые производят единичные изделия по индивидуальным заказам, до крупных компаний с крупносерийным производством, - добавил директор по сервису и инновациям Стефано Калестани. - Благодаря готовым решениям Biesse 4.0 любое из предприятий может превратиться в самую настоящую "умную фабрику"».
Многофункциональный обрабатывающий центр WinLine 16 - одна из недавних разработок Biesse в области производства окон и дверей - предназначен для ремесленников и небольших компаний, стремящихся увеличить выпуск продукции, а также для средних и крупных компаний, у которых возникает необходимость в изготовлении малых партий изделий и изделий нестандартных размеров. На станке можно производить как стандартные рамы, так и детали специальной формы, включая арочные, с максимальным уровнем автоматизации и при минимальном участии оператора. Двойной электрошпиндель позволяет выполнять все операции без простоев оборудования. WinLine 16 отличается чрезвычайной точностью и простотой использования - работа на нем не требует особых навыков, а возможности станка обеспечивают высокую эффективность. Нужно просто загрузить в машину заготовки, следуя указаниям, содержащимся в программном обеспечении, и после обработки выгрузить готовую деталь. При загрузке стандартной палеты заготовок машина за 50-60 мин. автономной работы производит до 280 деталей. Для установки WinLine 16 не требуется большой площади - центр занимает всего 45 м2.
На стенде Biesse Group были также представлены два инновационных обрабатывающих центра серии Uniteam, предназначенные для механической обработки деталей из массива древесины и многослойных конструкций. Uniteam CK специально разработан для изготовления сложных архитектурных элементов, применяемых в деревянном домостроении, на нем можно обрабатывать балки с поперечным сечением до 1000x300 мм и длиной до 14 м. Uniteam E MIX - обрабатывающий центр для раскроя панелей X-Lam толщиной до 300 мм.
Скажем пару слов о двух новых центрах раскроя плит. Дебютировавший в Ганновере Selco WN 2 - бюджетный вариант станка начального уровня для использования на малых и средних производствах. Он представляет интерес для предпринимателей, делающих первые инвестиции в оборудование, которое позволит повысить качество продукции при переходе от ручных станков к полноценному автоматизированному производству. Простая в управлении и надежная машина Selco WN2 оснащена запатентованной системой Quick change для смены пил без использования дополнительных инструментов. Selco WNA 6 - серьезное промышленное оборудование, секционная система с двумя полностью независимыми линиями резки и автоматической загрузкой, подходящая для нужд автоматизированных мебельных производств.
Обновления коснулись популярной линейки станков Rover. В экспозиции можно было впервые ознакомиться с моделью Rover M5 для габаритных заготовок (высота - до 535 мм) с возможностью трехмерной обработки предметов сложных форм с высокой детализацией. У Rover M5 отличные рабочие характеристики, при этом он весьма компактен: рабочая зона - 3200x1600x535 мм, а все оборудование занимает в цехе всего 18 м2.
Обрабатывающий центр Rover K FT для нестинга обращает на себя внимание эргономичностью и возможностью доступа с четырех сторон. Его можно настроить так, чтобы рабочий процесс протекал либо слева направо, либо справа налево. Rover K FT - первое из новых решений Biesse для быстрой plug&play установки, он разрабатывался как машина с минимальными габаритами, характеристики которой позволяют обеспечить максимальную производительность.
В модельном ряду Rover произошли и другие обновления. Стоит отметить устройства bPad и bTouch. Первое из них представляет собой новую беспроводную панель управления для всех основных операций при подготовке рабочей зоны и оснастки инструментальных магазинов станков. bTouch - новый сенсорный монитор с диагональю 21,5'', который поможет оператору осуществлять взаимодействие со станком без использования клавиатуры и компьютерной мыши.
Инновации в области автоматизации - основной профиль деятельности подразделения BiesseSystems, предлагающего комплексные решения для оснащения «умных производств», полностью интегрированные системы при идеальном взаимодействии станков и программного обеспечения. Вот пример: обрабатывающий центр Rover B Edge в связке с 4-осевым манипулятором Synchro, который подает заготовки из стопки, позиционирует их на рабочем столе станка, а потом забирает и складирует по завершении всех необходимых операций. Рабочий цикл выполняется в автоматическом режиме без присутствия оператора до завершения обработки всей партии. Другая пара - пильный центр Selco WN 6 с компактным и эргономичным автоматическим загрузочным устройством X-Feeder, которое адаптируется к разным форматам панелей благодаря автоматическому позиционированию присосок. Загрузчик может поднимать панели длиной до 4400 мм. В экспозиционной части BiesseSystems также демонстрировался сортировочный Robot Sorter - исключительно функциональное решение для единичных изделий, при том что машина может располагать панели в правильной последовательности в зависимости от заданного процесса.
Большой интерес посетителей вызвали представленная на стенде компании новая платформа Machines Knowledge Center (разработана в сотрудничестве с альянсом Accenture - Microsoft) с большим числом сервисов и функций, которые позволяют резко повысить эффективность станков, а также автоматизированный склад WinStore (предлагается в трех вариантах - 3D K1, 3D K2 и 3D K3) в линии для массового производства единичных изделий и новая версия программного обеспечения bSuite.
Также посетители стенда могли ознакомиться с новой службой технической поддержки Biesse и лабораторией bLab, возможности которой позволяют протестировать самые передовые версии программного обеспечения, используемого в ЧПУ станков и линий концерна, предназначенных для производства новой продукции.
На Ligna 2017 компания Biesse поставила рекорд: ее стенд посетили 4500 человек, приехавших на ганноверскую выставку с разных континентов (которым помогали освоиться в «мире Biesse» три сотни специалистов!), было сделано заказов на 45 млн евро, из которых 35% пришлись на линии типа «4.0». Инвестиции Biesse в исследования и разработки составляют в среднем 14 млн евро в год, компания владеет 200 зарегистрированными патентами. В сеть компании входят 9 заводов и 37 филиалов, на нее работают 300 дилеров и представителей, доля экспорта составляет 90%.
Компания Bürkle GmbH из г. Фройденштадта (Германия) предложила вниманию гостей выставки новое оборудование для финишной обработки поверхностей с нанесением лакокрасочных покрытий. Новинка создана на модульной платформе, а для повышения качества распыления разработана технология увлажнения воздуха. Кроме того, оптимизировано управление воздушной струей, подключение ультрафиолетовых секций, полностью автоматизированы операции загрузки и выгрузки. Система проста в управлении и эргономична, на выставке была представлена в работе - причем покрытия наносились как на древесно-стружечные плиты, так и на изделия из пластмасс и металла.
Более 60 лет шведская компания C. Gunnarssons Verkstads AB (CGV) является поставщиком оборудования для сортировки пиломатериалов не только в страны Европейского союза, но и за его пределы: в Россию, Австралию, Новую Зеландию. На своем стенде компания представила инновационные системы для сортировки досок, эффективные в работе и легкие в обслуживании. Разработки компании нацелены на повышение полезного выхода продукции и увеличение прибыли как крупных лесопильных предприятий, так и предприятий невысокой мощности. Высокоэффективная работа подающих транспортеров обеспечивает отличное взаимодействие всех агрегатов и узлов линии, включая систему подачи, накопительные транспортеры и устройство поштучной подачи пиломатериалов. Благодаря отличным техническим характеристикам всех компонентов сортировочных линий оборудование позволяет с высокой точностью торцевать доски на любую длину на скорости более 200 досок в минуту, что обеспечивает повышение сортности пиломатериалов. Новая конструкция подвижных позиционирующих упоров перед триммером позволяет с высокой точностью осуществлять раскрой досок на нужные размеры даже при очень высокой скорости подачи. Длина подвижных упоров равна длине хода поршня, соответствующего расстоянию между двумя лезвиями пил, что позволяет осуществлять распил доски в любом ее месте.
На выставке свои новые технологические решения продемонстрировала известная машиностроительная компания Casadei-Busellato (Италия). В числе новинок - обрабатывающий центр с ЧПУ для производства панелей и окон Jet Master 35 с системой позиционирования опоры панели; новый кромкооблицовочный станок с управляемой осью Flexa 47XE, оснащенный системой клеенанесения горячим воздухом Air Jet Package; новый узел скругления углов A2 Super для кромочников Flexa 207 Super и Flexa 307; обрабатывающий центр с ЧПУ Jet Optima S 20, используемый для изготовления окон.
Следует упомянуть также инновационные бесщеточные двигатели на всех моделях форматно-раскроечных центров AXO и ряд опционально устанавливаемых устройств для линейки форматников Xenia.
Итальянская группа компаний Cefla Finishing сделала фокус на способах создания 3D-эффектов и цифровой печати на поверхностях. «Мы печатаем на всем. В высоком разрешении» - на без малого 1,5 тыс. м2 выставочной площадки доказательств этому тезису нашлось немало. В числе инноваций - J-Print 3D, система для создания 3D-эффектов, синхронизированная с устройством цифровой печати. Решения, предлагаемые Cefla, позволяют наносить высококачественные изображения на разные виды древесных материалов, пластик, керамику, фиброцемент, картон, ткани, стекло.
Вклад компании Cefla в мировой тренд Industry 4.0 вылился в концепцию «умной фабрики», в рамках которой были представлены: симулятор сCloner - инструмент моделирования производственных процессов для выбора оптимальных параметров и предотвращения возможных проблем; сTracker - инструмент для отслеживания, анализа и оценки в реальном времени процессов производства с целью повышения производительности; cLink - средство интеграции полученных данных и их передачи в систему управления (PLC, Programmable Logic Control).
Эти решения нашли применение как в упомянутых печатных устройствах, так и в обновленной линейке вертикальных сушилок Omnidry, в которых внедрена новая запатентованная технология полностью автоматического регулирования объема загрузки в зависимости от размера заготовок и логистических требований и без остановки процесса сушки. Благодаря революционной функции Flexpo и автоматическому изменению высоты лотка в Omnidry можно с большой эффективностью обрабатывать плоские и изогнутые панели разной толщины.
Покрасочная установка iGiotto X2, работающая под управлением программного обеспечения iGotto App, была впервые показана в Италии на Xylexpo и удостоилась там награды за инновации: два 6-осевых антропоморфных робота с гибкими «руками»-манипуляторами осуществляют покраску деталей сложных конфигураций в безостановочном режиме как синхронно, так и асинхронно: например, пока одна рука красит пласти изделий, вторая красит кромки. Установка разработана таким образом, чтобы роботы могли обрабатывать в том числе и детали большого размера (например, дверные и оконные рамы). Система обеспечивает максимальную гибкость и оптимальный контроль расхода лакокрасочных материалов благодаря автоматической оптимизации траекторий движения и распыления. Диагностика оборудования выполняется дистанционно. Автоматическая очистка распылительного пистолета позволяет сократить частоту планового техобслуживания.
Вакуумная установка Smartedge для нанесения покрытий и обработки кромок плоских и фигурных деталей получила обновление в виде запатентованной головки Whiz Head. Щеточный станок для очистки панелей перед нанесением ЛКМ Smartclean дебютировал в новой версии 4.0. Кроме того, итальянцами в Ганновере были впервые показаны несколько небольших, но важных новых приспособлений - в частности, взаимодействующая с роботом iGiotto система визуального распознавания cVision, а также iLoad - не требующая участия оператора автоматическая система загрузки и выгрузки деталей с подвесного конвейера без остановки линии.
Коммерческий директор группы Cefla Finishing Роберто Болоньини обратил оособое внимание наших корреспондентов на разработку подразделения Duespohl - уже успевшего завоевать популярность станка Robowrap. На этом оборудовании окутывание профиля можно выполнять со значительно меньшими затратами времени по сравнению с традиционными системами. Причем на станке можно обрабатывать профили множества типов. Сканирующему лазеру требуется всего несколько секунд для считывания геометрии детали и расположения инструмента в магазинах, после чего система независимо настраивает «руки» робота на необходимый профиль обработки. Время переналадки сведено к минимуму - смена профиля может быть выполнена всего за пару минут.
Датская компания C.F. Nielsen и ее российский представитель - ООО «Вуд-Энджин» представили ряд запатентованных новинок. Особый интерес посетителей вызвали:
- гидравлический брикетный пресс BPH Quattro в компактном исполнении (пресс, буферный бункер, дозирующая система и панель управления). У пресса прочная конструкция и панель управления с PLC и с дистанционным управлением. Он оснащен главным двигателем мощностью 45 кВт, его производительность - 400-600 кг/ч. Пресс может производить брикеты из комбинированных материалов; прямоугольные брикеты размером 150х60 мм весьма удобны для хранения и использования;
- экструзионный шнековый брикетный пресс BPE Shimada с главным двигателем мощностью 45 кВт, поставляется также в виде компактного блока с прессом, буферным бункером, дозирующей системой, панелью управления и пилой. Панель управления с PLC с дистанционным доступом, может поставляться с панелью управления на основе реле. Производимые брикеты размером 55x55 мм или 65x65 мм с квадратным или восьмиугольным сечением используют для отопления в каминах и дровяных печах. Благодаря большой плотности эти брикеты могут быть карбонизированы (цена на подобные брикеты довольно высока, однако по таким характеристикам, как продолжительность горения, дымообразование, срок и удобство хранения они намного превосходят обычные брикеты). Новое технологическое решение от компании C.F. Nielsen по производству карбонизированных брикетов (в комплект установки входят сушильная камера, пресс и оборудование для карбонизации украинской фирмы Green Power) еще проходит стадию тестирования, однако у компании уже сформирован перспективный портфель от европейских и даже латиноамериканских клиентов - всего более 20. Первые покупатели смогут опробовать технологию карбонизации брикетов на своих предприятиях в октябре текущего года.
Датский производитель продолжает разработку новых моделей оборудования и технологий для разных областей. В их числе, например, SBP-9 Star Press («Звездообразный пресс») - крупнейший в мире брикетный пресс производительностью до 5000 кг/ч, работа которого основана на поворотном принципе движения. Он разработан для производства малогабаритных брикетов размером 40х60 мм.
Итальянская компания CMC Texpan выставлялась на Ligna в рамках внушительной экспозиции Siempelkamp - и не затерялась на этих просторах, а очень достойно выступила в партнерстве с гигантом индустрии: смеситель клея, продемонстрированный компанией совместно с новым агрегатом Siempelkamp для дозирования связующего (который сейчас проходит стадию тестирования), вызвал большой интерес у специалистов.
Подобно многим другим экспонентам, компания CMC Texpan вышла на выставку с собственным уникальным девизом - «Консолидация и инновации», который и нашел свое отражение в представленной новинке - внедрять смелые разработки проще совместными усилиями. Инновации не являются самоцелью, а должны осуществляться целенаправленно, путем совершенствования тех решений, которые в наибольшей степени отвечают требованиям к качеству и надежности продукции. После их успешной интеграции и эксплуатации как в новых, так и в действующих установках EcoResinator Plus и EcoFormer SL представленные CMC Texpan новые решения в области осмоления и формования стружечного ковра получают все больше положительных отзывов.
Кроме того, тенденция устойчивого развития и рационального использования ресурсов, набирающая все большую силу в последние годы, нашла отражение в широком спектре технологических решений по утилизации древесных отходов, в которых учтены все требования по безопасности и защите производств от риска пожаров и взрывов.
Свои новинки в области многоходовых погрузчиков для длинномерных грузов представил постоянный участник выставки - Combilift. Среди них - электрический боковой погрузчик Combilift C8000ESL, один из самых грузоподъемных на рынке: погрузчик обеспечивает максимальную производительность и скорость обработки длинномерных грузов весом до 8 тонн, значительно экономя расходы на топливо и снижая эксплуатационные затраты.
Не осталась без внимания многочисленных гостей и система перевозки трейлеров на базе популярной модели C2500CB, которая способна перемещать груз весом до 2,5 тонн и длиной до 14 метров с возможностью подъема на высоту до 1400 мм.
Comec Group (Италия) подошла к началу 2017 года с оборотом более 11 млн евро, что на 10% больше по сравнению с предыдущим годом; еще 10% роста руководство компании ожидает в нынешнем году. Завершился амбициозный проект по расширению производственной площадки компании, а кроме того, проведена корпоративная реорганизация, в результате которой достигнута консолидация в рамках Comec Group компании Camam и подразделения CNC Wood and Technology. По словам Лючио Бергамаско, основателя Comec Group, компании Comec и Camam объединили сети продаж, но при этом сохранили производственную программу каждой, сделав акцент на особенностях ассортимента и избежав дублирования продуктов. На Ligna 2017 посетители впервые могли увидеть компании под единым «флагом» и на едином стенде.
Основное внимание посетителей пришлось на долю линии для производства дверных и оконных элементов, отличающуюся большой гибкостью и высокой степенью автоматизации, что позволяет выпускать изделия быстро и отличного качества.
На стенде были показаны два обрабатывающих центра семейства Frontal: Frontal WD, представляющий новое поколение систем для механического соединения, чрезвычайно востребованных в производстве мебели, и Frontal CN для изготовления фронтальных элементов мебельных ящиков; а также две машины серии MD: MD Jamb 11X для производства дверных косяков и MD Top XL - обрабатывающий центр для изготовления элементов кроватей, детской и садовой мебели. Многошпиндельный сверлильный станок Fmov CA был представлен как отличное решение для сверления отверстий в элементах мебели для установки фурнитуры. Классические станки и агрегаты, которыми известен бренд Camam, Fis 4C 3U, Tac Cn, Lec 200, Lol 75, SI/F/4C также получили свое место в экспозиции.
- В последние годы мы сосредоточились на реализации идеи комплексных технологических решений, - говорит Лючио Бергамаско, - максимально эффективных и быстрых производственных линий на базе наших станков с целью изготовления продукции самого высокого качества. Во многом именно поэтому мы решили объединить компетенции наших компаний, что позволяет создавать полные производственные цепочки из взаимодействующих машин для получения наилучших результатов клиентом.
Известная машиностроительная компания Dieffenbacher из германского Эппингена представила полностью измененную по сравнению с предыдущими выставками концепцию экспозиции. В связи с изменением общей структуры выставки стенд предприятия «переехал» в павильон № 26, и у специалистов компании появилась возможность сделать открытый стенд, что позволило оптимально распределить общее пространство на зоны для деловых переговоров, демонстрации новинок и свободного общения. Судя по отзывам посетителей, эта затея в полной мере удалась.
Под лозунгом «Следующий уровень эффективности производства», отражающим стремление фирмы предлагать клиентам наиболее эффективные системные решения на рынке, Dieffenbacher продемонстрировала свои новые технические разработки и решения как для комплектных технологических линий, так и для модернизации действующих плитных производств.
Особое место было уделено развитию прессов непрерывного действия нового типа Dieffenbacher CPS+: Первые две производственные линии, оснащенные прессом нового типа, введены в эксплуатацию и уже работают в трехсменном режиме. Одна линия установлена в хорватском г. Беловар на предприятии компании Cronospan, первая плита на этой линии выпущена в октябре 2016 года. Вторая эксплуатируется в компании «Метро-Плай» г. Прачинбури (Таиланд), там первая плита была выпущена в марте 2017 года. Всего к началу выставки компанией Dieffenbacher продано 11 прессов нового типа CPS+. А на второй день Ligna прямо на стенде Dieffenbacher состоялась торжественная церемония подписания контракта с вьетнамской компанией Thien Lam Dat JSC (г. Бак Гианг, находится в 50 км к востоку от столицы - г. Ханоя) о поставке под ключ завода по производству плит MDF.
«11 лет назад мы организовали плантации быстрорастущих деревьев с целью в дальнейшем начать производство продукции из их древесины, - рассказал председатель правления компании Thien Lam Dat Данг Куок Лич. - В течение нескольких лет мы объездили более 30 заводов в Европе, перенимая опыт, изучая технологии и выбирая лучшего поставщика для своего проекта. Мы непременно хотели, чтобы все оборудование, которое мы установим, было сделано в Европе. Итогом долгих поисков стало наше партнерство с Dieffenbacher». В ответной речи член управляющего совета Dieffenbacher Кристиан Диффенбахер отметил, что горд сотрудничеством с вьетнамской компанией и уверен, что оно очень скоро принесет свои плоды, и новый завод MDF будет успешным.
Основу технологической цепочки завода составит пресс CPS+, также Dieffenbacher берет на себя оснащение всего производства - от биржи сырья до участка упаковки готовой продукции и энергетического хозяйства. Сырьем для плит MDF станет древесина акации с плантаций Thien Lam Dat. Старт проекта намечен на середину 2018 года.
Компания S. Kijchai Enterprise PCL из г. Районг (примерно в 200 км на юго-восток от столицы Таиланда - г. Бангкока) также подписала на выставке контракт с Dieffenbacher, оборудование которой необходимо для наращивания мощностей завода этой тайской фирмы. S. Kijchai Enterprise PCL в течение пяти последних лет выпускала плиты MDF на оборудовании Dieffenbacher, после чего было принято решение расширить производство за счет приобретения линии THDF. «Положительный опыт сотрудничества с немецкими машиностроителями подтолкнул нас к тому, чтобы снова выбрать Dieffenbacher в качестве поставщика оборудования для нового проекта», - сказал во время подписания договора генеральный директор компании Kijchai Вичай Сангвонкит.
Для германского производителя это пятый проект в Таиланде за последние два года. На линии, в составе которой 28-метровый пресс непрерывного действия, будут производить плиты толщиной от 1 до 32 мм. Сырьем станет древесина каучуковых деревьев, выращенных на плантациях. С помощью новой линии тайская компания рассчитывает вдвое увеличить выпуск продукции и закрепить за собой позицию одного из ведущих производителей древесных плит в своей стране.
Большой интерес посетителей стенда Dieffenbacher помимо прессов CPS+ вызвали и другие технические новинки. В их числе - новый оптимизатор потока материала FlowOptimizer, который обеспечивает равномерное распределение подаваемой щепы по всему объему камеры с помощью специального ножевого кольца для 3D-измельчения. Существенно сэкономить потребление клея позволяет новая система осмоления волокна EVOjet M 2.0, которая используется в технологических линиях производства плит MDF. Внесла свой вклад фирма Dieffenbacher и в развитие мирового тренда «Индустрия 4.0». Для дальнейшей «дигитализации» процесса изготовления древесных плит предлагается внедрение в производство активных исполнительных элементов и сенсоров, а также создание эффективных коммуникационных сетей по всей производственной линии. Потребители получают не только больший, чем до использования новинок, объем данных, но и, что особенно важно, более точную и значимую информацию, касающуюся актуального состояния технологической линии, которая нужна для принятия решений по оптимизации работы линии. Вся важная информация может передаваться не только в кабину операторов, но и на внешние электронные устройства и мобильные девайсы.
В качестве перспективного сервисного решения клиентам представлен MyDieffenbacher - новый электронный центр поддержки, который будет работать в течение всего жизненного цикла приобретенного оборудования. На интернет-портале будет содержаться вся информация об оснащении заводов, которая станет пополняться по мере введения в эксплуатацию новых предприятий; с его помощью каждый клиент фирмы сможет оперативно получать ответы на все вопросы, возникающие при использовании оборудования Dieffenbacher.
Есть у компании и новые достижения в области вторичной переработки древесины: Для завода компании Pfleiderer AG в немецком г. Ноймаркт была разработана концепция, позволяющая заказчику значительно увеличить долю вторичной древесины, которая используется в качестве сырья для изготовления плит ДСП, при сохранении постоянно высокого качества выпускаемой продукции, и тем самым существенно повысить экономическую эффективность производства.
Компания EWD (Германия) презентовала работу нового программного обеспечения и системы автоматизации, разработанных для поставляемых лесопильных заводов. Анонс этой разработки состоялся на предыдущей выставке Ligna, и сегодня программный продукт eWOOD уже поставляется в комплекте со всеми лесопильными линиями EWD.
Дополнением к системе eWOOD стал программный модуль «Индустрия 4.0», который обеспечивает беспроводной обмен данными между современными средствами связи (ноутбуком, смартфоном, планшетом) и программой eWOOD. Модуль позволяет осуществлять дистанционное наблюдение за процессом лесопиления, в том числе и при помощи систем видеонаблюдения. Главным его достоинством является возможность передачи производственных заданий на линию и сбор результатов их выполнения с учетом всех необходимых показателей (объема, периода выполнения, номенклатуры, стоимости и т. д.).
Фирма Felder KG (Австрия) не обошлась без инъекции креативности в экспозицию Ligna 2017. Машины и инструмент группы компаний из города Халль располагались в тесном соседстве с шумными и яркими итальянцами из SCM, что в некоторой степени было не на руку тирольским машиностроителям. А между тем, знающие и заинтересованные посетители не проходили мимо отлично зарекомендовавших себя станков под брендами Felder и Format. Один из этих станков - новый обрабатывающий центр с ЧПУ Format-4 profit H500 - стал несомненной «жемчужиной» стенда.
Производственная гибкость давно уже стала притчей во языцех на лесопромышленных смотрах. В том числе она может проявляться и в возможности обработки на одном станке наряду с древесными материалами ряда других материалов - и для этого 5-осевой обрабатывающий центр подойдет как нельзя лучше, помогая небольшим универсальным предприятиям и мастерским, выполняющим индивидуальные заказы, существенно снизить эксплуатационные расходы на приобретение специальных инструментов и агрегатов. Format-4 profit H500 обеспечивает индивидуальный раскрой заготовки и полностью автоматизированное производство при довольно небольших инвестициях; высокопроизводительный шпиндель фрезы позволяет получать идеальные результаты независимо от материала. Машина с 18 сверлильными шпинделями, каждый из которых может активироваться независимо от других, и интегрированным пазовым пильным агрегатом предоставляет пользователю почти неограниченные возможности для технического творчества, обеспечивает большое разнообразие видов обработки и максимально короткие производственные циклы.
Представитель французской компании Forezienne MFLS Юрий Сильверстов рассказал:
- Из наших новинок на выставке хочу отметить ленточные пилы для небольших горизонтальных пилорам: Hyper Cut Forestill - со стеллитированными зубьями, а также Hyper Cut TCT Forestill - с твердосплавными напайками. Повышенная износостойкость материала гарантирует долговечность работы режущего инструмента. Форма твердосплавных зубьев пилы обеспечивает высокое качество пиления, в результате чего качество поверхности пропила близко к качеству шлифованной поверхности. Ленточные пилы со стеллитироваными зубьями можно эксплуатировать 6-8 ч до перезаточки, а пилы с твердосплавными напайками 20-25 часов до перезаточки.
Для Джампьеро Маури Ligna стала трибуной для объявления о рождении промышленной группы компаний Giardina Group (Брианца, Италия). В нее вошли компании Mauri Macchine, Officine Aeromeccaniche Giardina, Ventilazione Italiana, Giardina Finishing и MM Store (коммерческий портал для онлайн-продаж запасных частей и оборудования для отделки поверхностей). Формирование группы г-н Маури начал семь лет назад с приобретения Giardina Finishing. Теперь этот процесс доведен до логического завершения.
По словам г-на Маури, цель создания индустриальной группы - укрепление позиций бизнеса на национальном и международном рынках с постепенным вхождением в число компаний-лидеров в сфере производства отделочного оборудования: «В нынешнем году наш оборот превысил 16 млн евро, и думаю, в 2018 году мы шагнем за 20 млн. С нашим оборудованием и стремлением к достижению четко поставленных целей мы способны на великие дела».
На стенде площадью 400 м2 в Ганновере Giardina Group представила новую номенклатуру продукции под новым именем, а также свой новый логотип, который постепенно распространится на все оборудование, выпускаемое компаниями, входящими в группу.
Объединив бренды, Giardina Group получила возможность использовать огромную общую клиентскую базу и предложить рынку широкий ассортимент оборудования - начиная с классических автономных станков и заканчивая гибкими комплексными линиями для производства разнообразной продукции - от окон до мебели и от крупных агрегатов для покраски балок до специальных машин по обработке стекла. Древесина и стекло - вот два основных материала, на обработке которых специализируется Giardina Group.
В числе ближайших задач по реорганизации и интеграции компаний - сосредоточение производства в местечке Фиджино Серенца, где изначально располагался завод Giardina, а склады и логистическое подразделение займут площадку компании Mauri Macchine в городе Черменате. К концу года, по планам главы компании, штаб-квартира группы должна быть полностью модернизирована с учетом новых потребностей, созданы шоурум, лаборатория, тестовая площадка и подразделение дизайна и инноваций.
Для большинства предприятий важнейшей задачей на пути к 4-й промышленной революции является получение в реальном времени значимой для производства информации с целью организации максимально эффективного и надёжного управления производственным процессом. Как рассказал руководитель филиала фирмы GreCon в РФ и странах СНГ Алексей Васичев, на выставке компания представила полный спектр контрольно-измерительного оборудования для плитной промышленности, а также установки искрогашения для защиты пневмотранспорта от возгораний и взрывов.
«Контрольно-измерительные системы от Fagus-GreCon всё чаще подключаются к специфической для каждого заказчика системе общего управления производственным процессом. Так, например, Formator контролирует равномерное распределение материала в формирующемся ковре, а это одна из важнейших предпосылок для обеспечения неизменного качества при изготовлении плитной продукции. Процесс регулирования базируется на обнаружении отклонений в характеристиках материала перед прессом, уже на формирующей станции. Полученные данные измерений автоматически, через соответствующий контур регулирования возвращаются на расположенный впереди инструмент формирования ковра (в данном случае на сегментированный скальпер). Сегментированный скальпер незамедлительно выравнивает распределение материала путем направленной регулировки валов, которые подъемом или опусканием устраняют отдельные отклонения. Это обеспечивает достижение заданного значения профиля плотности по всей ширине ковра.
С помощью Fiberview, оптической системы определения качества волокна в режиме реального времени, создается тот показатель качества, который будет автоматически регулировать настройку дисков рафинёра».
Инновационные продукты и услуги GreCon привлекли внимание многих специалистов, на стенде за время проведения выставки было проведено почти 800 переговоров.
Итальянская компания Greda привезла на выставку три своих машины - Mitika V, Poker V и ставший премьерой Ligna 2017 5-осевой рабочий центр Diva. Он является отличным решением для небольших и средних предприятий, где ценят компактность габаритов (станок занимает меньше 10 м2), богатый функционал в сочетании с высокой производительностью. Diva можно использовать как для выпуска небольших партий изделий, так и для обработки больших партий деталей благодаря возможности подключения автоматических систем загрузки и разгрузки. Обрабатывающий центр оснащен системой автоматического позиционирования заготовок и интеллектуальным рабочим столом.
Конструкции и возможности всех трех машин соответствуют принципам Industry 4.0 и могут взаимодействовать при помощи интернета и облачных хранилищ с другим оборудованием и программным обеспечением. Собственное ПО компании GreCam, установленное на всех машинах, позволяет оперативно управлять всеми рабочими процессами, проектировать изделия и моделировать этапы их обработки в 3D-проекции.
- Ганноверская выставка - большой вызов и вместе с тем - амбициозный проект, - считает председатель правления компании Greda Марианна Даскини. - Преодолев трудности работы в непростые годы и достигнув коммерческого успеха, мы решили выйти за пределы своего региона и, применив агрессивную стратегию продвижения, использовать отличную возможность для представления своей продукции всему миру. Мы планируем самостоятельно или с помощью партнеров и дилеров осваивать все основные профильные рынки - от Китая до России, от США до Ближнего Востока, от Центральной Европы до Скандинавии.
Экспозиция компании Grenzebach Maschinenbau GmbH (Германия) на Ligna была сфокусирована на инновациях в процессе сушки шпона, автоматизированных управляемых транспортных средствах для внутрилогистических процессов и технологиях производства энергоэффективных строительных материалов.
Современные сушильные линии с автоматическими штабелерами предназначены для обработки больших объемов листов шпона разного размера. Важным компонентом в этом процессе является сканер шпона FPI Grenzebach для непрерывной и надежной оценки качества. Сканер обнаруживает все дефекты, и в соответствии с установленными критериями качества система в кратчайшее время определяет, на какую укладку будет отправлен отсканированный лист. Посетители Ligna увидели сканер с многоканальной технологией в действии.
Компания Holz-Her представила NEXTEC - новую технологию на базе собственного ПО, призванную коренным образом преобразовать работу мебельщиков. Без сложного программирования для ЧПУ индивидуальную мебель под заказ теперь можно изготавливать несколькими кликами компьютерной мышки. C какими бы сложными операциями ни справлялся станок, в результате самым главным показателем его работы всегда остается качество конечного продукта. Промышленнику, использующему машины с ЧПУ, снабженные технологией NEXTEC, по заявлению производителя, волноваться совершенно не о чем: уникальное программное обеспечение позволяет легко выбрать нужный тип изделия, задать размеры, выбрать материалы для обработки и число выпускаемых единиц. И это все, что понадобится для создания программы-команды для ЧПУ. Как только требуемое сырье будет подано на обрабатывающий центр с NEXTEC и будет нажата кнопка «пуск», автоматика возьмет работу на себя - вся обработка может быть завершена за один проход, с заметной экономией времени без ущерба для качества.
Экспозиция HOMAG Group (при всем искреннем уважении к другим экспонентам) стала технологической и идейной доминантой павильона № 14. Хочется искренне аплодировать тому, насколько удачно компания преподнесла свои достижения и разработки на выставке!
Фокус был сделан на инновациях, предназначенных не для сегодня - но для завтра. Неслучайно в центре площадки был расположен «Инновационный центр», в котором были представлены «умные» приложения в духе концепции Industry 4.0, широкие возможности использования «интернета вещей», полное обновление всего портфолио программного обеспечения и других электронных продуктов. И главное - новая цифровая платформа tapio для индустрии производства мебели и деревообработки; которая, думаю, еще долго будет обсуждаться игроками рынка, ведь она представляет интерес для представителей как крупного, так и среднего и малого бизнеса. «Сегодня, как никогда прежде, важно согласовывать все детали и параметры в цепочке создания стоимости; необходимо координировать весь процесс - от поступления вводных данных до технологических операций и последующих действий с готовой продукцией; tapio предназначена для этого, - отмечают создатели платформы. - Это и компетенции в области производства и эксплуатации машин, и экспертиза программного обеспечения, консалтинговые услуги, которые могут быть использованы в работе деревообрабатывающими компаниями, оправдывая их инвестиции в будущее».
Чтобы понять, как работает tapio, в чем польза и революционность этой разработки, посетители стенда могли прямо на стенде скачать приложение на свои смартфоны и увидеть на экранах оперативную информацию о состоянии оборудования на стенде в реальном времени, а также сообщения и сигналы, поступающие от этих «умных» станков.
Разумеется, все станки Homag, показанные на Ligna, были готовы передавать данные в «облако» tapio, а оборудование с функцией CloudReady было оснащено необходимой технологией для подключения к платформе «Интернета вещей» (IoT).
«55 машин, устремленных в будущее» - так называлась экспозиция Homag, и с этим трудно спорить: фактически для каждого сегмента деревообработки на 5 тыс. м2 выставочного пространства было предложено какое-либо решение на перспективу. В этом обзоре мы можем только пунктирно обозначить новации, предложенные посетителям специалистами концерна из Шварцвальда под слоганом «Homag - ваше решение» (Your Solution).
На выставке компания впервые представила четырехсторонние станки, оснащенные интерфейсом управления powerTouch. Станки новой серии LPP 300 с ЧПУ предназначены для строгания заготовок перед изготовлением профиля в производстве окон. Особенность LPP 300 - использование системы комфортного управления powerTouch, адаптированной к характеристикам станка. Система обеспечивает управление инструментом и интерактивное создание настроек (программных шаблонов, которые пользователь может сохранять и использовать в дальнейшем). Кроме того, у станков новой серии, которые доступны в разных классах производительности и могут быть оснащены пятью, шестью и даже семью шпинделями, регулируемые подача и скорость шпинделей, система управления инструментом и зажимом шпинделя proLock.
Роботизированный раскроечный модуль HPS 320 flexTec, дебютировавший на предыдущей Ligna, был показан в обновленном виде - теперь он наделен функцией автоматического складирования деталей. Программный алгоритм позволяет удаленно управлять операциями без участия человека даже в том случае, когда модуль не подключен к производственной линии.
Новый сортировочный центр TLB 321 отличает большое разнообразие вариантов организации потоков заготовок. По всей цепочке процессов TLB 321 накапливает, сортирует и распределяет поток материалов на производстве. Его несомненные плюсы: удобство и увеличенные интервалы техобслуживания, высокая эффективность использования стеллажей, гибкость за счет настраиваемых стратегий материалопотока.
Модуль woodStore - «мозг» логистической системы Homag. Новая версия woodStore 7 усовершенствована с целью обеспечения простоты использования, расширения возможностей оптимизации управления материалами в единой системе «склад - станок» и повышения безопасности пользователей.
Компания адаптирует промышленные решения для малого бизнеса и развивает технологии мелкосерийного производства для будущих задач. Пример: оснащение функцией module45 даже младшей модели раскроечного центра HPP-130 позволяет выполнять точный раскрой под углом. LED-cистема помощи оператору простыми символами и подсветкой станка подсказывала, что делать с заготовкой. Сканнер системы распознавал каждую деталь и проецировал стрелки и символы согласно размерам.
Технология airTec для кромкооблицовки с «нулевым» швом теперь доступна для станков со скоростью подачи от 8 до 25 м/мин. Этот агрегат можно использовать на оборудовании начиная со станков базового уровня серии Ambition вплоть до высокоскоростных станков серии KAL 370. Достоинства: низкий уровень шума, эффективность и экономичность, обеспечение равномерного потока воздуха, управление с помощью системы powerTouch, снижение энергопотребления на 10-30% по сравнению с обычными технологиями.
Кромкооблицовочный станок серии Ambition - оптимальное решение для облицовки кромок по технологии «нулевого» шва. Станок оснащен агрегатом airTec и новым агрегатом для использования ПУР-клея. Возможности кромкооблицовочного станка дополняются возможностями центра с функцией module45 для раскроя плит под углом, а также корпусного пресса и обрабатывающего центра с ЧПУ для вертикального сверления.
В Ганновере было представлено новое поколение лазерной системы кромкооблицовки laserTec, позволяющей получать идеальный «нулевой» шов. Инженерам Homag удалось создать систему, которая обеспечивает 20% экономии электроэнергии за счет использования диодов, автоматизирован переход с расплава на лазер, сведена к нулю возможность перегрева, оптимизированы параметры лазерного светового пучка. Простая в управлении и надежная система чрезвычайно удобна для сервиса и обслуживания.
Новая тандемная концепция гибкого производства элементов кухни представлена двумя кромкооблицовочными станками K 610. Их основу составляют два последовательно установленных мощных фуговально-фрезеровальных агрегата, оснащенных инструментами с гидравлическими зажимами для подготовки заготовок без сколов. Модуль с автоматической сменой кромочного материала позволяет использовать 48 разных кромок, которые приклеиваются полиуретановым клеем. Компактный возвратный конвейер с поворотом заготовок занимает значительно меньше площади в сравнении с предыдущими вариантами.
Вниманию посетителей и специалистов была также предложена новая серия кромкооблицовочных станков BMG 110 для индивидуального производства. Станок доступен с трех сторон, что обеспечивает свободу действий оператора. Защитный кожух закрывает портал со всех сторон, станок может быть интегрирован в производственный процесс без устройства дополнительных ограждений и принятия защитных мер. Много места для инструментов: новый магазин обеспечивает быстрый доступ к инструментам (внешняя тарелка с 24 ячейками, внутренняя - с 8 ячейками).
Специалисты концерна разработали новую автоматизированную технологию нестинга с различением нулевых точек. Для этого в декоре определяются так называемые нулевые точки. Они оцифровываются с помощью камеры, после чего запускается программа обработки плиты.
Вызвал интерес у посетителей выставки и новый продукт Homag - покрасочные камеры для обработки поверхностей мебели, созданный специально для малых и средних компаний, которые хотят внедрить нанесение лакокрасочного покрытия распылением.
На Ligna 2017 состоялась мировая премьера новой программной платформы от Homag: посетители могли увидеть, как настроить индивидуальные решения для малых и крупных предприятий на основе модульного комплекта для интегрированных производств. Производители, ориентированные на каталоги (мебель для кухонь, офисов, жилых помещений, ванных комнат), с помощью Configurator3D смогут легко и быстро построить графическое изображение заказа. Трехмерный конфигуратор позволяет, автоматически генерируя технические характеристики, получать индивидуальные проекты мебели из неограниченного числа возможных вариантов.
С помощью ПО для дизайна мебели Designer3D и интернет-конфигуратора DesignerWEB можно увязать производство со всеми каналами сбыта - розничной торговлей, прямыми продажами, онлайн-магазинами: используя библиотеки электрооборудования и декоративных элементов, покупатель планирует обстановку жилого помещения, а приложение виртуальной реальности визуализирует ее, Designer3D взаимодействует с Configurator3D - и готовый проект передается в производственную систему.
Оптимальная организация и прозрачность производственных процессов достигаются с помощью новой системы контроля производства ControllerMES с интегрированной программой оптимизации Schnitt Profi(t), обеспечивающей тщательное планирование и мониторинг производства, а также организацию информационных потоков. Множеством новых функций дополнены woodCAD|CAM 12.0, woodWOP 7.1 и другие программные пакеты Homag.
Одной из важных новостей группы Homag на выставке в Ганновере стали изменения в организационной структуре ГК: все более глубокая интеграция ее составных частей привела к решению объединить их под единым брендом - отныне Holzma, Butfering, Weeke, Brandt, Friz, Homag Automation выступают под брендом Homag. Все оборудование, выпускаемое предприятиями, входящими в ГК, будет носить хорошо знакомый специалистам логотип концерна. По замыслу руководства ГК, это позволит упростить взаимодействие с клиентами, поставщиками и партнерами, повысить четкость коммуникации в любой точке мира и узнаваемость бренда.
Оборудование для деревянного домостроения от компании Weinmann демонстрировалось в павильоне № 13.
В частности, вниманию посетителей и специалистов был представлен WMS 060 - современный базовый станок с ЧПУ для домостроительного производства. Мультифункциональный мост WMS 060 с высокой точностью формирует и обрабатывает деревянные стены, в полностью автоматическом режиме создавая дверные и оконные проемы, ниши для розеток и пр. С помощью WMS 060 можно изготовить элементы для любой части дома - будь то стена, крыша, потолок или фронтон. Причем вся установка, включая рабочий стол, занимает лишь 90 м2.
Премьерой для автоматизированного каркасно-панельного домостроения стали новации в конструкции раскроечного центра HPP 300 multiTec, что позволяет выполнять распил, сверление и фрезерование за один проход; теперь станок оснащен интерфейсом COBUS NCAD, который генерирует производственные данные из планов CAD/CAM и передает их в программу оптимизации раскроя Schnitt Profi(t), откуда они передаются прямо в ЧПУ раскроечного центра. Если используются несколько станков, COBUS NCAD самостоятельно решает - на каком станке какой компонент дома должен быть изготовлен.
На стенде IMA Schelling Group площадью 3600 м2 было организовано полноценное автоматизированное производство единичных мебельных деталей, действующее без участия человека. Производительность участка раскроя панелей - до 800 деталей в смену. Оптимизация карты раскроя и вторичная обработка отходов пиления позволяют существенно сократить объем деловых отходов производства.
Интегрированный пильный центр (длина реза - 3,3 м, подъем пильного диска - 105 мм, max толщина обрабатываемой плиты - 60 мм) оснащен узлом независимых резов DUPLUS 2. На выходе из пильного центра автоматический принтер печатает этикетки со штрихкодом и наклеивает их на детали, после чего они поступают на сортировку и с помощью 6-осевого антропоморфного робота ABB с вакуумными захватами (усилие прижима регулируется в зависимости от панелей) распределяются по стеллажам автоматического склада Schelling vs 12 емкостью до 1000 деталей. Далее детали каждого вида по очереди подаются на кромкооблицовочную линию. Между отдельными участками линии выделены небольшие буферные зоны, что помогает согласовать и гармонизировать работу разноскоростных машин, поддерживать баланс и общий непрерывный ритм производства.
На участке кромкооблицовки работает станок Combima с автоматическим манипулятором и возвратным транспортером. За ним установлен сверлильно-присадочный центр IMAGIC с независимым управлением сверлильных шпинделей и минимизированным временем переналадки. Центр производительностью до 30 панелей в минуту может выполнять пазование, а также обработку деталей с шести сторон, установку шкантов в торцевую кромку (при помощи специальных агрегатов).
Новая серия кромкооблицовочников Novimat Compact была представлена станками Novimat Compact R3 для облицовывания кромкой толщиной до 3 мм и Novimat Compact L12 (как следует из маркировки станка, допустимая толщина кромки 12 мм). На станках используются ЭВА и ПУР-клеевые системы, бесступенчатая регулировка скорости подачи (до 20 м/мин.) и система Quick-lock быстрой замены клеящих узлов. Опционально Novimat Compact R3 можно дооснастить агрегатом IMALux для бесшовной лазерной кромкооблицовки*.
Главной новинкой в области раскроя плит стала компактная (занимает около 120 м2 площади цеха) и скоростная пильная линия Combi.cut 1, производительность которой - до 3500 разных деталей в смену. Здесь вслед за продольным раскроем фрезерная группа из пяти независимых агрегатов выполняет поперечные резы. Смена инструмента для обработки задних углов плиты, снятия фасок и т. п. осуществляется автоматически. Специальные захваты гарантируют точное позиционирование заготовки и выверенную геометрию изготавливаемых мебельных деталей.
Performance.CUT - компактный станок, сочетающий все плюсы нестинга со скоростью пильных центров. Базой для его создания стало инженерное переосмысление технологии высокопроизводительных обрабатывающих центров BIMA Cutting. Новая машина должна, по замыслу разработчиков, порадовать экономных производителей при обработке даже самых небольших партий изделий. В Performance.CUT возможна автоматическая смена инструмента во время работы за минимальный отрезок времени.
Чтобы оставаться в русле мировых технических тенденций, компания IMA приняла решение о создании отдельного специализированного подразделения - IMA Robotic Engineering, в обязанности сотрудников которого входит как обслуживание и программирование роботов на выпускаемых автоматических линиях концерна, так и перспективные разработки в этой области, открывающей широкие возможности для применения роботов в деревообработке.
Не осталось без упоминания в разговоре с Сергеем Панферовым, генеральным директором ООО «ИМА-рус», представляющим в нашей стране интересы IMA Schelling Group, недавно завершившееся слияние компаний IMA Klessmann GmbH (Германия) и Schelling Anlagenbau GmbH (Австрия) в IMA Schelling Group. Этот важный шаг призван улучшить интеграцию фирм, входящих в ГК, объединить их производственный потенциал и расширить спектр выпускаемого оборудования.
Более 1500 посетителей со всех уголков мира посетили стенд Imal-Pal Group на Ligna 2017. Руководство ГК удовлетворено результатами участия компании в выставке - портфель заказов Imal-Pal пополнился договорами на поставку оборудования на сумму 11 млн евро. Это рекордный показатель, который достигнут впервые за все время участия компании в подобных мероприятиях.
Посетители проявили большой интерес к шоуруму, где было продемонстрировано различное оборудование, начиная от компактного лабораторного влагомера до 7 метрового качающегося сортировщика HD на гидроподушках, а также к пеллетному прессу Dynapelletpress производительностью 12 т пеллет/час и дробилка SRC14.690_EVO4 для получения стружки, используемой в изготовлении древесно-стружечных плит (ее мощность - более 15 т/ч); на это оборудование поступило несколько заказов. Подписаны договоры на поставку систем парового прогрева ковра Dynasteam (более 91 подобной системы уже продано по всему миру), еще три заказа поступило на системы высокого давления Hi-Jet MDF, ДСП и OSB (более 107 проданных).
Кроме того, на стенде общей площадью 1600 м2 было представлено более 30 различных приборов лабораторного и онлайн-контроля производства начиная с полноформатного дефектоскопа древесных плит FBC-200 и заканчивая новой лабораторной концепцией «all-in-one 4.0 smartlab». Другие технологические решения и проекты под ключ для производства кубиков для поддонов, пеллет, изоляционной плиты и прессованных поддонов также вызвали большой интерес у посетителей.
И еще - основатели группы Imal-Pal Паоло Бенедетти и Лорис Занази получили специальную награду за преданность выставке в Ганновере «40 лет участия в Ligna».
Компания imos (Германия), которая с 1993 года занимается созданием передового программного обеспечения для производства мебели и обустройства интерьеров помещений и поставляет решения для более чем 4000 предприятий по всему миру, показала на выставке модуль виртуальной реальности. Каждый желающий, одев 3D-очки, мог в режиме реального времени виртуально «походить» внутри интерьера, определиться с расстановкой элементов, стилем, оценить удобство пользования мебелью, «открыть» двери шкафов, «выдвинуть» ящики и «достать» одежду или посуду. Новинка от imos позволяет дизайнеру в салоне продаж разработать проект, максимально соответствующий желаниям заказчика, а самому салону выгодно выделяться среди прочих.
imos одинаково удобен для разработки как индивидуальной, так и серийной мебели. Можно точно определить параметры по сути любых элементов конструкции. К примеру, при достижении критической ширины проема можно предусмотреть установку дополнительных ребер жесткости и крепежа. Удобный интерфейс позволяет быстро выполнить работу и получить удовольствие от проектирования.
В состав программы входят модули, позволяющие не просто осуществлять продажи в салоне или через интернет, но и автоматически формировать программы для станков с ЧПУ без «переконструирования» изделий на производстве.
Новинка от компании Incomac (Италия) - электронное устройство Socrates Advanced для контроля процесса сушки пиломатериалов, в состав системы входят процессор с тачскрином для управления каждой отдельной сушильной камерой и персональный компьютер последнего поколения. Socrates Advanced может поставляться клиенту в одной из двух версий - проводной или беспроводной.
Компьютер может управлять технологическими режимами в 32 сушильных камерах. Процесс управления полностью автоматический, а разные интуитивно понятные экранные образы позволяют управлять циклом сушки даже если оператор не является экспертом. Как программы, так и результаты процедуры сушки визуализируются время от времени схематически и записываются на карту памяти SSD и на жесткий диск. Память устройства может содержать неограниченное число программ.
Программы могут быть созданы как оператором, так и автоматически системой, исходя из введенных в память ПК характеристик древесины, предназначенной для сушки (порода, толщина, влажность и т. д.). Имеется возможность настроить дневную и недельную программы для контроля экономии энергии, используемой вентиляторами (если они оборудованы инверторами), и тепловой энергии.
При использовании опциональной карты возможно визуализировать и сохранить настройки потребления электрической и тепловой энергии, если сушильная камера оборудована специальными измерительными устройствами. Каждая функция может управляться как автоматически, так и вручную.
Все записанные данные преобразуются в графики, и можно выбрать, какой график визуализировать, а также цвет, данные и промежуток времени для анализа.
Каждая сушильная камера снабжается электронным устройством, при поломке или выключении управляющего компьютера все устройства продолжают работать и все программы остаются в памяти процессора, который управляет работой каждой камеры, и оператор может работать без компьютера. В случае перерыва в электроснабжении система перезапускается автоматически с последней фазы, которая была в работе на момент остановки.
Компьютер может быть установлен на расстоянии до 1000 м от камер, подключенных к нему посредством кабеля. Устройства Socrates Advanced могут быть подключены через Интернет к одному или более удаленным компьютерам или к серверу Incomac для оказания дистанционной помощи. Для подключения можно использовать такие программы, как Team Viewer, LogmeIn и другие.
Вся информация о выполняемом цикле сушки записывается через равные промежутки времени (по выбору оператора - минимум через 5 мин., максимум через 16 ч) и выводится на экран. Система оснащена сигналами оповещения, которые сообщают о возможных остановках в работе или нарушении режимов.
Socrates Advanced может быть использован для записи процесса термообработки палет и материалов для упаковки.
Компания Italpresse (Италия) провела на Ligna 2017 презентацию успешно реализованного проекта по установке полностью автоматической линии для изготовления элементов внутренней отделки автодомов (кемперов) Laika Caravans Spa.
Линия установлена на новом заводе компании в пригороде Флоренции и воплощает в себе самые совершенные технологии в секторе оборудования для отделки, что позволило компании-заказчику повысить эффективность рабочего цикла и, как следствие, увеличить производительность на 40%. Рабочая длина линии - 80 м.
Также компания Italpresse презентовала полностью автоматическую линию холодного прессования с повышенной производительностью для изготовления двух- и трехслойного паркета. В условиях постоянно растущего спроса на деревянные напольные покрытия на первый план выходят предприятия, оборудованные по самому последнему слову техники. Повышение производительности достигается за счет использования роботов на компоновочном участке. Это решение позволяет задействовать минимальное число операторов.
В этом году на выставке Ligna в Ганновере компания Kanefusa представила новую дисковую пилу для форматно-раскроечных станков Kanefusa 300х3.2х2.2х30хz96 D Board-Pro HV. Благодаря использованному для ее изготовления новому твердому сплаву удалось повысить стойкость пилы на 50% в сравнении с моделью Board Pro Plus. Кроме того, разработаны компенсаторы, за счет которых дисковая пила работает еще стабильнее и тише, чем ее предшественница, что позволяет клиенту получать идеальное качество при работе с любыми композитными материалами, а также экономить на приобретении инструмента и его обслуживании.
Продукция японской компании Kanefusa всегда отличалась непревзойденным качеством и являлась эталоном высококачественного инструмента. Благодаря многолетнему опыту, использованию лучших материалов, уникальной технологии производства и соблюдению строгих стандартов в компании производят инструмент, отвечающий самым высоким требованиям современного производства.
Начальник отдела продаж по Восточной Европе шведской компании Kvarnstrands Игорь Лапченко, рассказывая о новинках, старался делать акцент на тех продуктах, которые могут быть интересны покупателям в России: «Для российского пользователя на нашем стенде немало интересных новинок. Взять хотя бы High Speed Cutter - запатентованный инструмент для прямой строжки со специальной системой фиксирования ножей (для каждого ножа свой зажим). На российском рынке мы этот продукт пока не представляли. Он рассчитан на скоростные машины, недавно продали такой инструмент в Германию для строгальной линии со скоростью подачи 600 м/мин. Для машин, которые эксплуатируются в России, мы можем изготавливать уменьшенные версии инструмента. Он очень эффективен, позволяет экономить время, надежен и точен.
Принципиальное отличие «изюминки» нашего стенда - гидроголовки High Speed Cutter - от обычной состоит в том, что у стандартной строгальной головки ножи вставляются в специальные пазы на корпусе и каждый фиксируется своими винтами, которых может быть пять и больше; на новой головке винтов всего два, они установлены не на лицевой поверхности, а с боков корпуса инструмента. Ножи вставляются очень быстро, ведь мы предлагаем не плоские, а рифленые ножи для прямой строжки, которые моментально зажимаются - все сразу - этими двумя винтами. Это новшество обеспечивает серьезную выгоду по времени на перевооружение инструмента, а его деревообработчики умеют ценить.
Каждый из наших инструментов по-своему уникален. Например, особенность популярных цельных фрез HL состоит в том, что на один из зубьев нанесены специальные риски: когда фреза затачивается по передней грани, по ним можно с большим удобством определить и выставить оптимальный угол заточки, заданный заводом-изготовителем. Подобную опцию не предлагает больше никто из производителей.
Специальная конструкция фрез исключает возникновение вибраций, что значительно увеличивает срок службы оборудования, обеспечивает прекрасное качество поверхности готовой продукции, уменьшает число задиров. Цельные заднетылованные фрезы HL предназначены для профилирования различных погонажных изделий, деления заготовки на ламели с одновременным профилированием радиуса по канту (в комплекте с пилами). Процесс деления происходит так: используются три комплекта инструмента, которые выставляются один за другим на шпинделях станка и в результате за один проход получаются четыре-пять реек с радиусом. Эти фрезы мы устанавливаем вместе с пилами нашего партнера - компании Kanefusa. В России подобные фрезы уже приобрели несколько клиентов, а в странах Балтии есть стабильные продажи, на предприятиях в Швеции они эксплуатируются не один год и отлично себя показали, от клиентов получаем положительные отзывы, и на этот инструмент большой спрос. Серьезный интерес вызвали они и на стенде в Ганновере, как раз у посетителей из России, и я очень надеюсь, что этот интерес приведет к реальным сделкам.
Еще один новый для российского рынка продукт - фрезы для браширования. Ими обрабатывают поверхность обшивочной доски, которая потом идет под покраску. Клиенты из России очень интересуются этим инструментом».
Cловенская компания Ledinek Engineering Ltd - наш давний друг. Поэтому было более чем приятно наблюдать за нешуточным ажиотажем на стенде братьев-славян, причем его причиной было не только и не столько желание гостей сфотографироваться возле украсившего площадку деревянного аэроплана, сколько «горячая» новинка - X-Press, пресс для производства CLT-панелей длиной 5-18 м, шириной 2,45-3,55 м и толщиной от 60 до 360 мм. Развитие деревянного домостроения, в том числе высотного, набирает темпы в разных регионах мира, а плиты CLT - один из наиболее перспективных строительных материалов для этой сферы, поэтому интерес посетителей к новой машине был вполне закономерен.
В числе другого оборудования, показанного Ledinek, были давно завоевавшие популярность на рынке оборудования скоростная (до 160 м/мин.) линия сращивания по длине Kontizink M120 (на стенде демонстрировались шипорезный станок и укороченный двухметровый пресс, входящие в состав этой линии), многофункциональный строгально-профилирующий станок Multiplan (может обрабатывать заготовки сечением до 300х160 мм со скоростью подачи до 250 м/мин.), четырехсторонний строгальный станок Stratoplan 6VR-S500 (производительностью до 900 м/мин.), станок Rotoles 400 D-S для прямолинейного одностороннего строгания со скоростью подачи до 45 м/мин. и др.
Компания производит оборудование для обработки массива древесины более 65 лет и является постоянным участником Ligna на протяжении последних четырех десятилетий.
«Мы рады показать коллегам по отрасли как те машины, которые создали устойчивую репутацию Ledinek, так и самые свежие разработки, - сказал глава компании Павел Лединек. - А национальный вечер с традиционными блюдами и музыкой, который мы организовали на стенде, был призван показать, что в Словении не только умеют делать добротное оборудование для деревообработки, но и гостеприимно встречать друзей».
Компания Leitz, следуя в фарватере идеологии «умного производства», свои новые разработки обозначила как «интеллектуальный инструмент». Решения Intelligent Tooling, в которых используются встроенные чипы и специализированные QR-коды, обеспечивают отслеживание режимов обработки древесины прямо в процессе производства. Такая важная информация о параметрах детали и режимах обработки, как максимальная скорость и направление вращения, установочные размеры, скорость подачи и т. д. в буквальном смысле слова встроена в чипы режущего инструмента, позволяя оптимизировать функции обработки и непосредственным образом влияя на производительность, качество и эффективность (в том числе и энергетическую, поскольку инструменты всегда используются в оптимальных режимах, наиболее точно соответствующих стабильным и экономичным производственным процессам). Электронная начинка позволяет: оценить состояние (износ) инструмента, определить оставшийся ресурс, включая прогноз об оптимальном времени замены, а также необходимые параметры обслуживания. Интеллектуальный инструмент непрерывно собирает данные, регистрируя критическую операционную информацию для оптимизации будущего производства. На основе собранных данных машина может устанавливать наиболее эффективные параметры обработки. Дополнительные плюсы связи машины и обрабатывающего инструмента состоят в повышении безопасности работы, безотказной перезагрузке инструментов, возможности моделирования процессов обработки.
Руководители компании - Юрген Кёппель (председатель совета директоров), Гюнтер Каммель (коммерческий директор) и Андреас Киссельбах (R&D директор) - на встрече, устроенной для журналистов в рамках выставки, в числе наиболее передовых решений от Leitz отметили: высокоскоростную инструментальную систему обработки профиля ProfilCut Q, ShrinkTec (гибридные и интегральные технологии), создание индивидуальных комплексных решений (концевые фрезы EdgeExpert + фуговальные фрезы + малошумные пилы WhisperCut), высокопроизводительный инструмент линеек Premium и Excellent, высокое качество финишной отделки на обрабатывающих центрах при помощи циркульных пил Katana, пильные диски Leitz BrillianceCut для обработки композитных материалов (они обеспечивают настолько качественный раскрой, что пользователь может полностью отказаться от шлифования), стойкое покрытие Marathon, значительно (в 3-6 раз по сравнению с инструментами без покрытия) увеличивающее срок службы инструментов, систему комплексного обслуживания Complete Care и многое другое. Самое серьезное внимание спикерами было уделено развивающейся тенденции в деревообработке - обработке пальмовой древесины. Для производителей обрабатывающего оборудования и инструмента этот материал - самый настоящий вызов: ведь, помимо наличия в мягкой и рыхлой древесине жестких волокон (1-2% ее состава), это хаотично разбросанные вкрапления силикатов с высокими абразивными свойствами. Однако необходимо считаться с тем, что плантации масличной пальмы в мире занимают 20 млн га, а ежегодный объем заготовки пальмовой древесины - 120 млн м3, что с учетом всего лишь 25-летнего возраста достижения спелости пальмовых деревьев диктует необходимость работы в этом направлении. Достоинств у древесины масличной пальмы немало: широкий диапазон плотности (180-650 кг/м3) для разных вариантов использования, отсутствие сучков, высокая прочность на сжатие по направлению волокон, изотропия в сечении, низкая горимость, отличные теплоизоляционные и акустические свойства. Наконец, пальмовая древесина просто красива! Поэтому хорошо подходит и для производства пиломатериалов, используемых в изготовлении мебели и строительстве, и для дверных полотен.
Готовясь представить свои новации на Ligna, специалисты Leuco Ledermann GmbH & Co. KG. сосредоточились на пяти основных направлениях: повышении качества обработки, улучшении рабочих условий (в частности, снижении уровня шума), гибкости в использовании инструмента (получении большего числа возможностей обработки с помощью одного инструмента), оптимизации и совершенствования производственных процессов. В рамках этой концепции компания предложила вниманию посетителей новые алмазные фуговальные фрезы airFace, алмазные дисковые пилы с покрытием для раскроечных центров Topcoat, концевые фрезы Leuco p-System с малым диаметром рабочей части, концевые фрезы для обработки плит MDF и мультиплекса по технологии нестинга, насадные фрезы для строгания и пазования, систему инструментального учета и контроля ToolCloud.
Представленный инструмент серии р-System с увеличенным осевым углом позволяет с высоким качеством обрабатывать широкий спектр материалов при разной скорости подачи на стандартных позиционных станках и на обрабатывающих центрах. Режущие пластины на фрезах p-System установлены с осевым углом 70°, что гарантирует весьма высокое качество фрезерования и выход инструмента без сколов. Подобные модели инструмента прекрасно зарекомендовали себя при высокоскоростной обработке древесины твердых пород, древесных плит с покрытиями, фрезеровании кашированных, ламинированных и деталей, окрашенных ЛКМ.
Главное в технологии p-System - эффект «тянущего» реза, который похож не на обычное фрезерование, а на строгание. В процессе обработки деталей образуется легкая сливная стружка, которая подхватывается и удаляется потоком воздуха систем аспирации. Таким образом р-System не только успешно решает вопросы качества реза, но и гарантирует чистоту в рабочей зоне.
Модернизированный инструмент р-System может выбирать паз минимальной шириной до 8 мм, без вырывов на поворотах, входе и выходе фрезы, а также осуществлять продольное и поперечное пазование изделий из древесины мягких и твердых пород, плитных материалов. Инструмент для прямолинейной обработки профильный, теперь пользователи подобных фрез могут за один проход формировать идеальные крупные сферические поверхности высокого качества, не нуждающиеся в дальнейшей доработке.
Результат совместной работы Leuco и фирмы Fischer - концевая фреза с резцами из поликристаллического алмаза для фрезерования за один проход паза для установки систем крепежа вентиляционных или фасадных деталей.
Еще одна новация - патроны для сверл диаметром 1 мм для производства шумопоглощающих панелей. Особенно важна стабильность работы этого ультратонкого инструмента для сверления большого числа отверстий.
Система инструментального учета и контроля позволяет из офиса отслеживать состояние и наработку инструмента, число сделанных заточек, оперативный ресурс и режимы эксплуатации, позиционирование на станке, своевременность обслуживания. Специальное приложение поможет клиенту оперативно получать наиболее эффективную техническую поддержку, четко планировать сервис и число сменного инструмента, повысить безопасность работы, а также свести к минимуму риск ошибок из-за человеческого фактора. Несколько лет назад на фрезах Leuco начали устанавливать чипы для постоянного получения данных, с помощью специально разработанного программного обеспечения информация с этих чипов аккумулируется и анализируется. Кроме того, пилы и фрезы компании помечаются двухмерными QR-кодами, которые позволяют идентифицировать каждый инструмент. Коды объединяются в группы, информация с них направляется в облачные хранилища, откуда может быть в любой момент истребована пользователями.
Самый большой в мире пресс для производства многослойных древесных панелей CLT (перекрестно-клееной древесины) представила на выставке фирма Minda. В июле текущего года начата поставка пресса английской фирме, специализирующейся на производстве сборных домов.
Механизация, устройство нанесения клея и конструкция пресса рассчитаны для ежегодного производства 120 тыс. м3 CLT при работе в одну смену. Прилагаемое прессовое усилие составляет 0,6 H/мм2, что соответствует общей прессовой нагрузке 7200 т. Спрессованные элементы с продольным и поперечным направлением слоев подаются к обрабатывающим центрам с ЧПУ.
Можно изготовить элементы размером до 20x6 м. Такие нестандартные размеры были выбраны с целью создания разных модулей и конфигураций домов.
Кроме того, большой интерес посетителей (особенно тех, кто проживает за пределами Европы) вызвало решение фирмы Minda для производства дорожных плит (rig-mats или crane-mats), которое было реализовано в США. Плиты размером 2,4x6,0 м из трех- или пятислойной прессованной древесины CLT используются для транспортировки оборудования по бездорожью, например, на нефтеносных песках, болотистых местностях и т. д. По оценкам специалистов, годовая потребность в подобных настилах составляет около 5 млн шт. После использования они очищаются и могут применяться в строительстве еще несколько раз в зависимости от нагрузки.
На предприятии, которое находится вблизи г. Чикаго (США), на линии Minda изготавливают 480 шт. пятислойных дорожных настилов (1000 м3) за смену.
Компания Nestro Lufttechnik GmbH (Германия), известная своими разработками в сфере аспирации и фильтрации воздуха, взяла на себя обеспечение эффективного удаления древесной пыли, опилок и стружки от всего комплекса оборудования, работавшего на стенде концерна Homag.
В числе оборудования, использовавшегося для этой цели, была новая модель вакуумной системы аспирации NE 200; очистку воздуха она выполняет с минимальным расходом электроэнергии и низким уровнем шума (72 дБ). Компания Nestro в последнее время концентрирует свои усилия именно на обеспечении энергоэффективности и снижения уровня шума при использовании оборудования и с успехом решает эту задачу благодаря внедрению высокопроизводительных малошумных вентиляторов и схем частотного управления работой двигателей, применения особых шумопоглощающих материалов, а также оптимизации конструкции и дизайна установок. Максимальная производительность NE 200 - 3,350 м3/ч.
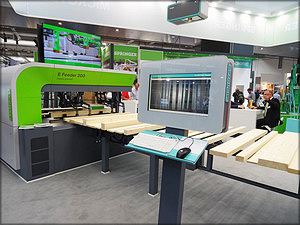
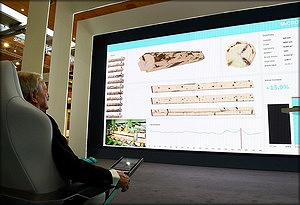
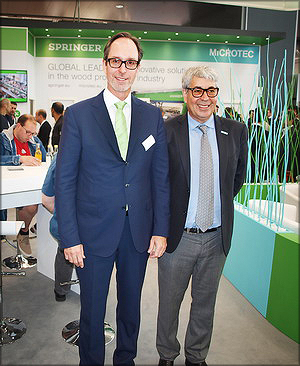
Глава Springer Maschinenfabrik AG Тимо Шпрингер и
директор компании Microtec д. т. н. Федерико
Джудичеандреа
Австрийская компания Springer Maschinenfabrik AG и итальянская Microtec выступили на Ligna 2017 в тесном сотрудничестве и заняв соседствующие стенды. Переходя от одного стенда к другому, можно было наглядно убедиться в том, как успешно сочетается в работе оборудование двух деловых партнеров.
- Мы показывали, как работает наша система контроля и мониторинга Trueye на подающем устройстве Springer E-Feeder, - рассказал руководитель отдела маркетинга и PR Microtec GmbH Симон Швайгкофлер, - она фактически задает синхронность работы устройства: специальная инфракрасная камера анализирует расстояние между поступающими досками и подает команду на изменение скорости подачи, оптимизируя работу линии, чтобы свести к минимуму холостой ход. 7,5х15 метров - такую максимальную площадь может измерять одна камера; если клиенту нужно, чтобы был больший охват, просто устанавливаются дополнительные камеры.
Интеграция этой системы в подающее устройство Springer E-Feeder позволяет оптимизировать процесс производства и повысить качество формирования слоев при накоплении на участке распределения, что обеспечивает повышение эффективности работы оборудования. Тем самым, по словам генерального директора Springer Maschinenfabrik GmbH Тимо Шпрингера, его фирма сделала еще один важный шаг в реализации принципов Industry 4.0.
К новинкам Springer следует отнести и RLS (Robotic Labeling System) - этикетировочную систему, обеспечивающую полностью автоматизированную маркировку пакетов и штабелей. Высокая гибкость и возможности адаптации промышленного робота позволяют совершенствовать производственный процесс при одновременном сокращении его продолжительности. Накопитель, рассчитанный на 8000 скрепок и 4500 самоклеящихся этикеток, обеспечивает непрерывную работу оборудования в течение длительного времени - от нескольких дней до недели.
Microtec представила на выставке в Ганновере несколько мировых премьер. В их числе: лесопильная линия со сканером CT Log (интерактивный симулятор, с помощью которого гости могли оказаться «внутри» не только сканирующего устройства, но и сканируемой им заготовки или детали, задать исходные данные собственного производства и получить расчет возможного увеличения выхода готовой продукции), высокоскоростной сканер для обнаружения дефектов пиломатериалов GoldenEye 800, оснащенный тремя источниками рентгеновских лучей (работает на высокой скорости загрузки - до 1200 м/мин.), а также установка для «умной» подсветки Smart Mill: высокоэффективные LED-приборы в ней - это не просто «лампочки», но и средство контроля оптимального использования рабочего пространства, где складируются заготовки или готовые изделия. Стереоскопические камеры, установленные вместе с осветительным оборудованием, передают объемное изображение отслеживаемого пространства в систему по Wi-Fi, а система использует эту информацию для поддержания 100%-ного контроля и оптимизации рабочих процессов.
Компьютерный томограф CT Log гарантирует непрерывную, качественную и полную 3D-реконструкцию изображения бревна. Размеры и расположение внутренних дефектов древесины можно точно описать во всех трех измерениях. С учетом внутренних дефектов древесины CT Log может оценить бревно по его визуальным характеристикам, качеству и прочности, определив качество конечной продукции еще до того, как бревно будет распилено. Методы распиловки и раскряжевки постоянно оптимизируются исходя из требований высокого качества продукции, помогая организовать производство в соответствии с приоритетами реального времени. Конусно-лучевая компьютерная томография (Large Cone-Beam Computed Tomography) - самая передовая технология, разработанная инженерами Microtec для складов круглых лесоматериалов и лесопильных цехов. Высокая точность и скорость компьютерной томографии обеспечивается за счет использования вращающихся вокруг бревна датчиков рентгеновских лучей и инновационного алгоритма реконструкции бревна в цифровом формате. На основе данных круговой рентгеновской компьютерной томографии мощное программное обеспечение оптимизации распиловки Maxicut Pro сканирующего устройства CT Log определяет наиболее подходящую схему распиловки при самой высокой выработке с учетом качества и стоимости при продаже конечной продукции. Система оптимизации раскряжевки Interopt определяет способ поперечной распиловки с задействованием самых высококачественных схем раскряжевки на разных участках бревна. Система оптимизации сортировки Winlog управляет сортировкой бревен, организацией склада лесоматериалов и разделкой лесоматериалов на деловые сортименты.
- Надежность, скорость и точность оборудования и приборов являются ключом к высокой производительности лесопильных заводов и производств конструкционных пиломатериалов продукции. С помощью наших устройств мы стараемся убедить клиентов, что им нет необходимости искать компромисс между производительностью и качеством, - таково мнение генерального директора Microtec Федерико Джудичеандреа.
Помимо нового сканера GoldenEye 800, на стенде компании был представлен широкий спектр популярных устройств этой серии Microtec, в числе которых демонстрировались: мультисенсорный сканер качества модульной конструкции с функцией цветоделения и лазерного и рентгеновского сканирования для точного выявления дефектов древесины GoldenEye 300, рентгеновский сканер-сортировщик прочности для определения модуля упругости и условного предела прочности при высокой скорости производства GoldenEye 700 и др.
В ходе выставки был заключен контракт с французской компанией Piveteau Scierie на поставку установки Microtec CT Log. На заводе французской компании в Сент-Флоранс уже эксплуатируется оборудование Microtec - например, мультисенсорный сканер оценки качества пиломатериала GoldenEye 500.
- Мы гордимся тем, что Piveteau в очередной раз выбрала нашу установку, - говорит Федерико Джудичеандреа. - Для нас это прежде всего означает, что покупатель доволен сотрудничеством, а это самая высокая из возможных оценок нашей работы.
В рамках выставки немецкая компания Simon Möhringer Anlagenbau GmbH («Мёрингер») анонсировала уникальную разработку, которая будет интересна всем деревообработчикам, вынужденным организовывать работу склада готовой продукции самостоятельно. «Автономная Транспортная Система Мёрингер» (M.A.T.S.) позволяет перевести работу склада в полностью автоматический режим: модуль с разными подъемными устройствами (например, вилочный подъемник, роликовый стол, поворотный стол и т. д.) не знает усталости, перемещается по оптимальной траектории и действует по строго заданной программе круглые сутки без участия человека.
Погрузка древесного сырья, деталей или готовых изделий на многоярусные стеллажи или формирование штабелей разной высоты, а также выгрузка выполняются четко и безопасно. Модуль компактен и мобилен: может перемещаться вперед/назад, влево/вправо, по диагонали, разворачиваться на месте и т. д., один модуль может переносить груз весом до 5 т. Если необходимо обеспечить большую грузоподъемность, несколько модулей могут работать синхронно, что особенно важно для работы с габаритными изделиями (такими как, например, конструкционные балки). Однажды задав траекторию и точки погрузки/выгрузки, можно повторять операцию в любое время одним нажатием кнопки на пульте управления.
Каждый модуль оснащен датчиками безопасности, которые учитывают препятствия, возникающие на пути передвижения модуля. Если требуется изменить траекторию, это можно сделать в ручном режиме.
В 2017 году компания Polytechnik Biomass Energy отметила на Ligna круглую дату - уже 30 лет этот австрийский производитель энергетических установок, работающих на биотопливе, является постоянным участником одной из самых авторитетных в лесопромышленном секторе выставок, площадка которой позволяет не только установить новые деловые контакты и поприветствовать клиентов и коллег, но и дает возможность продемонстрировать свои передовые разработки и технологические достижения. В этом году новинка от Polytechnik - запатентованное оборудование для производства древесного угля. Установки по изготовлению биоугля разработаны таким образом, чтобы производить продукты с высоким содержанием углерода и низким содержанием смолистых загрязнений. Пиролиз (превращения биомассы под воздействием высокой температуры и воздуха) протекает в реторте периодического действия. Дымовые газы и загрязняющие вещества, полученные в процессе карбонизации, сжигаются в замкнутом контуре, а избыточная энергия может быть использована для производства тепловой или электрической энергии, что позволяет соблюдать при коксовании требования экологических нормативов, а также достигать высокого КПД используемого сырья. Весь производственный процесс - от подачи сырья до получения готовой продукции - в значительной степени автоматизирован. Из древесины производят уголь высокого качества для нужд промышленных предприятий, биоуголь для повышения качества почвы, кроме того, он реализуется для нужд индивидуальных потребителей.
По словам исполнительного директора по работе со странами Восточной Европы компании Polytechnik Марии Королевой, несмотря на то, что выпуск оборудования для производства древесного угля - новое направление для компании, перспективы у этого направления хорошие - интерес к выпуску древесного угля, в том числе и со стороны российских потребителей, довольно высок, что подтвердило общение с посетителями выставки.
Рост производственных издержек и дефицит высокосортной древесины привели к тому, что эффективность использования перерабатываемого сырья стала ключевым фактором в производстве фанеры и бруса из клееного шпона. Многие современные технологии предназначены для увеличения выхода продукции, повышения эффективности в отдельном секторе производства или на конкретной производственной линии, но наибольшей экономии можно добиться, оптимизировав технологические процессы и потоки материалов в масштабах всего производства. Комплексное технологическое решение SmartMill, разработанное корпорацией Raute, позволяет кардинально усовершенствовать технологический процесс и повысить общую эффективность производства - начиная с биржи сырья и заканчивая выпуском готовой фанеры и клееного бруса - при помощи «умных» анализаторов и цифровой информационной системы. Применяя SmartMill, можно повысить коэффициент использования сырья на 15%.
Линейка инновационных анализаторов нового поколения G5 была разработана подразделением Mecano, входящим в состав корпорации Raute. Эти приборы оценивают качество изготавливаемого шпона и спустя миллисекунды принимают решения по оптимизации режимов его обработки. Платформа G5 позволяет анализаторам обмениваться данными по качеству. Сканеры, установленные в начале линии, виртуально симулируют наиболее подходящий способ продолжения технологического процесса, принимая решения о ребросклейке или ремонте того или иного полотна шпона. Если по расчетам сканера подобные действия не оправданы, шпон изымается из технологического процесса еще на этапе лущения и далее перерабатывается в топливо или древесную массу. Подобная симуляция на раннем этапе позволяет экономить сырье, повысить пропускную способность линий сушки, починки и ребросклейки, на которые будет подаваться только деловой шпон. Система G5 Mecano на самом раннем этапе распределяет наиболее качественный шпон по нужным секторам производства, минимизирует число операций, оптимизирует условия хранения, снижает риск неоправданных потерь. Преимущество комплексного технологического процесса заключается в разумной оптимизации потока материала в масштабах всего производства, в результате чего экономятся значительные средства.
Теперь каждый блок G5, снабженный модернизированной высокоточной системой машинного зрения и определения влажности шпона, удобным в использовании интерфейсом, сенсорным монитором и другими новшествами, обеспечивает повышение коэффициента выхода продукции и эксплуатационную готовность каждой линии. Систему G5 можно устанавливать как на новых линиях и станках, так и в рамках модернизации систем машинного зрения и определения влажности шпона на эксплуатируемом оборудовании. Переход на технологию G5 может выполняться постепенно - от узла к узлу, от линии к линии, или же одновременно на всем производстве.
Революция «умных» технологий коснулась и сферы сервиса: в дополнение к услугам по модернизации, техническому обслуживанию и поставке запчастей теперь Raute предлагает клиентам также и «цифровые» услуги - такие как сбор данных в режиме реального времени, осуществление контроля оборудования в удаленном режиме, обучение сотрудников по сети и предоставление круглосуточной линии технической поддержки. Таким образом, клиенты Raute получают самые современные инструменты поддержания работоспособности своего оборудования на высоком уровне.
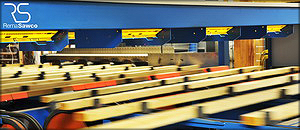
Компания RemaSawco представила вниманию посетителей свою новую разработку - BoardScannerQ, систему сканирования сухих досок для определения их качества с автоматическим определением прочностных характеристик пиломатериала (RS-StrengthGrader), а также передовую систему BoardScannerP с такими же техническими возможностями, как у системы для сухих досок, но специально разработанную для линий сырой сортировки пиломатериалов.
Система RS-StrengthGrader позволяет определить прочностные характеристики пиломатериала путем бесконтактных измерений расположения (ракурса) древесного волокна хвойных пород древесины. Она подключена к системе RS-BoardScannerQ и полностью интегрируется с программным обеспечением. Таким образом, заказчику не потребуется приобретать дополнительное оборудование для определения качества досок, что позволит сократить его финансовые затраты. Кроме того, система может определять и плотность пиломатериалов.
Большой интерес у гостей стенда вызвала и демонстрация новой концепции AIT, суть которой - интеграция всех предлагаемых компанией RemaSawco систем в одной базе данных. Благодаря этому решению в режиме реального времени можно осуществлять контроль и оптимизацию процесса переработки пиловочника на лесопильном предприятии, начиная с сортировки бревен и заканчивая выпуском готовой продукции.
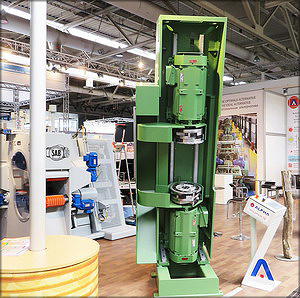
Станкостроительная компания SAB Sägewerksanlagen GmbH (г. Бад-Берлебург-Ауэ, Германия) представила технологические модули современного фрезерно-брусующего, круглопильного и профилирующего оборудования. В их числе есть новые решения, которые могут быть интересны малым и средним предприятиям российского ЛПК: это разработки для полностью автоматической распиловки несортированного пиловочника. Следует особо отметить RBZ-10, которая в настоящее время находится в производстве. По словам представителя компании SAB, несмотря на спад продаж в России, фирма не снижает активности на российском рынке, отмечая постепенное ослабление политической и экономической напряженности, за которыми неизбежно последует и высокий интерес со стороны российского клиента. А пока некоторое сокращение числа заказов со стороны российских клиентов компания компенсирует поставками в другие страны Европы. Так, недавно на одном из европейских предприятий была введена в эксплуатацию большая профилирующая установка, оснащенная механизмом штабелирования пиломатериала сразу после распиловки и пропиточными станциями проходного типа.
SCM Group привезла в Ганновер более 60 станков, на огромном стенде площадью 4000 м2 представив все виды выпускаемого оборудования, обеспечивающего потребности производителей любого типа - от мелких ремесленных мастерских до крупных международных компаний. Впервые было принято решение разместить все оборудование в едином выставочном пространстве, чтобы подчеркнуть технологическую мощь концерна. Центральную часть экспозиции, получившую название SCM Arena и предназначенную для делового общения, занимала мультимедийная система с двумя гигантскими видеопанелями (6x3,4 м) для виртуального знакомства со станками и технологиями. Благодаря этой системе посетители могли «проникнуть внутрь» технологических узлов и агрегатов.
В числе инноваций прежде всего следует отметить систему производственных ячеек Lean Cell 4.0, воплотившую в реальность принципы «Индустрии 4.0» и отвечающую потребностям компаний, занимающихся промышленным производством изделий индивидуального исполнения. Она полностью автоматизирована и может производить до 10 мебельных гарнитуров в смену. Весь процесс производства - от обработки полноформатной плиты до выпуска готовой детали - полностью контролируется программой-супервайзером. Система гарантирует высокое качество и низкую себестоимость продукции и может управляться одним, даже малоопытным оператором, что способствует низкой себестоимости производства. С помощью этой системы можно выпускать широкий ассортимент продукции - от стандартизованных мебельных панелей до штучных изделий.
Система производственных ячеек построена на базе автоматизированного склада полноформатных плит Flexstore EL. По электронным каналам связи на склад поступают заказы, автоматически, без задержек на перенастройку, запускается процесс производства. Склад Flextore EL обслуживает две работающие параллельно машины: пакетный раскрой крупных партий щитовых деталей ведется на пильном центре SCM Gabbiani P75, а для изготовления малых партий и наиболее сложных деталей используется нестинговый обрабатывающий центр с ЧПУ SCM Morbidelli N100. На линии установлен антропоморфный робот, который с помощью телекамеры распознает раскроенные заготовки и переносит их на кромкооблицовочный станок SCM Stefani Solution XD с устройством автоматического возврата Mahros, где они проходят облицовку с безупречным качеством поверхностей. После выхода из кромкооблицовочного станка деталь передается роботом в присадочный станок SCM Morbidelli CX100, где выполняются финишные операции. Готовые детали выводятся по рольгангам в зону отгрузки заказов.
Программная система-супервайзер Maestro Watch отслеживает весь процесс производства, начиная с запуска заказа в работу, и распределяет управляющие программы между станками. Это простое и функциональное решение позволяет точно рассчитывать производственные потоки и сроки выполнения заказов, гарантируя быструю и уверенную окупаемость. 25 книжных шкафов, изготовленных на Lean Cell 4.0 в дни выставки, отправлены в реставрируемые школы населенных пунктов Центральной Италии, пострадавших от землетрясений лета и осени 2016 года.
Впервые были продемонстрированы новые обрабатывающие центры для плитных материалов Morbidelli Author M100 и M200, построенные по принципу «всё в одном». В числе особенностей станков - гибкая конструкция рабочего стола (все траверсы можно сдвинуть влево или вправо + ассиметричная работа в режиме «маятник»), сверхбыстрая смена инструментов (всего 12 с) и магазин на 14 позиций, установленный на подвижной балке. Целый ряд изменений затронул семейство универсальных обрабатывающих центров для присадки, фрезерования и кромкооблицовки: станок для мебельных предприятий Morbidelli Planet P800, позволяющий выполнять операции присадки, фрезерования и облицовки кромок, а также обрабатывающий центр с ЧПУ Morbidelli СX100, отличающийся малыми габаритами и возможностью пильного раскроя и фрезерования.
Среди новаций оборудования для сегмента кромкооблицовки - производственная ячейка Stefani Easy Order SZ, построенная на базе одностороннего кромкооблицовочного станка, управляемого одним оператором. Система отличается невысокой стоимостью и обеспечивает возможность работы в режиме штучной облицовки для предварительно отформатированных заготовок. На выставке было также представлено новое решение для производства фасадов с J-образными профилями-ручками Stefani Solution J-Shape - уникальная технология, отмеченная в 2016 году призом Xia (Xylexpo Innovation Award) в категории «Обработка плитных материалов».
На Ligna дебютировала новая линейка станков Stefani с цифровыми приводами регулировки рабочих агрегатов и возможностью установки двух устройств предварительного плавления клеев - ЭВА и полиуретанового. Модели линейки Olimpic получили обновленный дизайн благодаря проведенному недавно рестайлингу. На этих станках, в арсенале которых имеются цифровые оси настройки, можно выпускать продукцию с двумя разными радиусами кромки.
Одной из важнейших новаций в области оборудования для раскроя стало обновление операторского интерфейса. Новые станки, выпускаемые концерном, будут комплектоваться 21-дюймовым дисплеем с функцией multi-touch, которая призвана повысить эффективность действий оператора. Программное обеспечение предоставит полную свободу обмена данными с внешними системами в полном соответствии с принципами «Индустрии 4.0». Два бюджетных пильных центра - SCM Gabbiani P и SCM Gabbiani ST с загрузочным столом теперь оснащены веб-камерами, что позволяет наблюдать за всеми рабочими операциями дистанционно - из центра технической поддержки. Предусмотрена и функция сканирования штрихкода, которым снабжаются сырьевые материалы, что позволяет упростить ведение склада остатков и сократить объемы отходов при раскрое.
Среди станков для калибрования и шлифования под маркой DMC были представлены новый станок промышленного класса Eurosystem модульной конструкции, а также линейка из трех шлифовальных станков System. Эти модели могут применяться как для калибрования и шлифования, так и для структурирования поверхностей с созданием специальных эффектов отделки вроде имитации обработки стамеской или ленточной пилой.
Главной новинкой в сегменте оборудования для обработки массива древесины стал пятикоординатный обрабатывающий центр с ЧПУ SCM Accord 25 FX, оснащенный новым рабочим агрегатом с сопровождающим инструментальным магазином и двумя независимыми осями Z. Он может использоваться на многих инновационных направлениях, обеспечивая полную свободу операций при обработке элементов с высотой до 500 мм.
Сектору деревянного домостроения SCM предложил обрабатывающий центр с шестью рабочими осями Routech Oikos, предназначенный для изготовления конструкционного бруса и модульных стеновых элементов. Занимая в цехе довольно небольшую площадь, Oikos может выполнять самые сложные задачи с высокой скоростью и безукоризненной точностью, характерной для обрабатывающих центров с ЧПУ.
Еще одна секция выставочной экспозиции SCM была посвящена высокотехнологичному оборудованию CMS - под этой маркой были представлены три обрабатывающих центра специального назначения. Atom - пятикоординатный обрабатывающий центр с подвижным порталом для производства любых столярных изделий; Monofast - эксклюзивное решение для автоматизированного производства сложных изделий, таких как ружейные приклады, накладки рукояток пистолетов и другие элементы малых размеров; Turbopower - представитель инновационной линейки портальных обрабатывающих центров, отличающихся большой гибкостью при решении многочисленных и постоянно усложняющихся задач деревообработки, в частности, при производстве элементов интерьера, лестниц и музыкальных инструментов.
Отдельная зона на выставочной площадке была выделена для станов, предназначенных для малых и средних предприятий, среди которых нашлось место нескольким новинкам: форматно-раскроечного станка с двухсторонним наклоном пилы - Minimax Si 400 X и ставшего премьерой выставки высокоскоростного кромочника Minimax ME40, комплектуемого полным набором узлов чистовой обработки.
Хорошо известная российским деревообработчикам компания Secal S.R.L. (Италия) представила новый софт для сушки древесины EPL Supervisor 8. Это программное обеспечение использует язык программирования последнего поколения и предназначено для Windows 10. Новый софт EPL Supervisor 8 дает возможность использования волоконно-оптической связи, что обеспечивает быструю и безопасную передачу данных.
Сетевой интерфейс позволяет подключать контроллеры сушильных камер через безпроводную сеть. Новая графика софта EPL Supervisor 8 обеспечивает детальный контроль работы всех элементов сушильных камер в реальном времени. ПО EPL Supervisor 8 снабжено такими новыми функциями, как «Воздушный динамический поток» (Air Dynamic Flow System), которая позволяет оператору сушильных камер создавать периодические циклы вентиляции по его усмотрению; «Полуавтомат» для системы нагрева и воздухообмена; «Ассистент графического программирования» и другие.
Новая быстрая графическая система анализа данных процесса сушки позволяет управлять графиками с огромным объемом информации на скорости, которая ранее была невозможна.
Два интерфейса, встроенные в электрический щит сушильных камер, гарантируют защиту режимов работы камер от нестабильной подачи электроэнергии.
Компания Serra Maschinenbau GmbH (Германия) привезла на выставку ленточнопильные станки первого ряда, а также оборудование второго ряда производительностью 100-150 м3 досок за смену: новый многопильный станок с циркулярными пилами CS 600 и многоголовочный делительный станок на базе ленточных пил для изготовления сортиментной доски MK402.
Корпус CS 600 изготавливается из двух стальных листов толщиной 15 мм, цепные приводы и клиновые ремни, оснащенные защитными кожухами, находятся вне их. Система подачи заготовки разделена на два независимых блока. Регулировка скорости подачи осуществляется с помощью преобразователя частоты. Конструкция пильного узла обеспечивает легкую смену инструмента. Отсутствие вибраций на упрочненном пильном валу гарантировано его двухопорной системой крепления в корпусе станка. Станок может комплектоваться двигателями мощностью от 22 до 90 кВт. Компактная конструкция CS 600 позволяет существенно сократить время пусконаладочных работ. Станок поставляется полностью готовым к работе, пользователю нужно только определиться с местом его установки и подключить электроэнергию.
Новая версия ленточнопильного станка Alpina KE90 с лентой шириной 80 мм предназначена для распиловки бревен диаметром до 90 см и изготавливается с учетом индивидуальных требований клиента.
Вниманию посетителей и специалистов были предложены новые системы управления станками ProComfort Plus, которые позволяют оптимизировать работу станка. Большой монитор (21,5 дюйма Full HD), сенсорная клавиатура, два многофункциональных джойстика со свободно программируемыми функциями и т. д., обеспечивают комфортную работу оператора.
На стенде была представлена и новинка в сфере мобильного лесопиления - тяжелый ленточнопильный станок XT135, который предназначен для распиловки бревен диаметром до 1,35 м.
Новые прессы ContiRoll Generation 9 и ContiRoll Generation 9 NEO обеспечили стенду машиностроительной компании G. Siempelkamp GmbH & Co. KG (Германия) пристальное и почти ажиотажное внимание как потенциальных клиентов, так и многочисленных журналистов. Для некоторых представителей отраслевой прессы руководство компании устроило эксклюзивную мини-конференцию. Полученную на ней информацию мы и публикуем в этом отчете.
Премьерная презентация ContiRoll Generation 9 и Generation 9 NEO стала кульминацией выставочной программы Siempelkamp на Ligna 2017. Пресс непрерывного действия ContiRoll успел стать эталоном оборудования для производства древесных плит, а благодаря инновационным разработкам (таким как измененная входная зона пресса, самые современные приводная и измерительная техника, техника моделирования и управления процессом, новые методы предварительного нагрева ковра и новые технологии, используемые на линии конечной обработки), примененным в технике нового поколения, уместно говорить о достижении принципиально нового уровня в развитии прессового оборудования для плитного производства.
Особенно впечатляет в ContiRoll Generation 9 NEO удлиненная входная зона. 14 рам пресса обеспечивают статическую стабильность. Удлиненная на 100% по сравнению с конструкцией прессов предыдущего поколения входная зона нагревательной плиты с тепловым ударом вместе с гидравликой пресса обеспечивают производительность, которая выше на 30% по сравнению с предыдущим поколением оборудования.
- Повышение производительности пресса - это самый убедительный аргумент для тех, кто намерен приобрести его, - отметил спикер правления Siempelkamp Юрген Филиппс. - Добавьте к этому бесперебойность работы оборудования, минимизирование расходов на технический уход, высокоточный мониторинг состояния узлов и агрегатов, а также высокое качество продукта при возможности экономить материал и энергию, и вы поймете, в чем отличия прессов девятого поколения.
В числе особенностей ContiRoll Generation 9 Ecodrive - гибкая загрузка, новый прессовый контроллер, высоконадежная цепь питания, модернизированная гидравлическая система, операционная скорость до 2500 мм/с, новый компактор для высокоскоростного производства тонких плит.
- Когда вы задумаетесь о новом, десятом поколении прессов ContiRoll? - отчасти в шутку, отчасти всерьез спросили мы г-на Филиппса.
- Не так уж и много времени прошло с момента разработки и производства оборудования восьмого поколения, а на сегодня уже установлено 30 этих линий, - вполне серьезно ответил спикер правления Siempelkamp. И тоже пошутил: - Вот поставим заводов 15 с прессом девятого поколения, вот тогда, через несколько лет и вернемся к этому разговору!
Помимо презентации нового поколения прессов акцент в экспозиции Siempelkamp был сделан на измерительной системе EcoScan, EcoPulser (почти неизнашивающемся устройстве для дополнительного измельчения щепы и стружечного материала), диагональной пиле для плитного производства, новой системе клеенанесения для линий по производству ДСП, а также SicoCam - инновационной измерительной системе для плит, полностью интегрированной в технологическую цепочку (автоматизированная и управляемая с помощью компьютера система высокоточных камер позволяет без участия человека оперативно отслеживать любые несоответствия габаритов сделанных плит заданным и передавать корректирующие команды на пильный центр).
На выставке также был показан разработанный Siempelkamp совместно с компанией Ventapp сепаратор для волокна EcoSifter, применяемый в производстве плит MDF; он характеризуется повышенной пропускной способностью и отличается от других моделей более высокой энергоэффективностью.
Отдельно следует сказать о новом приложении Siempelkamp Service to Go, которое позволяет клиенту решать все производственные вопросы онлайн со смартфона или планшета, обозначать поставщику возникшие проблемы, получать консультации в реальном времени, отслеживать поставки запчастей и т. д.
На пресс-конференции руководства Siempelkamp были обнародованы некоторые экономические выкладки. Так, мы узнали, что в 2016 году машиностроительное отделение группы компаний увеличило число полученных заказов почти на 8% по сравнению с 2015 годом. Объем общего портфеля заказов составил 500,8 млн евро, а оборот - 593,7 млн евро.
На выставке Ligna 2017 компания Siempelkamp подписала три контракта на поставку оборудования для производства древесных плит общей стоимостью около 100 млн евро, а также несколько договоров по сервисному обслуживанию.
Укрепляется положение концерна в Азиатском регионе - на сегодня там установлено уже более 100 прессовых линий. Деятельность компании в Азии не ограничивается поставками оборудования: Siempelkamp сделал более 12 млн евро инвестиций в полностью укомплектованные заводы (в г. Циндао и г. Вуши, Китай) и инжиниринговые службы (в Индии и Малайзии). Китайские заводы (100% собственность компании) осуществляют производство и сборку элементов технологических линий в соответствии с самыми высокими стандартами качества.
Что касается России, директорат Siempelkamp предпочел пока обойтись без подробностей, однако журналистам сказано, что очень большой проект по оснащению предприятия «АлтайЛес» компания ведет как генеральный поставщик.
Еще одна новость, о которой нельзя не упомянуть: с апреля 2017 года в состав концерна вошла существующая на рынке с 1903 года компания Pallmann, продукция которой очень помогает Siempelkamp проводить оснащение плитных предприятий. В Ганновере концерн Siempelkamp представил компетенции всей группы компаний, включая дочерние: SLS (Siempelkamp Logistics & Service: существует с 2010 года, обеспечивает все услуги и сервис, включая логистику, доставку, запчасти, пусконаладку, остановку линий и пр.), Sicoplan (проектный институт, Бельгия), CMC Texpan (эксперт по подготовке сырья, Италия) и Pallmann (эксперт по технике измельчения древесины).
Теперь, благодаря консолидации усилий компаний всей группы, Siempelkamp осуществляет полный цикл работ и услуг, начиная с консультаций, концепта, финансовых расчетов проекта и заканчивая его техническим воплощением и последующим обслуживанием оборудования.
Новое поколение шлифовальных лент TSQ для обеспечения наилучшего качества поверхности продемонстрировала в Ганновере швейцарская фирма Steinemann Technology AG. Создание этого продукта стало результатом творческого поиска команды сервисных специалистов, исследований по оптимизации технологий шлифования поверхностей ДСП, фанеры и плит MDF, большого опыта и глубокого знания конструкции шлифовальных станков специалистами компании и ноу-хау фирмы Steinemann в сфере изготовления материалов для шлифования.
Повышенные плотность насыпки, уровень связующего покровного слоя, адгезия зерна, качество соединения ленты и использование новой полиэфирной ткани обеспечивают превосходное качество поверхности изделий, обрабатываемых на широколенточных шлифовальных станках фирмы Steinemann.
Сотрудники компании Terex Deutschland GmbH на выставке представили две модели новой серии F, a именно - перегружатель MHL350F с подъемной кабиной (применяется для разгрузки и погрузки железнодорожного и автотранспорта, складирования лесоматериалов в штабель и др.), а также новую модель специальной серии лесных перегружателей Pick & Carry MHL334F. Перегружатели серии Pick & Carry одновременно выполняют сразу три операции: разгрузку древесины, ее транспортировку и погрузку или штабелирование.
Но бесспорным «чемпионом» посетительского интереса на протяжении всей выставки была новая кабина Fuchs (в этом году она была удостоена премии международного конкурса промышленного дизайна iF design awards) - Fox Cab с изображением лисы на борту. Впрочем, задачей разработчиков было не достижение привлекательного внешнего вида, но - в первую очередь - обеспечение оптимальной эргономики, функциональности и комфорта при работе.
Кабина, специально разработанная для погрузочной техники, обеспечивает максимальное удобство работы оператора, все основные элементы управления находятся в пределах досягаемости с сиденья. Лобовое тонированное стекло с наклоном вниз предоставляет возможность отличного обзора при погрузочно-разгрузочных работах, прекрасно защищает от воздействия интенсивного солнечного света и способствует снижению температуры воздуха в салоне; специальный навес защищает от атмосферных осадков, а особая конструкция раздвижной двери обеспечивает работнику удобный и безопасный доступ в кабину.
Главный менеджер отдела НИОКР компании Üstunkarli Makine A.Ş. (г. Измир, Турция), инженер Коральп Арслан, рассказал о том, с чем турецкая компания приехала в Ганновер: «Выставка прошла для нас успешно: состоялся ряд встреч с партнерами, постоянными и новыми клиентами, с которыми были обговорены некоторые проекты и заключены соглашения. Организация проведения выставки в целом, как и всегда, на высшем уровне, мы очень довольны».
Компания Üstunkarli производит станки для лесопиления и деревообработки с 1954 года. В результате интенсивных научно-исследовательских и опытно-конструкторских работ в 2016 году фирма предложила рынку новую линейку продуктов из серии UHYB - экономичное решение для клиентов, которые хотят начинать бизнес с минимальными финансовыми вложениями.
Горизонтальная ленточная пилорама от Üstunkarli не требует детальной подготовки фундамента, что обычно необходимо при установке стандартных пилорам. Широкий спектр опций позволяет предлагать клиентам наиболее экономичные решения в соответствии с их потребностями. Три системы для обработки круглого леса из серии UHYB уже нашли своих владельцев и введены в эксплуатацию на объектах заказчиков.
В 2017 году компания представила на рынке каретки-бревнотаски серии UTA новой конструкции. Число компонентов в них сокращено, что исключает риск сбоев и потери точности в течение жизненного цикла каретки, а также повышается эффективность использования сырья.
Конструкторы Üstunkarli разработали комплексный проект под ключ для производства поддонов: в комплект линии входят: наклонная ленточная пилорама и наклонная каретка, кантер/фрезерный блок, кромкообрезной станок с оптимизацией позиционирования дисковых пил, фрезерная установка для кромкообрезного станка, многопильный торцовочный станок, многопильный станок, вспомогательное погрузочно-разгрузочное оборудование и аспирационная система. Основными задачами проекта были повышение производительности, эффективности и качества производства, сокращение числа обслуживающего персонала и оптимизация работы кромкообрезного станка в зависимости от ширины конечной продукции на выходе многопильного станка без вмешательства оператора. В основе этой линии - кромкообрезная система, которая состоит из выравнивающего доску конвейера, фрезерной установки для кромкообрезного станка, кромкообрезного станка и конвейера рейкоотделителя. Было разработано программное обеспечение для последовательного управления кромкообрезной системой, которая оснащена 10 гидравлическими цилиндрами, приводимыми в действие отдельными пропорциональными клапанами. Оператор позиционирует доску в соответствии с неподвижной пилой на кромкообрезном станке и отмечает линии на доске лазером, после чего отправляет ее на станок. Головка фрезерной установки и пилы кромкообрезного станка позиционируются автоматически. Кромкообрезная система измеряет высоту доски, расположение верхних прижимных роликов регулируется автоматически.
Вниманию гостей стенда компании Valutec (Швеция - Финляндия) было предложено несколько новинок. Наибольший интерес вызвали очки виртуальной реальности, с помощью которых можно было совершить тур по сушильной камере непрерывного действия типа TC, понять, как она устроена, и принцип ее работы.
Еще одним значимым экспонатом на стенде Valutec стала Valmatics - система управления, которая также включает в себя симулятор (Valusim). «Использование этой системы позволяет сократить продолжительность сушки и эксплуатационные расходы без снижения качества продукции», - сказал специалист по маркетингу компании Valutec Эрик Йоханссон.
Эксперты компании также рассказали об открытии нового направления работы концерна в России - продаже запасных частей и оказании услуг по модернизации сушильных камер. За это направление будет отвечать Артем Веретенников. Теперь клиенты компании имеют возможность приобретать комплектующие для сушильных камер со склада в Санкт-Петербурге и получать техническую помощь от российских специалистов Valutec. Сформирован оперативный склад наиболее востребованных запасных частей и материалов для сушильных камер, что позволит существенно сократить сроки их поставок клиентам. Специалисты компании полагают, что благодаря новой схеме работы также появится возможность снизить стоимость запчастей, что очень важно для покупателей.
По мнению Эрика Йоханссона, сервисное обслуживание клиентов, в том числе поставка комплектующих и запасных частей - важнейший фактор успешного развития Valutec. Компания видит свою задачу в максимальном упрощении процесса послепродажного обслуживания и коммуникации с заказчиками, в том числе в России.
Немецкая компания Vecoplan AG представила на двух своих стендах разнообразные новинки оборудования для измельчения, транспортировки и переработки отходов деревообработки и вторичного сырья. В их числе - одновальные измельчительные установки серии VAZ, предназначенные для лесопильных предприятий, производителей фанеры, ДСП, ДВП и других подобных материалов. Одновальные шредеры универсальны, предназначены для переработки разных материалов и могут использоваться без дополнительных загрузочных систем. Толкатель с гидравлическим приводом быстро подает утилизируемую массу к измельчающему механизму. Благодаря медленному вращению ротора и вертикальной загрузке измельчение выполняется почти бесшумно и без пыли. Компанией разработаны как компактные, так и крупные производительные измельчители: например, производительность VAZ 1100 XL с ротором 370 мм - 1075 кг/ч.
Помимо прототипов установок VAZ, гостей экспозиции интересовала барабанная рубильная машина VTH 45/10/2U. Измельчение древесины в этой стационарной установке с горизонтально расположенным узлом подачи осуществляется при помощи быстро вращающегося ротора, оснащенного рубильными ножами. Машина отличается высокой производительностью и вместе с тем экономичностью, она может использоваться, например, для производства энергетической щепы или щепы технологической - для целлюлозной промышленности.
Внимание посетителей выставки привлек также измельчитель биомассы VTH 105/60/4B с подающим транспортером. Он предназначен для переработки энергетической щепы, используемой в качестве топлива на электростанциях, работающих на биомассе.
Экспозиция Venjakob Maschinenbau GmbH & Co. KG (г. Реда-Виденбрюк, Германия) была выдержана в стилистике дизайна знаменитых на весь мир автогонок Le Mans (24 Heures du Mans) и состояла из трех машин для окраски деталей распылением Ven Spray (серий Perfect Comfort и Smart), а также роботов Vario. Посыл был вполне понятен: девиз «Быстрее к финишу!» отлично подходит как к движению скоростных авто, так и к операции финишной обработки поверхностей. Отличный маркетинговый ход!
Автоматические покрасочные линии Venjakob предназначены для применения в разных сегментах рынка, начиная с начального уровня и заканчивая мощным промышленным производством. Применение самых современных технологий позволяет заказчикам организовывать свои рабочие процессы безупречно и логично, в то же время повышая степень автоматизации производства. Интегрированная сетевая технология обеспечивает связь между отдельными компонентами установки и предоставляет широкий спектр возможностей для анализа процессов, генерируемых системой. Контроль процессов основан на мониторинге расхода материала в покрасочной распылительной установке и на контроле правильности процесса распыления. Данные, поступающие в базу, позволяют делать оценку эффективности работы и прогнозировать необходимость обслуживания оборудования.
Посетители выставки могли оценить удобство эксплуатации машин в действии, работа оборудования была продемонстрирована на стенде в мельчайших деталях.
Главная новинка из представленных немецкой компанией Vollmer - автоматический центр по производству дисковых пил с твердосплавными напайками Vollmer CC 355. Особенность этой модели в том, что она обеспечивает значительно более короткий, по сравнению с предыдущими моделями, процесс обработки заготовок за счет коротких перемещений - за один цикл станок выполняет заточку передней, задней и боковых граней резцов пилы. Эта высокоскоростная машина идеально подходит для серийного производства пил стандартного исполнения. Пила проходит цикл заточки и перемещается с помощью четырех манипуляторов от загрузочного отсека и между агрегатами обработки внутри станка. Диаметр обрабатываемых пил - от 150 до 355 мм.
Также компания продемонстрировала в Ганновере станок Vollmer CP 650 для заточки дисковых пил с широким диапазоном обработки пил диаметром от 80 до 650 мм - подобное оборудование отлично подойдет для машинного парка сервисного центра или мебельного предприятия.
В сегменте концевого инструмента Vollmer представила оборудование для эрозионной обработки инструмента QXD 250 с роботизированной системой загрузки, а также достаточно новый станок для производства полностью твердосплавного концевого инструмента - VGrind 360, эта модель уже успела хорошо зарекомендовать себя на заводах ведущих мировых производителей концевого инструмента и активно используется уже и в России.
Компания Weima Maschinenbau GmbH (Баден-Вюртемберг, Германия) представила вниманию посетителей и участников выставки в Ганновере новый компактный шредер WL 600 для малых и средних производств, на котором можно перерабатывать любые виды древесных отходов - обрезки плит MDF и ДСП, пиломатериалов из массива древесины (в том числе самых твердых пород). Надежный и недорогой одномоторный измельчитель с проверенными технологиями - что еще нужно потребителю? Новая разработка WL 600 - модель начального уровня, но это вовсе не исключает высоких эксплуатационных характеристик: выходная мощность - 15-18,5 кВт, рабочая ширина - 600 мм, ротор диаметром 252 мм с 14 ножами и сменное сито с отверстиями 10-40 мм. Полученная древесная щепа идеально подходит для брикетирования или может быть использована в качестве древесного биотоплива.
Помимо новой машины Weima привезла на Ligna еще три измельчителя - WL 4, WLK 1000, WLH 300, а также брикетные прессы моделей TH 714 и TH 1500.
- Российский рынок, как и прежде, очень важен для нас, - сказал корреспонденту «ЛПИ» председатель правления Michael Weinig AG Вольфганг Пешль, - мы верим в него и считаем надежным. В последнее время он снова начал расти, мы видим, как это проявляется в продажах не только отдельных наших машин, но и системных решений.
Более 40 станков и линий на площади 4000 м2 и заказы на 47 млн евро. Вот что такое Weinig на Ligna 2017. Под традиционным девизом «Think Weinig» концерн впервые представил новую выставочную концепцию совместно с дочерней компанией Holz-Her, специализирующейся на оборудовании для обработки древесных материалов. Все пять дней выставки на стенде толпился народ - и слово «толпился» здесь не преувеличение, потому что порой к некоторым из станков было просто не подойти. Особенный интерес публики вызвал новый стандарт W4.0 digital, ставший ответом компании на вызовы сетевого производства: с его помощью Weinig, наряду с представлением комбинаций разного оборудования в виде единых линий, объединенных в сеть, продемонстрировал, как должны выглядеть решения для всей цепочки создания стоимости.
Что касается новинок оборудования (похоже, скоро, в наступающую эпоху сетевого производства, мы будем уточнять - «единичных станков»), стоит прежде всего отметить мировую премьеру Powermat 2400, самого современного строгально-калевочного станка в ставшей уже канонической линейке Powermat. «Революцией в профилировании» без ложной скромности назвал его директор по продажам компании Michael Weinig AG Грегор Бамбуш. Гибкая модульная система для строгания и профилирования рассчитана на промышленное производство брусков и планок со скоростью подачи до 100 м/мин. Новая функция позволяет изготавливать на станке детали с коническим и/или изогнутым контуром, а версия 3D - за один проход получать произвольно программируемые структурированные поверхности. Выделялся этот станок среди собратьев не только возможностями, но и экстерьером - впервые на нашей памяти станок Weinig был не зеленого цвета, а в раскраске, применяемой для маскировки автомобильных прототипов.
Как и в моделях Powermat 700 и Powermat 1500, здесь также последовательно реализована концепция управления Comfort Set: ручные регулировки, для которых не требуются инструменты, а также элементы с ЧПУ гарантируют быструю, удобную и надежную наладку.
На новом станке можно выполнять автоматические регулировки при закрытом кожухе, то есть в процессе работы: боковые прижимные ролики втяжного устройства с четырьмя валиками по команде ЧПУ могут автоматически позиционироваться с учетом ширины детали; боковые направляющие линейки после левого шпинделя также оснащены осями для автоматического позиционирования по ширине; джойнтеры синхронно перемещаются на всех шпинделях и следуют за шпинделем при его радиальной регулировке; гидравлическая контропора оснащена автоматическим зажимным устройством для радиального позиционирования шпинделя на работающем станке.
На выставке новый Powermat, интегрированный со средствами механизации для загрузки заготовок и выгрузки готовых изделий демонстрировался в действии на скорости подачи до 100 м/мин., производя шпунтовые доски, планки из плиты MDF, а также доски с шероховатой поверхностью для обшивки внахлест. Станок поступит на рынок до конца текущего года.
В области комплексной обработки оконных и мебельных деталей было представлено второе поколение интегрированных высокопроизводительных станков Conturex: модель 125 Vario обогатилась входной механизацией с параллельной подачей материала, четырьмя цанговыми столами Vario с двумя цанговыми креплениями на каждом, а также двумя интерполирующими 5-осевыми головками. Для демонстрации Conturex в работе он был соединен в сеть с Weinig Multirex 7225 Windows (станок с многофункциональной головкой для рациональной пятисторонней обработки элементов из массивной древесины; новая технология PRO-Torque обеспечивает высокоточное синхронное перемещение для фрезерования по пяти осям) и новым станком UniPin 200 для автоматического нанесения клея на шипы и установки дюбелей, характеризующимся чрезвычайно равномерным нанесением клея, что гарантирует прочность и плотность швов в угловых соединениях, влияющих на общий уровень качества конечного продукта.
Модернизирован и торцовочный станок с толкателем OptiCut S 50. Новизна - в выравнивающем приспособлении для пакетов, которое позволяет повысить точность, а также в автоматической маркировке деталей. Более крупный, чем OptiCut S 50, станок OptiCut S 90 Speed теперь оснащается сервоподъемником шпинделя для распила без сколов и дополнительной обработки. Самый быстрый оптимизирующий пильный станок в мире OptiCut 450 Quantum оснащен новым инструментом OptiStat для анализа производственных данных.
Две других премьеры компания представила в области склеивания и прессования. Одна - новый пресс ProfiPress T Next Generation, производительность которого по сравнению с предшественниками выше на 25% благодаря селективному нагреву, при котором шов нагревается только изнутри, что ведет к сокращению времени цикла прессования. А автоматическое регулирование толщины заготовки позволяет избежать ошибок при изготовлении мебельных щитов. Вторая - пресс ProfiPress L B для склеивания оконных брусков с использованием токов высокой частоты; новация этого высокочастотного пресса - отключаемые цилиндры, позволяющие сократить время на подсобные работы. Специальный верхний прижим обеспечивает минимально возможное смещение заготовок по высоте, синхронно выдвигаемые цилиндры пресса предотвращают смещение по длине.
Средства автоматизации все более активно применяются во всех сферах деятельности концерна. Так, в сканерах Weinig новая автоматическая система регулировки камер позволяет свести к минимуму ошибки оператора и их влияние на конечный результат, а использование новой системы EasyStop упрощает переход к автоматизации станков с ручным обслуживанием. Этот список можно продолжать долго.
Большой вклад сделан специалистами Weinig и во внедрение самого современного программного обеспечения для деревообработки. Например, заточной станок для инструментов Rondamat 1000 CNC, измерительный стенд OptiControl Digital и система управления PowerCom Plus на базе ПО Moulder Master формируют комплекс, который объединяет все технологические этапы создания продукции - от идеи до готового профиля, и выполняет подготовку следующих инструментов и профилей параллельно с выполнением текущих задач. Программный пакет OptiPal на торцовочных станках от Weinig обеспечивает интеллектуальную подготовку списков распилов для изготовления поддонов и ящиков. Millvision и Envision - программные компоненты, используемые для перевода производственных этапов в цифровой вид; они дают возможность соединить в одну цепочку все процессы, начиная с поступления заказа и заканчивая готовым изделием.
Одной из основных тем экспозиции концерна Weinig на выставке стал проектный бизнес, который ведет отдельное подразделение - Weinig Concept. Им было представлено четыре перспективных проекта. Один из них - построение технологической линии для производства опалубки (для строительной промышленности) с возможностью изменения ее размеров и адаптации к конкретным требованиям заказчиков. Второй проект - технология стыкового блочного склеивания, третий - линия для производства панелей CLT, четвертый проект посвящен исследованиям и конструкторской проработке изделий из древесины масличной пальмы.
Директор по коммуникациям концерна Weinig Клаус Мюллер сообщил, что за прошедший год компания достигла 16% роста продаж (эта тенденция получила продолжение и в 2017 году, так как в период до апреля был отмечен рост заказов на 17%, а оборот увеличился на 21%). За счет чего же это стало возможным?
- Оптимизации и модернизация, следование принципам Industry 4.0, союз с Holz-Her и GreCon, дигитализация процессов (под брендом Weinig 4.0 digital) и внедрение интернет-технологий, пристальное внимание к дизайну - вот те факторы, которые способствуют успеху компании, - считает г-н Мюллер. С учетом хороших показателей за прошедший период наблюдательный совет концерна, заседание которого состоялось в ходе ганноверского биеннале, согласовал инвестиционный бюджет в размере 30 млн евро. А значит, в будущем нас ждут новые передовые решения от Weinig.
Самой значимой премьерой известного австрийского производителя Wintersteiger AG (г. Рид-им-Иннкрайс) стал ленточный станок для тонкого распила DSB Singlehead NG XM. В новинке воплощено гибкое и эффективное решение, позволяющее соединять в линию несколько ленточнопильных станков. При разработке станка учитывались актуальные требования клиентов к качеству распила древесины. Эти требования следует выполнять независимо от области применения и типа обрабатываемого материала. В результате был создан ленточнопильный станок, который отлично подходит для распила как сухой, так и сырой древесины, причем максимальная ширина пропила составляет 350 мм, а максимальная высота заготовки - 165 мм. Возможности новинки позволяют значительно упростить процесс изготовления сверхтонких ламелей (толщиной от 1,3 мм) с минимальной толщиной пропила 1,1 мм. Высокий КПД и быстрая окупаемость, надежность и точность в работе - основные преимущества DSB Singlehead NG XM, которые позволяют оптимизировать технологии распила древесины. Например, надежный механизм подачи заготовок в зону пропила: в нижней и верхней части станка расположены приводные роликовые транспортеры. Технология обеспечивает бесперебойную подачу заготовок, даже если есть сильное расхождение по качеству и размерам. Инновационная система прижима и резиновое покрытие роликовых транспортеров гарантируют надежную фиксацию сырых и сухих заготовок при минимальном уровне трения.
Еще один плюс станка - высокотехнологичное управление процессом резания. В частности, в начале пиления инструмент входит в заготовку на небольшой скорости, а ускоряет движение только после полного вхождения в древесину (метод плавного врезания). Этот метод позволяет уменьшить вибрацию и отклонение полотна от заданного направления, продлить срок службы пилы и повысить качество ламелей. Кроме того, станок оборудован датчиками контроля реза, которые контролируют ход полотна и при малейшем его отклонении от заданной траектории работа автоматически прекращается, что предотвращает повреждения пилы и станка, минимизирует объем отходов и повышает рентабельность производства.
Ленточные станки DSB Singlehead NG XM для тонкого распила можно использовать как самостоятельную единицу, а можно объединить в высокопроизводительную систему, последовательно соединив до шести машин, что обеспечит увеличение мощности и пропускной способности.
На выставочном стенде компании (его площадь составляла 500 м2) также можно было ознакомиться с полным ассортиментом продукции Wintersteiger, в том числе с оборудованием модельного ряда TRC для восстановления поверхности древесины - полуавтоматической установкой TRC 1000 и базовой моделью TRC-M Easy. В группе оборудования для тонкого распила, помимо нового станка DSB Singlehead NG XM, были представлены базовая модель DSB Compact 310, ленточные станки с тонким пропилом DSB Twinhead NG XM и DSB Singlehead 660. Рамные станки Wintersteiger были представлены моделью DSG Notum. Кроме того, на стенде демонстрировались ленточные и рамные пилы производства Wintersteiger с напайками из твердого сплава и стеллита.
Директор по маркетингу и коммуникациям итальянской компании Wirutex S.R.L. Констанца Боиани, с которой на минувшей выставке Xylexpo в Милане нас познакомили коллеги из компании Biesse, была откровенно рада снова видеть журналистов из России:
- Чао, друзья! Мы привезли в Ганновер новые продукты и решения в сфере оборудования и режущего инструмента, в частности, Gladio - небольшой фрезер, идеально подходящий для обработки деталей в индивидуальном производстве, а также комплекты инструментов для инструментального магазина обрабатывающих центров Rover NC, созданные в сотрудничестве с Biesse.
Шведская компания WoodEye AB представила сканер древесины нового поколения - WoodEye 6 с улучшенными (по сравнению с предыдущими моделями) характеристиками, а также уникальной функцией обнаружения дефектов, которая особенно полезна для производителей оконных рам. Впервые специалисты WoodEye продемонстрировали публике датчик ядровой древесины, который может точно отличать ядровую древесину от заболони. На выставочном стенде компании WoodEye была установлена линия поперечной распиловки с оптимизатором, разработанная совместно с одной из компаний-партнеров. Высокая скорость работы этого оборудования произвела сильное впечатление на посетителей.
- В последние два года в Центральной Европе началась новая волна автоматизации производства паркета и напольных покрытий, а в этой сфере сканер «WoodEye Паркет» просто незаменим благодаря высокой точности обнаружения минимальных дефектов ламелей дуба, а также измерения толщины доски и ее углов, - рассказал менеджер по продажам компании WoodEye Эрик Лильенгрен. - Три разных вида сканера были проданы в ходе выставки, один из них отправился в Россию; заложен крепкий фундамент для переговоров с рядом потенциальных покупателей. Столь оживленный интерес к своей продукции мы отмечали здесь впервые после финансового кризиса 2008 года. По моему мнению, тут сыграли свою роль растущая уверенность в стабильности рынка и наличие у компании WoodEye множества технологических новинок, позволяющих клиентам повысить эффективность производства.
Компания Wood-Mizer (США) приступила к выпуску высокопроизводительной линии Titan, возможности которой позволяют распиливать более 150 м3 круглой древесины в смену. Конструктивно линия спроектирована так, чтобы обеспечить высочайшую надежность и бесперебойную работу оборудования. На выставке Ligna 2017 были показаны некоторые компоненты линии Titan: основа линии - широколенточная горизонтальная установка WB2000, сдвоенный вертикальный станок с широкими ленточными пилами, а также мощная продольно-обрезная и многопильная машины. Всё оборудование Titan окрашено в синий цвет, чтобы отличать его от хорошо известных оранжевых станков Wood-Mizer с узкими ленточными пилами.
Еще одной новинкой от Wood-Mizer, продемонстрированной в Ганновере, стала новая конструкция пилящей головы ленточнопильного станка LX с узкими ленточными пилами, в конструкцию которого входит рама xFRAME для перемещения пильного узла по двум рельсам.
Новая ленточная пила Vortex с уникальным профилем предназначена для пиления древесины и одновременного удаления опилок с поверхности распиленного материала. Профиль пилы был разработан на заводе Wood-Mizer в США, это техническое решение заинтересует в первую очередь производителей поддонов, которым необходима чистая палетная дощечка. Опыт эксплуатации пилы Vortex на предприятиях в США, результаты ее испытаний на производствах в Европе, Азии и Африке выявили значительный интерес производителей поддонов к этому инструменту.
На стенде компании также был представлен широкий ассортимент продукции под маркой Wood-Mizer Tools: более 2000 типоразмеров режущего инструмента - круглых и рамных пил, фуговальных ножей и ленточных пил. В числе другого оборудования следует отметить высокопроизводительный ленточный многопильный станок HR700, созданный по модульному принципу и снабженный круговым конвейером Merry-Go-Round для возврата недопиленного бруса на вход установки, а также хорошо известные станки серий LT, оборудование для заточки и разводки ленточных пил и полный спектр узких ленточных пил.
К великому сожалению, за пять выставочных дней, до предела насыщенных событиями, мы не смогли пообщаться со всеми экспонентами, которые того, безусловно, заслуживали, и присмотреться ко всем достойным внимания новинкам. Это было просто физически невозможно - как невозможно и рассказать о них в рамках журнальной публикации. Но ничего страшного: во-первых, «эхо» Ligna будет разноситься по отрасли еще долго, и мы не раз в своих публикациях обратимся к технике, инструментам, оборудованию и услугам компаний, которые были представлены в павильонах Hannover Messe в майские дни 2017 года. А во-вторых, уже начат обратный отсчет времени до следующей выставки - и мы понемногу начинаем подготовку к ней, чтобы непременно наверстать упущенное. Напомним: очередная Ligna пройдет в выставочном центре Ганновера 27-31 мая 2019 года. До встречи!
«ЛесПромИнформ»
Фото Максима ПИРУСА, Андрея ЗАБЕЛИНА, компаний-экспонентов