Учиться, учиться и учиться!
Или как повысить эффективность производства с помощью матрицы компетенций
На предприятиях лесного холдинга «Алтайлес» осуществляется масштабный проект по повышению эффективности производства при участии Федерального центра компетенций. О мероприятиях и результатах проекта я попросил рассказать генерального директора холдинга Ивана Ключникова и директора Павловского ДОКа Алексея Гильманова.
– По какой причине вы приняли решение об участии в проекте?
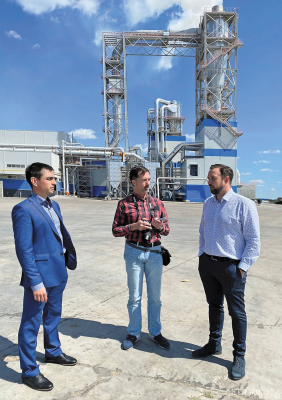
Иван Ключников: Не зря говорят, построить завод – это только 35–40% дела, самое главное обустроить его так, чтобы он стал полноценно действующим производством: обучить людей, наладить цепочки. Сейчас, на четвертом году после пуска, оценил бы удовлетворенность примерно в 80%. Еще далеко не все умеем, видим много вещей, которые можно улучшить, но пока не знаем как. А если возникает интересная идея, не всегда знаем, как ее использовать. Не хватает системного подхода при решении задач.
– С какими трудностями довелось столкнуться на этапе реализации?
ИК: Пожалуй, самым сложным оказалось преодолеть инертность и скепсис персонала. Парадоксально, но по всей структурной вертикали проще всего было «раскачать» среднее звено: скажем, начальник производства позитивно отнесся к проекту и, поверив в возможность улучшений, быстро включился. А вот руководители и те, кто непосредственно занимается рабочими процессами, вовлекались не сразу. Пришлось даже привлекать коучей из нашего регионального центра развития компетенций. После первых наглядных результатов дело пошло веселей.
Успех проекта вижу среди прочего и в том, что удалось перенастроить мышление, убедить людей, что непрерывные улучшения возможны и необходимы. А кроме того, даже визуально производство становится другим.
Алексей Гильманов: Порой полезно перенять опыт других предприятий холдинга. Допустим, Павловский ДОК вошел в проект на 6 месяцев раньше «Содружества», но когда мы съездили к ним в гости, изучили результаты реализации их программы повышения производительности труда – оказалось, что в этом направлении они опережают и нас, и Рубцовский комбинат. Есть чему поучиться у коллег!
– Как строилось взаимодействие со специалистами Федерального центра компетенций?
АГ: ФЦК работает комплексно. К компании прикрепляется куратор, который на месте от начала и до конца ведет работу по повышению производительности в течение полугода. Также в команде есть специалисты, привлекаемые для отдельных видов работ или проведения семинаров. По факту реализация такого проекта начинается с вовлечения инженерно-технического состава предприятия в процесс усовершенствования. Прежде всего, нужно объяснить людям, для чего это нужно. У консультантов это получается без труда и эффективно, с помощью проверенных инструментов и практик, деловых игр.
ИК: Специалисты ФЦК правильно отметили: важно не только создать компетенцию (в рамках совместного проекта), но и поддерживать, а затем развивать – уже самостоятельно. И мы задумались о необходимости в холдинге сотрудника, который будет постоянно этим заниматься.
– Какие конкретные новшества внедрены на предприятии в рамках проекта?
АГ: Зачастую «находки» кажутся мелочами, но на эффективном производстве мелочей нет – порой даже самое незначительное усовершенствование может оказаться необычайно полезным. Простой пример. Сотрудников ремонтной службы мы обязали на любой вызов по устранению неполадок брать с собой необходимый инструмент. Казалось бы, очевидно. Теперь, получив сигнал по рации, ремонтник спешит на вызов не с пустыми руками (или на ходу выбранными средствами), а с установленным набором самых востребованных инструментов, позволяющих безотлагательно начать работу. На случай серьезного вмешательства также подготовлен необходимый комплект. В результате время простоев сократилось в среднем на 75%.
А на участке размола щепы мы установили специальный ящик с инструментами для обслуживания установки, поскольку заметили, что на регулярные перемещения инструмента при обслуживании тратится много времени. И если раньше на замену размольной гарнитуры уходило восемь часов, то сейчас по регламенту полтора часа. И это всего лишь за счет переноса инструмента на месте работы и постоянных тренировок работников.
Проводим видеосъемку разных периодически выполняемых работ и потом анализируем, где и на чем теряем время, какие «узкие места» приводят к простою оборудования. И устраняем их.
ИК: Мы распространяем принцип бережливого производства на всех предприятиях холдинга. В частности, на Павловском ДОКе полностью пересмотрена организация слесарной мастерской. Реформирована деятельность на участке шлифовке плит – прежде там работали два человека, теперь все операции выполняет один сотрудник. Оптимизирована структура склада сырья. Изменений проведено немало, но резервов для совершенствования еще больше, предстоит очень большая работа.
АГ: Эталонный пример и успешного решения, и взаимодействия в холдинге: на участке шлифовки плит совместили пост упаковки с последним постом производственной линии MDF, что позволило отказаться от одного погрузчика. То есть мы сэкономили целую единицу внутрицеховой техники – и этой машиной поделились с Рубцовским заводом, у которого в ней была острая потребность. А сами вполне справляемся двумя оставшимися.
ИК: Из всех наших предприятий Павловский ДОК наиболее успешно работает с матрицей компетенций, не снижая темпов даже после завершения проекта с ФЦК. Это очень важно, ведь тут заложен в том числе и потенциал роста оплаты труда операторов. Например, в центральной операторской ДОКа в смену работают восемь человек: один умеет обслуживать, допустим, только один участок, другой – два, третий – три или четыре. И, разумеется, когда мы обдумываем апгрейды, исходя из ценности для компании, большое значение имеют компетенции и квалификация. Верно говорил Суворов: «Воевать надо не числом, а уменьем» – и мы готовы распределять фонд зарплаты так, чтобы квалифицированные сотрудники, выполняя самые сложные задачи, получали больше.
Тем самым можно решить и насущную проблему утечки персонала. Ведь работа действительно сложная, но бесконечно раскочегаривать затраты на персонал невозможно, поскольку это сказывается на себестоимости продукции. Пусть на участке будет меньше работников, но оплата их труда будет выше.
АГ: Да, за последние полгода мы вырастили двух мастеров, которые, помимо своего функционала, могут выполнять обязанности оператора пресса (а это ключевая позиция основной технологической линии), а также двух операторов пресса, которые могут работать еще и на участках размола щепы и сушки. Подготовка универсалов – дело небыстрое, как оказалось, не каждый готов осваивать соседний участок, хотя в результате увеличивается доход. Мы сразу сделали ставку на то, чтоб оператор каждого участка разбирался в работе, но и в том, что происходит до и после него по технологии. Такой подход обеспечивает не только взаимозаменяемость, но и оперативное мышление, особенно необходимое в нестандартных ситуациях, улучшает координацию операторов по всему процессу.
Но сегодня мы себя уже надежно обезопасили, и в центральной операторской нет никого, кто работал бы меньше года. Чтобы было понятно: первый год – критический, в это время фиксируется самая большая текучка персонала. Особенно сильно она ударила в первые месяцы после запуска – люди просто не выдерживали бесконечных остановок, отладок и переналадок. Многих это отпугнуло.
– Кто и как обучает производственный персонал?
ИК: Когда год спустя после старта производства сложилась сложная ситуация и из тех, кого обучили «оригиналы» (пусконаладчики оборудования, представители компаний-производителей), осталось, дай Бог, 25–30%, как раз эти специалисты смогли натаскать новых работников. Не без труда, но мы справились. И очень серьезно озадачились проблемой квалифицированного персонала. Тут большая роль отводится ИТР – есть у нас несколько хороших специалистов. Еще двоих мы готовим.
Процесс обучения длительный. Допустим, базовый уровень оператора рафинера для нормального обслуживания техники достигается за три с половиной месяца.
Работает много молодых людей, а они склонны к перемене мест и ориентированы на высокую зарплату. И нам приходится бороться за операторов с соседними предприятиями, чтобы не переманили.
Теперь, с введением матрицы компетенций, уровень оплаты труда сотрудника зависит от того, сколько он знает и умеет. Мы стали доплачивать за компетенции, но как это работает, все поняли только тогда, когда тех, кто не хочет развиваться, начали сокращать. У нас всегда есть резерв стажеров, которые начинают с низовых позиций, но мотивированы учиться и осваивать технику.
Основной костяк производства, наше «золото» – это 28 человек, которым созданы такие хорошие условия, чтобы они просто не смогли уйти. И получается, что это выгодно и им, и нам.
Текст Максим Пирус