Способы облицовывания кромок. Часть 1
Постформинг
Технологии постформинга (нем. postforming) и софтформинга (нем. softforming) были придуманы в Германии и вот уже несколько десятилетий используются мебельщиками всего мира.
1)
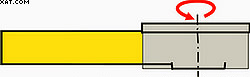
2)
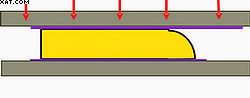
3)
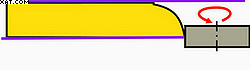
4)
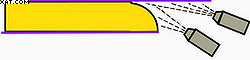
5)
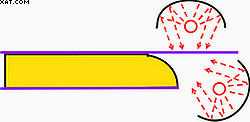
6)
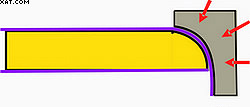
7)
Уступ для выхода клея, выдавленного
при облицовывании пласти
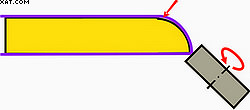
Рис. 1. Последовательность операций,
выполняемых при облицовывании кромок
методом постформинга (Postforming)
К сожалению, ни в учебниках по деревообработке, ни в специальной литературе нет ни четких определений этих способов облицовывания кромок, ни истории их создания. Многие наши современные конструкторы мебели просто не знают, как создается облицованный профиль на кромках заготовок из древесных плит. И это незнание уже давно оказывает отрицательное влияние на конструкции многих отечественных изделий, из-за своей «прямоугольности» заметно уступающих по внешнему виду зарубежным прототипам.
Технологический прорыв
В конце 40-х годов прошлого века, сразу после окончания Второй мировой войны, в Европе началось восстановление разрушенных городов и активное строительство нового жилья. Потребовалось много недорогой мебели, спрос на которую никак не могли удовлетворить мелкие ремесленные мастерские, где самым сложным оборудованием оставались фуговальные и рейсмусовые станки. Нужен был прорыв в технологиях.
И такой прорыв произошел благодаря использованию в мебельном производстве древесно-стружечных плит, первый завод по изготовлению которых был пущен в Германии еще в 1942 году. Этот шаг подвиг множество изобретателей к созданию принципиально нового оборудования. Так, в 1951 году Эрих Клессманн (Erich Klessmann) основал фирму IMA (Industrie Maschinenanlagen Klessmann -«Промышленные установки Клессмана»), освоившую производство односторонних станков мод. AVM для облицовывания кромок заготовок из ДСП полосой натурального шпона. Серийное производство таких станков было начато уже в 1953 году, после их показа на ярмарке в Ганновере. Они работали с применением клеев на основе карбамидных смол, отверждение которых происходило за счет воздействия металлического ленточного нагревателя.
в 1960 году Ойген Хорнбергер (Eugen Hornberger) совместно с Герхардом Шулером (Gerhard Schuler) создали фирму Homag (Homag — Hornberger Maschinengesellschaft — «машиностроительное общество Хорнбергера»), уже в 1962 году на выставке LIGNA в Ганновере впервые продемонстрировавшую свой совсем небольшой односторонний кромкооблицовочный станок, в котором для наклеивания полосы из шпона использовался клей-расплав, наносившийся на кромку заготовки в процеcсе ее обработки. Этот станок произвел настоящую революцию в мебельном производстве, и его усовершенствованные копии выпускаются сегодня десятками фирм во всем мире.
В 1969 году немецкая фирма Brandt разработала способ облицовывания кромок с использованием реактивации горячим воздухом клея-расплава, заранее нанесенного на кромочный материал, а также двухсторонние кромкооблицовочные станки, на которых производилась обработка деталей с использованием этого способа. Но ни один из этих станков не позволял получить профиль на кромке.
Постформинг («последующее формование»)
К концу 1960-х мебели из ДСП, собранной из прямоугольных щитовых деталей с плоскими кромками с помощью таких станков, производилось все больше. Она отличалась прямыми острыми линиями и минимализмом декора и к началу 70-х годов прошлого века уже успела изрядно надоесть покупателям, а в Австрии даже получила название kastenmöbel — мебель-ящик, или ящичная мебель. Рынок, где потребитель с послевоенных времен уже разбогател, потребовал новизны. Но технология мебельного производства была ориентирована на производство изделий из плитных материалов — преимущественно из ДСП. Причем к середине 1970-х к ним добавилась и древесно-волокнистая плита сухого способа производства. Способ смягчить форму кромок щитовых деталей был разработан специалистами фирмы Brandt, которые создали первый позиционный станок для облицовывания кромок способом, названным «постформинг» (Postforming).
1)
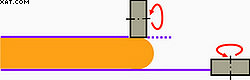
2)
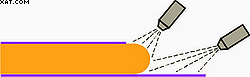
3)
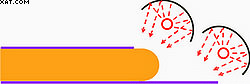
4)
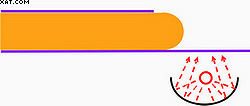
5)
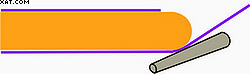
6)
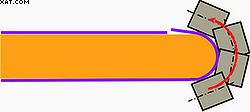
7)
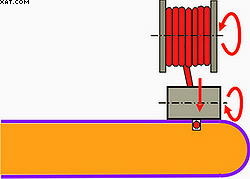
Рис. 2. Последовательность операций,
выполняемых при облицовывании кромок
методом постформинга на станках проходного
типа
Технология заключается в облицовывании профиля прямолинейной кромки заготовки путем приклеивания к нему свеса облицовочного материала пласти. Название новой технологии произошло от двух слов: post — «позже, после» и form — «формовать»; таким образом, Postforming («постформинг») можно перевести как «последующее формование».
Процесс изготовления деталей с кромками, облицованными этим способом (рис. 1), изначально включал в себя фрезерование профиля на одной или двух параллельных кромках щитовой заготовки (поз. 1); облицовывание заготовки одновременно с двух сторон (поз. 2); удаление нижнего свеса облицовочного материала пласти (поз. 3); нанесение клея на основе ПВА-дисперсии путем распыления на профиль кромки и оборотную сторону облицовочного материала (поз. 4); нагрев облицовочного пластика посредством ИК-излучения и подсушивание клеевых слоев (поз. 5); прижатие облицовочного материала к профилю на кромке и его обжатие (поз. 6); удаление свеса облицовочного материала со снятием фаски на ребре (поз. 7).
Для облицовывания этим способом был специально разработан декоративный бумажно-слоистый пластик (дбсп), термореактивные пропиточные смолы которого содержат соответствующие добавки, придающие ему способность изгибаться при нагреве, вследствие чего его называют постформуемым (постформируемым). Но для облицовывания кромок способом постформинга могут также применяться натуральный шпон (дублированный и недублированный) и любые однослойные пластики (в том числе термопластичные). Причем облицовываемый профиль может иметь различную форму сечения (рис. 3).
Простое решение
К концу 1980-х на отечественном рынке еще не было такого большого числа представительств крупных зарубежных производителей плит с кромками, облицованными способом «постформинг», как сейчас, а потребность в столешницах и дверях для мебели, используемой на кухне, была очень велика.
Мелкие производители кухонной мебели проявили интерес к пусть и малопроизводительному, но достаточно простому и дешевому оборудованию для изготовления столешниц и мебельных дверок. Выходом из положения стал станок со сваренной их металлического уголка станиной, в верхней части которой на откидывающейся рамке были смонтированы горизонтальные инфракрасные нагреватели, а на другой рамке — эластичное резиновое полотно.
Заготовка со свесом облицовочного материала, предназначенным для заворачивания на кромку, устанавливалась в «карман» на станине. Оператор вручную распылял клей на кромку заготовки и оборотную сторону пластика и подводил к заготовке ИК-нагреватели. Когда пластик размягчался, а нагретый подсушенный клей приобретал необходимую липкость, оператор убирал нагреватели и подводил к заготовке вторую рамку. Установленное на ней полотно резины огибало профиль и с некоторым усилием прижимало свес пластика к кромке. После выдержки полотно отводилось, а профиль с помощью резинового ролика дополнительно прикатывался к кромке вручную. Затем заготовка снималась, а оставшийся свес удалялся ручным фрезером.
Главные недостатки такого устройства — невозможность заворачивания свеса на 180° и его слабый прижим к кромке, что часто вызывало отслоение пластика. Причем, его ребро из-за снятой фаски было заострено и создавало опасность при эксплуатации готового изделия мебели. Лучшие результаты могли быть получены с применением контактных полиуретановых клеев, но они существенно дороже клеев на основе ПВА-дисперсии, а это не устраивало мелких производителей мебели.
К тому же такие установки, как описанная выше, не могли обеспечить облицовывание кромок заготовок длиной более 3 м, в то время как для современной кухни часто требуются столешницы длиной более 4 м.
И когда к концу 1990-х фасады для кухонь с дверями, кромки которых, облицованные способом постформинга, уже вышли из моды, а зарубежные поставщики организовали в нашей стране склады продукции с широкой номенклатурой столешниц (часто длиной до 5,5 м), у мелких предприятий необходимость организации собственного производства таких деталей отпала.
Проходные станки
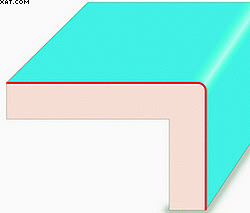
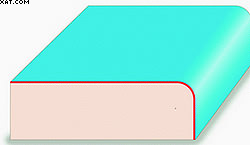
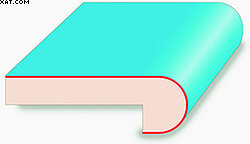
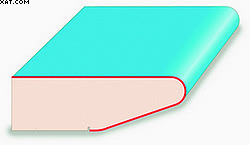
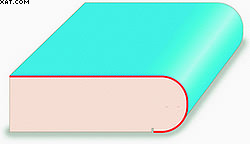

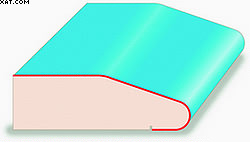
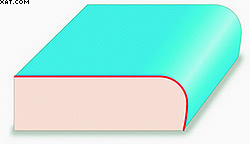
Рис. 3. Варианты профилей сечения кромок,
облицованных методом постформинга
Однако различные детали с кромками, облицованными способом постформинга, широко используются и сегодня. Их чаще всего изготавливают крупные производители древесно-стружечных плит, которых не устраивали возможности позиционных станков. И поэтому в 1976 году компания IMA разработала и получила патент на станок проходного типа для облицовывания кромок щитовых деталей способом постформинга; за основу его конструкции были взяты узлы и агрегаты кромкооблицовочных станков, которые работали с использованием полосовых и рулонных кромочных материалов.
Однако состав операций, выполнявшихся на этом станке (рис. 2), несколько отличался от операций, выполнявшихся на позиционном станке. При обработке заготовки на станке проходного типа сразу же производилось удаление верхнего свеса облицовочного материала пласти и калибрование длины нижнего (поз. 1 рис. 2); нанесение распылением клея на основе ПВА-дисперсии на профиль и оборотную сторону облицовки (поз. 2 рис. 2); нагрев облицовки с наружной стороны (поз. 3 рис. 2); высушивание и разогрев клеевых слоев на профиле и облицовке (поз. 4 рис. 2); начало загибания свеса на профиль в направлении сверху вниз косо расположенным стержнем (поз. 5 рис. 2); прикатывание облицовочного материала к профилю и его обжим (поз. 6 рис. 2); удаление свеса или пропиливание паза по оборотной стороне заготовки с вдавливанием в него и последующим расплавлением пластмассовой проволоки (поз. 7 рис. 2), препятствующей проникновению влаги внутрь материала детали.
Способ постформинга стал широко применяться преимущественно для деталей, традиционно облицовываемых ДБСП: дверей и столешниц кухонной мебели. При этом считается, что радиус закругления (изгиба) облицовочного материала — не меньше 10-кратной толщины этого материала.
Но у этого способа есть и серьезный недостаток — невозможность обеспечения сохранности свесов при транспортировке заготовок между операциями облицовывания пластей и кромок. Тем более что к середине 1970-х пластики и шпон стали вытесняться из производства тонкими пленками на основе бумаги. А увеличение объемов выпуска и применения полноформатных плит, облицованных на заводе-изготовителе, вообще сделало получение свесов облицовочного материала вдоль кромок заготовок ненужным.
В конце 90-х годов прошлого века теми же фирмами — IMA и Homag почти одновременно были разработаны станки, в которых использовался так называемый прямой постформинг (нем. Direkt Postforming). При этом способе необходимый профиль кромки в уже облицованной с двух сторон плите выполнялся с помощью фрезерования (так что слой облицовки одной из пластей оставался нетронутым) и в том же станке сразу же загибался и приклеивался к сформированному профилю. Но из-за сложности наладки, высоких требований к инструменту, прочности самой облицовки и в силу других причин этот способ широкого распространения не нашел, и в России пока не закуплено ни одного такого станка.
Одно из достоинств деталей, кромки которых облицованы способом постформинга, — плавный переход материала пласти на кромку, зрительно создающий впечатление монолитности материала, и отсутствие стыка между облицовочным материалом пласти и кромки, что предотвращает их отслоение из-за возможного попадания влаги через этот стык.
Но сегодня для облицовывания прямолинейных, профильных в сечении кромок щитовых деталей на мебельных предприятиях чаще используется способ, который называется «софтформинг» (softforming). Об этой технологии, разработанной в развитие постформинга, мы расскажем в следующем номере журнала.
Владимир КОЛОМИЙЦЕВ,
компания «МедиаТехнологии»
Способы облицовывания кромок. Часть 2. Софтформинг
Постформинг − форма под защитой