Деревообрабатывающее оборудование. Классификация Eumabois. Часть 7
Станки продольно-фрезерные
В классе 02.04 «Фрезерные и строгальные станки» по классификации Eumabois представлены станки для чистовой обработки древесины с целью получения плоских или профильных поверхностей.
Часть 1. Оборудование склада сырья круглых лесоматериалов
Часть 2. Лесопильное оборудование
Часть 3. Оборудование для сушки пиломатериалов
Часть 4. Торцовочные пильные станки для вторичной деревообработки
Часть 5. Круглопильные станки: прирезные и форматные
Часть 6. Станки ленточнопильные столярные
Часть 8. Станки фрезерные и фрезерно-копировальные
Часть 9. Шипорезные станки
Часть 10. Станки для обработки и облицовывания кромок
Часть 11. Станки для выборки отверстий и пазови
Часть 12. Станки токарные
Часть 13. Станки шлифовальные
Часть 14. Оборудование для сращивания на зубчатый шип
Часть 15. Оборудование для склеивания массивной древесины
Часть 16. Оборудование для отделки древесины жидкими лакокрасочными материалами
Часть 17. Оборудование для облицовывания древесины пленочными материалами
Часть 18. Оборудование для производства окон и дверей
Часть 19. Специализированное оборудование для производства стульев
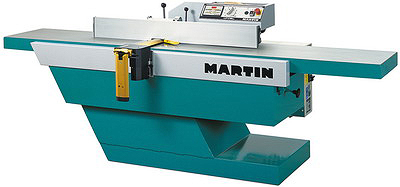
Рис. 1. Фуговальный станок Martin T 54 (ФРГ)
Термин «фрезерование» означает обработку материала вращающимся инструментом. Принято различать продольно-фрезерные и фрезерные станки. Продольно-фрезерные являются станками проходного типа, т. е. такими, в которых материал движется относительно режущего инструмента. Фрезерные - это, как правило, станки позиционного типа, в которых материал (заготовка) жестко фиксирован в момент обработки ножами или фрезами разной конструкции.
Термин «строгание» в деревообработке означает создание гладкой поверхности на заготовке путем механической обработки прямолинейно движущимся инструментом (ножом фуганка или рубанка, ножом шпонострогального станка, цикли). Поэтому, строго говоря, строгальными можно называть только шпонострогальные и циклевальные станки. Однако почти повсеместно продольно-фрезерные станки называют строгальными, так как результатом их работы является гладкая поверхность на обрабатываемой заготовке.
Продольно-фрезерные станки подразделяются на фуговальные, рейсмусовые и четырехсторонние.
Фуговальные станки предназначены для базирования, т. е. создания на заготовке одной или двух технологических баз (термин «фугование» означает получение ровной плоской поверхности). Обычно объектами обработки являются черновые заготовки, полученные после поперечного и/или продольного раскроя сухих пиломатериалов. Такие заготовки всегда покоробленны, и их дальнейшая обработка возможна только после создания хотя бы одной идеально ровной поверхности путем фугования пласти и/или кромки заготовки.
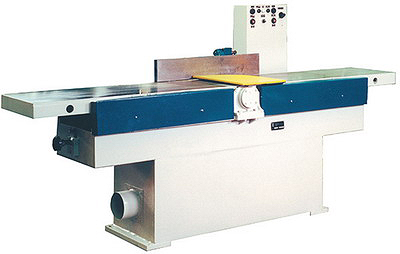
Рис. 2. Фуговальный станок СФ4(К)(Кировский станкостроительный завод)
На рис. 1 показан общий вид типичного фуговального станка. Привод ножевого вала осуществляется от электродвигателя через клиноременную передачу. Глубина снимаемого слоя регулируется путем изменения высоты переднего рабочего стола. Направляющая линейка позволяет выполнять обработку под заданным углом к кромке. У двухстороннего фуговального станка за ножевым валом находится еще и вертикальный фрезерный шпиндель для обработки кромки заготовок. Подача заготовок выполняется вручную или с помощью автоподатчика, расположенного над задним столом (рис. 2).
Основные технические характеристики фуговальных станков:
- длина ножевого вала (ширина фугования) 300-620 мм;
- макс. высота снимаемого слоя 6 мм;
- частота вращения ножевого вала 3000-6000 об./мин.;
- мощность привода ножевого вала 3-6 кВт;
- общая длина рабочих столов 600-3000 мм;
- мин. длина заготовки 400 мм;
- масса станков 400-1200 кг.
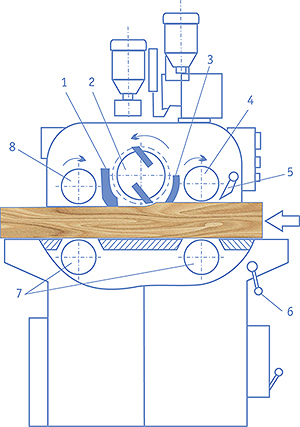
Рис. 3. Схема рейсмусового станка:
1 – прижим задний, 2 – ножевой вал,
3 – прижим передний, 4 – валец подающий передний, 5 – когтевая защита, 6 – фиксатор высоты стола, 7 – опорные ролики, 8 – валец подающий задний
Современные фуговальные станки отличают: увеличенная длина столов, цифровой указатель глубины строгания, электрическая настройка высоты переднего стола и наклона направляющей линейки.
Рейсмусовые станки выполняют обработку заготовок в размер по толщине путем фрезерования поверхности, противоположной базовой (рис. 3). Название станков происходит от названия инструмента рейсмас (нем. Reißmaß), который служит для проведения на заготовке разметочных линий, параллельных выбранной базовой линии. В сегодняшнем понимании рейсмусовать означает задать детали нужный размер по толщине. Интересно, что в немецком языке такие станки называют Dickhobelmaschinen, что буквально означает «строгающие по толщине».
Обработка выполняется при вальцовой подаче заготовок по гладкому столу станка с опорными роликами для уменьшения сил трения. Передний подающий валец рифленый, задний валец - гладкий. Для предотвращения обратного выброса заготовки служит когтевая завеса. Подающий валец делают ступенчатым, что позволяет обрабатывать заготовки с разнотолщинностью 5-8 мм.
Настройка на нужный размер достигается вертикальным перемещением нижнего стола. Выпускаются также станки с постоянным уровнем нижнего стола и вертикальным перемещением узла резания.
Основные технические характеристики рейсмусовых станков:
- ширина обработки (длина ножевого вала) 300-1200 мм;
- мин. толщина заготовок 5 мм, макс. толщина 300 мм;
- скорость подачи до 30 м/мин.;
- мин. длина заготовки 250 мм;
- масса станка 400-1600 кг.
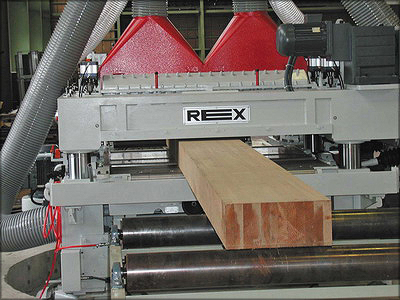
Рис. 4. Рейсмусовый станок HO-63 (Rex Maschinenfabrik, ФРГ)
Современные станки отличают: автоматическая настройка высоты стола, цифровая индексация заданной толщины обработки, бесступенчатая настройка скорости подачи в зависимости от усилий резания.
В России фуговальные и рейсмусовые станки выпускают Кировский станкозавод, завод «КОДОС» из Костромы, «Красный металлист» из Ставрополя. Из импортных машин популярны станки немецких и итальянских фирм. Особо следует отметить большие рейсмусовые станки немецкой фирмы Rex Maschinenfabrik (рис. 4). У этого станка рабочий стол находится всегда на одном уровне, а настройка на толщину заготовки выполняется подъемом верхней части. Кроме того, верхняя часть может поворачиваться вокруг вертикальной оси, что удобно при строгании крупных строительных деталей, в том числе гнутоклееных. Рабочая ширина строгания на станке НО-63 - до 1100 мм при высоте детали до 280 мм.
Существуют также двухсторонние рейсмусовые станки. Конструкция станков этого класса позволяет выполнять операции фугования (базирования) и рейсмусования (строгания в размер по толщине). Можно выделить три разновидности станков для выполнения этих операций (рис. 5).
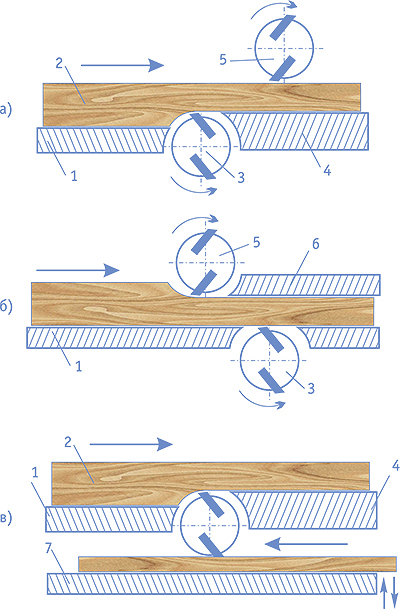
Рис. 5. Типы двухсторонних рейсмусовых станков: а – фуговально-рейсмусовый, б – двухрейсмусовый, в – с одним ножевым валом (1 – передний стол, 2 – заготовка, 3 – фуговальный ножевой вал, 4 – задний стол, 5 – рейсмусовый ножевой вал, 6 – базирующий стол, 7 – нижний стол рейсмусового устройства). Механизмы подачи не указаны
Больше других распространены фуговально-рейсмусовые станки (рис. 5а). В их конструкции имеется нижний ножевой вал для создания базисной поверхности и верхний ножевой вал, высота которого над нижним столом определяет толщину обрабатываемой заготовки.
Двухрейсмусовыми станками (рис. 5б) называют станки, у которых первым по ходу расположен верхний (рейсмусовый) ножевой вал. Подобные станки применяют для обработки жестких, недеформируемых материалов, а также тонких (до 5 мм) гибких деталей.
У станков с одним валом (рис. 5в) при прохождении заготовки сверху выполняется фугование, а при обратном ходе заготовки под ножевым валом - строгание в размер по толщине (толщина настраивается установкой нижнего стола по высоте).
Фуговально-рейсмусовый станок С2ФР6 Курганского ЗДС представляет собой гибрид обычного фуговального станка ССФ6 и одностороннего рейсмусового станка. За один проход на заготовке создается базовая поверхность и выполняется строгание в заданный размер по толщине. Максимальный размер заготовки - 600 мм по ширине, размер по толщине - от 8 до 170 мм.
Компания Hofmann Holzbearbeit-ungs Maschinen (ФРГ) производит фуговально-рейсмусовый станок AD515 (рис. 6), конструкция которого позволяет одновременно обрабатывать две пласти заготовок за один проход. Два фуговальных вала в станке позволяют уменьшить глубину строгания на каждом валу и повысить качество обработки нижней пласти заготовок, а пильный узел на выходе дает возможность не устанавливать в линию дополнительный прирезной станок для получения деталей нужной ширины.
Четырехсторонние станки служат для одновременной обработки пиломатериалов или заготовок с четырех сторон. Конструкция этого оборудования позволяет выполнять операции фугования, рейсмусования и фрезерования кромок заготовок и получать таким образом за один проход детали нужной формы и размеров. Встречаются и трехсторонние станки подобной конструкции.
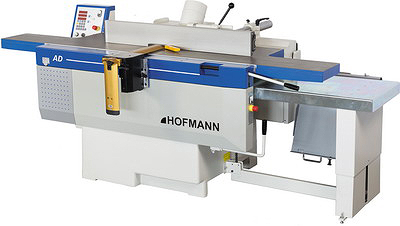
Рис. 6. Фуговально-рейсмусовый станок AD515 (Hofmann Holzbearbeitungs Maschinen, ФРГ)
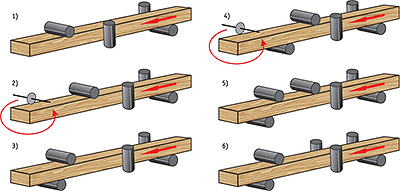
Рис. 7. Схемы многошпиндельных продольно-фрезерных станков (Weinig, ФРГ): 1) четырехшпиндельный; 2) пятишпиндельный с пятым универсальным шпинделем; 3) пятишпиндельный с дополнительным нижним шпинделем для профильной обработки нижней пласти заготовки; 4) шестишпиндельный с универсальным шпинделем; 5) шестишпиндельный с дополнительным верхним шпинделем для профильной обработки верхней пласти заготовки; 6) шестишпиндельный с двумя правыми шпинделями
Обычно станки снабжены четырьмя шпинделями - нижним (фуговальным), правым, левым и верхним. При вальцовой подаче заготовки последовательно обрабатываются с четырех сторон, причем все или некоторые ножи могут быть профильными, что позволяет получать за один проход детали сложного профиля (доски пола, наличники, плинтусы, доски обшивки и т. п.).
Строгально-калевочные станки отличаются от обычных строгальных только наличием специального инструмента - вертикальными шпинделями с профильными ножами для формирования калевки (фигурной кромки).
Основные технические характеристики продольно-фрезерных станков:
- макс. ширина заготовки 300 мм;
- макс. скорость подачи обычно 40 м/мин., хотя имеются станки для получения строганных пиломатериалов со скоростью подачи до 300 м/мин.;
- число шпинделей - от 4 до 10; встречаются станки с тремя шпинделями для трехсторонней обработки;
- частота вращения шпинделей 4000-12000 об./мин.
На рис. 7 показаны варианты расположения шпинделей на станках Profimat производства компании Weinig.
Перечислим основные конструктивные особенности современных станков для получения профильных деталей (на примере станков фирмы Weinig) (рис. 8).
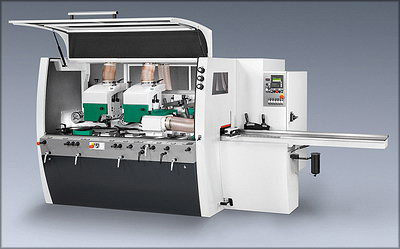
Рис. 8. Продольно-фрезерный станок Powermat 600 (Weinig)
У станков тяжелая литая станина, которая хорошо гасит вибрации и отличается высокой формостабильностью при длительной эксплуатации. Для привода шпинделей использованы подшипники с высокой несущей способностью и плоскоременной привод. Снятие и установка ножевых головок на шпиндели может выполняться «одним щелчком» с помощью специальной системы. Новые конструкции привода шпинделей позволили увеличить их скорость до 12 тыс. об./мин., что дает возможность увеличить скорость подачи материала (производительность станка) без снижения качества обработки поверхности. Для обеспечения надежного фугования нижней пласти заготовок на первом нижнем (фуговальном) шпинделе может быть установлена пазовая фреза, которой фрезеруется канавка, служащая базой для обработки на остальных шпинделях.
Увеличен диапазон осевой настройки шпинделей по вертикали и горизонтали, что позволяет менять инструмент с помощью позиционирования шпинделей. Внедрен новый способ крепления ножевых головок на валу шпинделя с помощью гидрозажима, что позволило снизить биение ножей до 0,005 мм и добиться такого качества обработки поверхностей, что перед отделкой не требуется шлифование.
Специально для обеспечения качественной работы строгальных станков разработано оборудование для изготовления и заточки профильных ножей (например, станки Rondomat). Надежное крепление ножей в головке с помощью одного винта и системы Joint, устанавливаемой прямо на станке, позволяет добиться расположения режущих ножей строго на одной окружности и минимизировать волну строгания.
Для деления заготовок по толщине станки могут быть дополнены пильным двухвальным узлом, что необходимо, например, при производстве ламелей для покрытий пола. Тонкие пилы малого диаметра позволяют сократить потери древесины в опилки. На станке может быть установлена дополнительная пила для отделения штапика от оконного бруска. Пила вступает в работу автоматически, вместе с направляющей для отвода штапика.
При производстве реечных щитов можно использовать станок с последним пильным шпинделем, который распилит строганную заготовку на рейки нужной толщины. На выходе из станка может быть установлен под любым углом универсальный шпиндель. Его можно использовать для выборки паза, для фрезерования калевки с тыльной стороны под углом к столу или упору, для продольного распиливания и других работ.
Система подачи материала отличается тем, что у верхних и нижних вальцов имеется карданный привод. Это упрощает уход за станком и расширяет возможности его настройки. Подающие вальцы снабжены пневматическим прижимом, что позволяет сохранять постоянным давление на валец при разной толщине заготовок. Каждая секция подающих вальцов регулируется по отдельности. Например, можно увеличить прижим стальных вальцов и уменьшить давление обрезиненных вальцов на выходе. Станки оборудованы подающими вальцами с самоочищающимися зубцами с хромовым покрытием. Нарезка зубцов выполнена так, чтобы предельно снизить их вдавливание в древесину. Подающий валец напротив левого шпинделя находится на телескопической оси, что позволяет быстро и плавно перенастраиваться с узкой заготовки на широкую. При необходимости подающие вальцы могут быть повернуты на нужный угол для надежной подачи заготовок сложного профиля.
В подающем столе имеются пазовые направляющие, через которые может подаваться сжатый воздух. Подача с воздушной подушкой значительно облегчает продвижение материала в станке.
Имеется возможность установки дополнительных подающих роликов между шпинделями для обработки коротких заготовок. Станки могут быть оснащены системой «подвижный шпиндель», которая позволяет строгать в одном потоке доски разной ширины. На приемном столе устанавливается измеритель ширины, который дает команду на установку левого шпинделя на нужный размер строгания.
Возможна обработка с одновременным снятием фасок со всех четырех сторон заготовки. Для каждого шпинделя имеется цифровой указатель радиального и аксиального размеров. Настройка в нужный размер выполняется поворотом рукоятки до получения нужного результата (с точностью до 0,05 мм).
Станки могут быть оснащены системой автоматической настройки всех шпинделей на нужный профиль обработки, задаваемый с пульта управления. Специально для этих целей созданы электронные системы LogoPack и LogoCom. После задания на дисплее всех размеров одним нажатием кнопки выполняются перемещения всех шпинделей. Все установки сохраняются в памяти компьютера и могут быть вызваны в любой момент при обработке нужного профиля.
В России четырехсторонние станки выпускают Боровичский ЗДС (Новгородская область), Ишимбайский завод в Башкирии и «Красный металлист» в Ставрополе. Это 4-6-шпиндельные станки с шириной строгания 160 и 250 мм.
Оригинальный станок марки ПФ4-1 выпускает ставропольский завод «Красный металлист». Это комбинация трех станков: фуговального, рейсмусового и двухстороннего фрезерного. Длина станка всего 1,5 м, на нем можно обрабатывать заготовки минимальной длиной 0,65 м и шириной до 400 мм.
Кроме традиционных поставщиков продольно-фрезерных станков из Германии, на российском рынке в последние годы появились новые игроки: китайский Beaver, японская IIDA, португальская MIDA, High Point из США. Потребитель может найти станки для изготовления разных видов продукции - от тонких погонажных изделий до крупных строительных деталей.