Инвестировать свалку или экономить и получать доход?
В России всего 15% отходов деятельности деревоперерабатывающих предприятий используется для производства экологически чистых видов топлива. Это означает, что большинство компаний ЛПК в буквальном смысле отправляют часть своей прибыли на свалку.
Многие предприятия российского ЛПК относятся к утилизации отходов производства как к неизбежному злу и дополнительной статье расходов. Сучья, кору, опил надо куда-то вывозить и платить за это немалые деньги. В противном случае, при менее ответственном подходе производителя, отходы попросту сохнут или гниют на несанкционированных свалках, ухудшая экологическую обстановку и повышая пожароопасность.
Правда, стоит отметить, что в последние 5−6 лет подход к использованию отходов лесопереработки в нашей стране стал меняться. Формируется совершенно другое к ним отношение: компании, руководители которых умеют считать деньги, предпочитают вкладывать средства в инновационные технологии – строительство котельных, брикетирование и пеллетирование (гранулирование) отходов – и в итоге остаются в выигрыше. Ведь объемы «неликвида» колоссальны – больше половины всей поступающей на производство древесины.
«До 60 % срубленного леса превращается в отходы производства, – говорит менеджер отдела продаж компании "Нестро" Дмитрий Помазунов. – Среди самых рациональных вариантов дальнейшего использования древесных отходов – сжигание их в котлах для получения энергии, переработка в гранулы или брикеты для того же сжигания или последующей продажи».
Сжечь проще всего
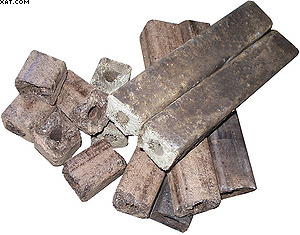
Вариантов утилизации отходов лесопереработки действительно много. Выбор зависит и от масштабов производства, и от качества и количества первоначального сырья – породы обрабатываемой древесины, объемов отходов первичной и вторичной переработки, их состояния, особенностей складирования. Специалисты отмечают, что самый простой способ использования отходов – сжигание в котельных.
«Отходы первичной переработки бревен – влажные опилки – можно весьма эффективно использовать в качестве топлива для котельных, – уверяет заместитель генерального директора ТД "Негоциант-инжиниринг" Олег Федоров. – Горячая вода, полученная таким образом, применяется для отопления производственных помещений и сушильных камер при обработке пиломатериалов и для других технических нужд всего производства».
Специалисты компании «Теплоресурс» подчеркивают, что подобные котельные будут выгодны предприятиям, у которых большие запасы собственного топлива: щепы, коры, опила. Но среди потенциальных покупателей отходов могут быть и компании, находящиеся недалеко от поставщика топлива. Правда, доставка опила дальше 50 км вряд ли принесет производству большую прибыль.
Как правило, заводы – изготовители котлов выпускают оборудование мощностью от 300 кВт до 2,5 мВт. Причем котельную предприятия можно укомплектовать несколькими котлами разной мощности. Чем выше будет мощность котельной, тем выгоднее будет стоимость 1 кВт электроэнергии для лесоперерабатывающего предприятия.
«Котельная, состоящая из двух котлов мощностью 2 мВт и топливного склада, обойдется предприятию примерно в 5 млн руб., – говорит начальник отдела маркетинга компании "Теплоресурс" Дмитрий Жуков. – Такая котельная потребляет около 800 кг отходов в час – это более 570 т в месяц. Конструкции некоторых котлов подходят для сжигания влажной необработанной древесины, так что её не надо предварительно высушивать. Правда, есть одно обязательное условие, которое следует соблюдать в любой котельной: в топку нужно загружать отходы одной фракции, поэтому вначале они должны пройти обработку на рубильных машинах».
По данным компании «Теплоресурс», окупаемость такого проекта для котельной мощностью 4 мВт – 1,5 года при потреблении отходов от собственного деревообрабатывающего производства и более 3 лет, если сырье для котлов покупное.
Конечно, сухие отходы вторичной переработки также можно сжигать в котлах. Но гораздо практичнее их пеллетировать или брикетировать. «Брикеты спрессованных опилок по теплотворности, компактности упаковки, технологичности не уступают цельной древесине, – отмечает Олег Федоров из "Негоциант-инжиниринг". – В России есть регионы, где брикеты практически полностью вытеснили с рынка такой традиционный продукт для топки, как древесный уголь». Успешно конкурируют древесные гранулы и с мазутом.
Биотопливный портал wood-pellets.com приводит близкий к современным реалиям расчет экономической эффективности перевода котельной с мазута на пеллеты. Учитывая стоимость тонны мазута, которая на сегодняшний день колеблется от 8,5 до 13 тыс. руб., экономический эффект от использования пеллет составит до 15 млн руб. в год. Соответственно, весь проект по переводу котельной на новый вид топлива может окупиться за два с небольшим года. И это без учета продажи квот на выбросы в атмосферу. Сегодня стоимость сэкономленной тонны выбросов парниковых газов составляет 10−12 евро. Так что если пересчитать выгоду, которую получит предприятие с учетом возможных продаж «прав на загрязнение», компания сможет выручать за квоты более чем 11 тыс. т в год.
Выгода в гранулах
Правда, чтобы получить подобную выгоду, надо не только дождаться возможности продавать «киотские квоты» на выбросы, но и иметь мини-завод по производству древесных гранул. При этом надо учитывать, что гранулирование и брикетирование – сложные технологии, которые требуют грамотного проектирования целой производственной линии.
«Оборудования на рынке много, но нужно особое внимание уделить проектированию. Если допустить ошибку хоть на одном участке, например недосушить сырье или недобрать мощности, то экономика проекта сильно пострадает. Это проблема практически всех линий, спроектированных в 1990-х», – отмечает Дмитрий Помазунов из компании «Нестро».
Мини-завод для производства пеллет в самой нехитрой комплектации начального уровня стоит от 2,5 млн руб., стоимость же сложных технологических линий составляет десятки миллионов. По данным компаний – поставщиков оборудования, полная линия рубки, сушки и гранулирования обойдется приблизительно в 28−30 млн руб. Условно технологию производства пеллет можно разделить на семь технологических процессов: крупное дробление, сушку, мелкое дробление, смешивание, прессование, охлаждение и вторичную сушку, упаковку. На первом этапе следует подготовить сырье. Отходы производства выгружаются на приемный транспортер, где диагностируются на предмет посторонних включений (например, металла), затем сырье поступает на рубильную машину. Подающие устройства тут могут быть самого разного типа – эстакады, транспортеры, рольганги.
Специалисты компании «Экотехнологии» отмечают, что для измельчения кусковых отходов подходят рубильные машины барабанного либо дискового типа. Их производительность должна быть рассчитана с учетом мощности всей линии и размера отходов, направляемых на переработку. Сегодня на российском рынке богатый выбор подобного оборудования – есть небольшие машины, не требующие устройства под них фундамента (Farmi Forest, Japa), есть средние и большие машины (Europe Chippers, Dutch Dragon, BRUKS, Kesla, Vermeer, Willibald, Jenz, Haas, Musmax, Bandit, Precision, Doppstadt, Petersson, Rotochopper, CBI). Механизмы резания и подачи (в зависимости от потребностей конкретного предприятия) могут быть успешно совмещены в одном корпусе.
Следующий этап – сушка. Как правило, она производится в сушильных камерах барабанного типа: сначала при температуре 250−500°C, а на последней стадии сушки при более низкой – до 110°C. В барабанах камер перемолотая древесина равномерно просушивается до влажности не более 8−12 %. Готовое сырье может выгружаться на автоматизированный склад.
Затем проводится повторное дробление; полученная масса смешивается с паром и водой и подается на пресс-грануляторы (их количество может варьироваться). Стандартный диаметр готовых гранул, как правило, 6 или 8 мм. Позже разогретые гранулы попадают на транспортер, где из них удаляется избыточный пар, и далее на охладительную установку, после чего на упаковку или хранение.
«Для обслуживания такого современного оборудования нужны два – три квалифицированных оператора», – говорит Дмитрий Помазунов. А в компании «Армасис» отмечают, что для надежной работы техники требуются ещё и сложные системы контроля и управления смазки, защиты от перегрева подшипников и от заклинивания пресса, отвода пара, работы главных приводов, блокировок безопасности и т.п.
Перспективный рынок
В России производство пеллет в заметных для рынка объемах наладилось с 2005 года. Конечно, технологии переработки древесных отходов появились гораздо раньше, ещё в 1990-х. Но тогда использовалось старое оборудование, поэтому объем выпуска древесных гранул был небольшим – не более 10 тыс. т в год. Сегодня ситуация сильно изменилась. Так, по данным wood-pellets.com, общий объем производства топливных гранул в России в 2009 году составил более 960 тыс. т. Из них большая часть – до 700 тыс. т – экспортируется в страны ЕС, остальное идет на внутреннее потребление. Рынок топливных гранул, один из немногих российских рынков, стабильно прирастает на 50 % в год, несмотря на финансовые потрясения. Оно и понятно: ведь газ и другие виды топлива доступны предприятиям далеко не во всех регионах, а лес – это тот ресурс, который есть практически везде. Кроме того, Европа была и будет надежным рынком сбыта подобной продукции при её надлежащем качестве и сертифицировании.
«Ежегодно в России вырубается 130 млн м3 древесины, но этот показатель может быть увеличен и до 550 млн м3 (или до 275 млн т). Отходы составят до 40 % от этого объема, или 370 млн м3. Экспорт пеллет, произведенных из этого количества отходов, может принести 6,6 млрд евро в год», – отмечает в одной из своих научных работ заместитель генерального директора ЗАО «Центр «ЭкоРос» доктор биологических наук Евгений Панцхава.
Промышленники не спешат зарабатывать
Несмотря на такие радужные перспективы и, казалось бы, довольно свободную рыночную нишу, многие отечественные лесопромышленные компании просто не могут позволить себе приобрести дорогостоящее оборудование для налаживания выпуска этого перспективного древесного топлива. Те же, у кого есть на это средства, не спешат с инвестициями и дожидаются окончания кризиса. «Спрос на оборудование за последние полгода год упал на 50 %. Многие компании предпочитают сейчас не инвестировать в оборудование, а отложить деньги на черный день – говорит Дмитрий Помазунов из "Нестро". – В такой ситуации без государственных программ переработки отходов и низкосортной древесины не обойтись».
И определенные шаги в этом направлении уже сделаны. Например, в начале октября 2009 года на XI Лесном форуме с презентацией программы использования малоценной древесины и отходов выступил директор Департамента лесного комплекса Архангельской области Николай Кротов. Он отметил, что в области имеются колоссальные ресурсы отходов, которые можно перерабатывать. Так, объем санитарных рубок в 2008 году составил 1,535 млн м3, а объем отходов лесной промышленности, пригодных для переработки, вырос до 5 млн м3. Концепция проекта предусматривает, помимо реконструкции котельных, строительство мини-ТЭЦ, работающих на биотопливе, в Лешуконском районе, а также нескольких заводов по выпуску топливных гранул (пеллет). Стоимость проекта оценивается в 5 млрд руб. Николай Кротов подчеркнул, что в результате реализации этой программы может быть сэкономлено до 1 млн т выбросов парниковых газов за десять лет.
Вывод из всего сказанного очевиден. На отходах можно и нужно зарабатывать. Чтобы завтра получить миллиарды долларов прибыли от продажи «киотских квот» за счет перехода на экологически чистые виды топлива, нужно сегодня вложить значительные средства в программы экологизации и переработки отходов лесной промышленности. Это один из тех немногих рынков, где у России ещё есть шанс занять свою нишу.
Оксана КУРОЧКИНА
Техобзоры по рубительным машинам и мульчерам
Мульчеры и измельчители пней: Мобильные машины специального назначения для измельчения древесины
(журнал «ЛесПромИнформ» № 4 (70) 2010)
Машины для измельчения древесины: Мобильные рубительные машины и измельчители биомассы
(журнал «ЛесПромИнформ» № 3 (69) 2010)
Машины для измельчения древесины: Стационарные рубительные машины и шредеры
журнал «ЛесПромИнформ» № 2 (68) 2010)